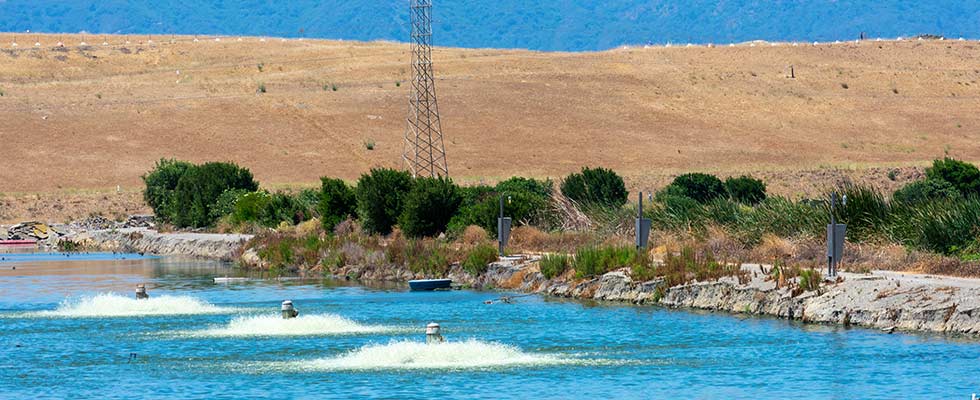
Few motors face harsher daily conditions or play a more critical role in wastewater treatment plant operations than those used to power aerators.
Essential to biological treatment processes, aerator motors are tasked with oxygenating and mixing the corrosive wastewater stored in settling tanks and ponds. Operating continuously at slow speeds, they face severe duty conditions daily that can lead to premature failure.
While an average motor can expect a useful life of 15 years or more, these motors rarely survive half as long. Some must be replaced as often as every two or three years. The more users know about these motors, the better equipped they will be to choose one that lasts longer.
Reliable Operation in Corrosive Conditions
The oxygen provided by aeration motors is needed to help microorganisms digest the organic waste in wastewater. It can be introduced in one of two ways.
In some cases, the motor is attached to a high-pressure blower that pumps air to the bottom of a tank or on submerged diffusers inside a lagoon. The focus here is on a second aeration method. With these applications, a fixed or floating motor is mounted shaft down over the surface of the wastewater. Propellers mounted on the shafts rotate to agitate and oxygenate the wastewater from above.
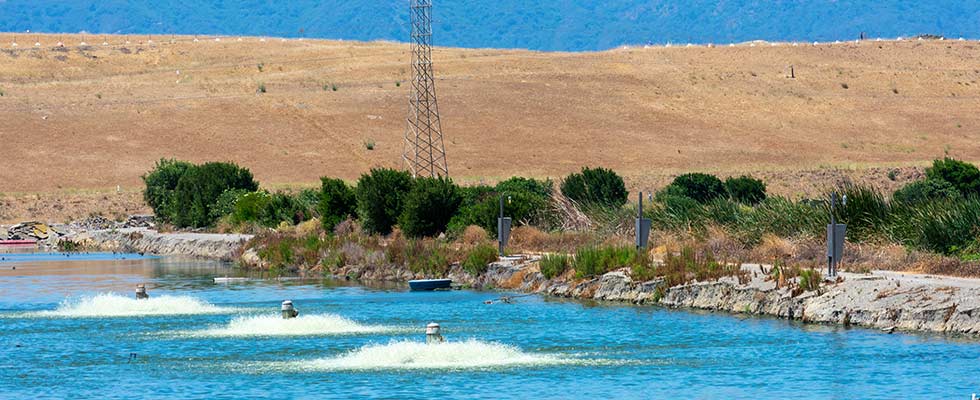
Each is built to an aerator OEM’s specifications. These motors share many similarities, but look a little closer and there are important differences that can impact long-term reliability. Five essential features to look for include:
1. Cast Iron Construction
An aerator motor’s exterior faces a constant risk of coming into contact with highly caustic wastewater. If the drip cover is composed of ordinary carbon steel, it will corrode and virtually dissolve in this unforgiving environment in a short period of time.
To extend their life, aerator motors should be constructed of corrosion-resistant materials. While OEMs may specify either cast iron or stainless steel, experience demonstrates that cast iron delivers the best value. Its durability is comparable to that of stainless steel but requires a lower investment.
2. No Mixing of Dissimilar Metals
When two dissimilar metals, such as carbon steel and stainless steel, are coupled and brought into contact in highly moist environments, galvanic corrosion can occur. To avoid its life-shortening damage, look for motors that use the same metal—preferably cast iron—for all components, including the frame, brackets, conduit box, fan cover guard and drip cover. The motor shaft, external hardware and breather/drains should be stainless steel. For aerator shafts, look for 17-4 pH stainless steel.
Be cautious of motors that combine stainless steel with carbon steel components. Some motors, for example, may use a combination of stainless-steel hardware with epoxy-coated carbon steel spacers between the fan cover guard and drip cover—a combination that will likely end with corrosion. Even the most effective coatings will wear off over time, exposing the drip cover bolt spacers to oxidation and eventual galvanic corrosion.
3. Sealing the Motor From Contaminants
While no coating or sealing is truly permanent, both play an important role in extending an aerator motor’s life. The fact is aerator motors must be shielded from the environment in which they operate. That is best accomplished by protecting the winding, internal parts and any other potential source of entry with a silicone sealant or other special coating. For example, a silicone sealant applied under bracket bolt heads and between the bracket-to-frame fitting surfaces protects the machine’s surface from corrosion and seals that contact point from allowing moisture to enter the motor.
Better aerator motors include a moisture-resistant overcoat in addition to the standard varnish treatment used to protect windings. The conduit box is also a common source of entry and must be completely sealed from the motor. Look for double-gasketed ingress protection code (IP)55-rated conduit boxes made of cast iron. Likewise, the opening where the stator leads exit the frame and enter the motor box should also be sealed to prevent contaminants from entering the inside of the motor. Finally, a potting compound should be used to fully isolate the motor from the conduit box.
The top and bottom of the motor should also have shaft seals to protect the bearings and internal components. A double lip seal, a rotary rubber seal that keeps water from entering the shaft, is one of the most effective ways to prevent entry via the bottom-exiting drive-end shaft. At the top-exiting external fan-driving shaft, a water deflector—a rubber V-ring shaft slinger mounted on the shaft—uses centrifugal force to keep contaminants out.
The paint used in this application should be capable of passing a 500-hour salt spray test in accordance with the American Society of Testing and Materials (ASTM) B117. Paints that do not remain intact after 500 hours of continuous spraying are insufficient for these applications. Request models coated with a two-part epoxy paint system. And finally, to prevent internal condensation, which may reduce motor life, consider models that add an internal strip space heater that maintains internal temperatures above the ambient dew point. This will help prevent internal condensation when not aerating, which may reduce motor life.
4. Low Maintenance Requirements
When properly sealed, a motor may be difficult to disassemble. The locations on flotation cells in a settling pond can make them difficult to access as well. The reality is, even the best-sealed motors can withstand only so much methane, chemicals and other corrosive elements. Within seven years, windings can end up pitted and a replacement motor is needed.
Given these realities, end users may purposely seek to minimize the maintenance requirements for these motors. For example, relubrication intervals may be scheduled beyond the motor manufacturer’s recommendations.
5. Bearings That Can Take Thrust
Bearings play a vital role in aerator motor reliability. As the aerator’s propeller spins, it creates a thrust on the motor that, in turn, puts pressure on its bearings. Were the motor not secured, it would take off like a boat motor. The bearings must, therefore, be sized to take the thrust without consuming excessive grease or overheating. That requires a delicate balance, especially when the motor is expected to operate for long intervals between relubrication.
One solution that accomplishes this goal involves designing the upper guide bearing to include a small cavity above the bearing for capturing grease and a lower bearing shield to keep the grease in the bearing as long as possible.
In addition, because axial and radial thrusts are taken at the bottom of the motor, these models will use either a 3000 series double-row angular contact bearing or back-to-back 7000 series angular contact bearings on the drive end, which allows for more grease storage.
Sourcing the Aerator
The shafts used in aerator motors are highly customized in how they mount to an aerator and propeller. In other words, they are propriety to the aerator OEM.
Rather than working with a distributor, replacement aerator motors should be sourced from the OEM, which can provide further guidance on selecting the model that will deliver long, reliable operation for the application.