Take these precautions to maximize your investment.
04/05/2016
The life expectancy of a mechanical seal is determined by a wide variety of factors, most of which are independent from the seal design. Seal selection, installation technique, equipment startup procedure, operation, seal storage conditions, product variables and seal support systems all play a part in how long a seal will last. Even with so many variables, there are steps users can take to prevent seal failure and increase seal life. Here are four proven methods to ensure any seal operates in peak condition for as long as possible.
1. Choose the Correct Seal
Lack of knowledge and information is an obstacle in the seal selection process. Before deciding on a seal, carefully consider the application and normal operating conditions, as well as any potential off-design usage. For example, selecting a seal to operate in hot water may seem easy because the medium is not particularly difficult. However, if the application is boiler feedwater, this assumption is incorrect. Hot water at temperatures above 190 F is unable to appropriately lubricate and cool the seal faces. The sealing process is then compromised by elevated friction between the two mating faces and will culminate in premature seal failure. To solve this issue, the user must determine if the correct operating parameters are being maintained, then talk with the seal supplier to verify the appropriate American Petroleum Institute (API) flush plan and to choose the correct seal face combination and elastomer materials. Every application has unique requirements, and the proper seals are designed specifically to overcome application challenges.2. Properly Install the Seal
Seal installation should be performed using the steps outlined by the manufacturer and with great care to avoid damaging the delicate seal faces and/or O-rings. Common issues that may occur when installing a seal include forgetting to tighten set screws before removing setting clips, not tightening gland bolts evenly, damaging O-rings, nicking seal faces or incorrectly using the piping connections. Improper seal installation caused by a lack of knowledge is a significant factor in most seal failures. Component seal installation is inherently more prone to installation errors when compared with cartridge seals because of the extra steps and measurements needed. This is why, if possible, users should choose a cartridge seal over a component design. There is already enough to be meticulous about when installing a mechanical seal; why add additional opportunity for mistakes?3. Prevent Excess Heat Generation
Excessive heat generation between seal faces will drastically reduce seal life. Dry-running is the most common example of this issue. It typically occurs when a pump is flooded and/or the seal chamber is incorrectly vented before pump startup. Other situations can also lead to excessive heat generation and dry-running. For example, the seal chamber's pressure can exceed the seal's design parameters during upset conditions. In this situation, contact the seal manufacturer. The seal design may need to be altered if condition fluctuations are an ongoing issue.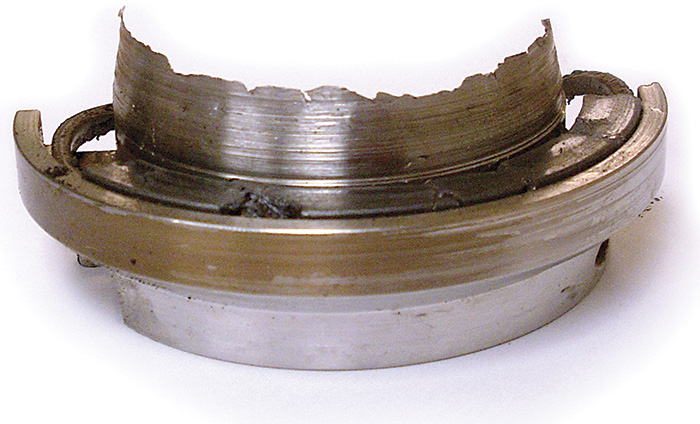
4. Maintain Proper Storage Conditions
Mechanical seals are composed of many unique parts formed from a variety of materials. Because of the diverse properties and the precise, delicate nature of these components, it is important to understand how long a seal can be stored safely without compromising function..jpg)
- Disassemble the seal and store all parts as individual components. Ensure that O-rings are in a relaxed state and meet the appropriate environmental conditions. For a seal that has been in service, clean and dry all components before storage.
- Plug all openings in the seal's gland as well as the unused pump's seal chamber.
- Do not store seal faces (silicon/carbon/tungsten) together in the same packaging. Faces are best separated into individual, protective, bubble-wrapped packages.
- Check O-rings for cracks, cuts and wear, and lubricate O-rings for easier assembly.
- If O-rings are damaged or have experienced compression set, replace them.
- Check mating ring/seal ring for cracks or chips, especially on the sealing faces. If they are damaged, contact the vendor for a replacement.
Mechanical Seal Storage Environmental Conditions:
- Room temperature between 5 C (40 F) and 25 C (80 F) with humidity below 70 percent
- Free of radiation, particularly sunlight
- Free of contamination (pumped products, solvents, oils, copper)
- Free of ozone and ozone-generating devices and equipment