These engineered machined products can help increase a facility’s return on investment.
SIMS Pump Valve Company Inc.
10/04/2016
As industry invests tremendous amounts of effort to reduce energy consumption, the U.S. Department of Energy (DOE) and the Hydraulic Institute (HI) have focused on improving efficiencies of pumps, motors and pump systems. One way end users can reduce energy consumption—in some cases, by 10 percent or more—is the use of highly engineered structural-composite pumps and impellers. Upgrading existing pumps with qualified structural-composite components can reduce energy use and improve return on investment (ROI) in five key ways.
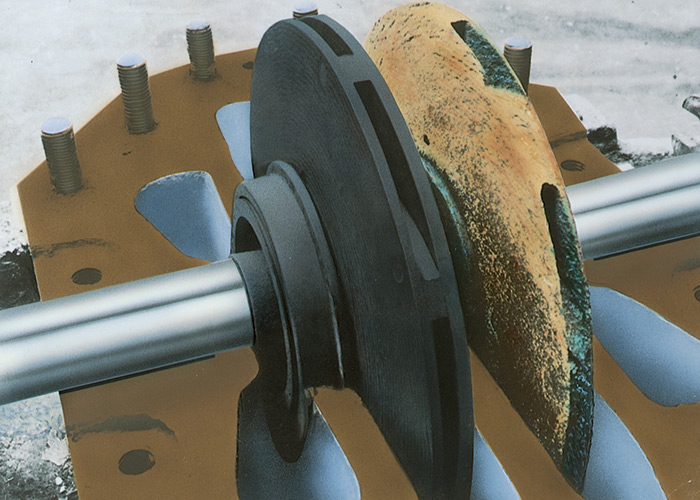
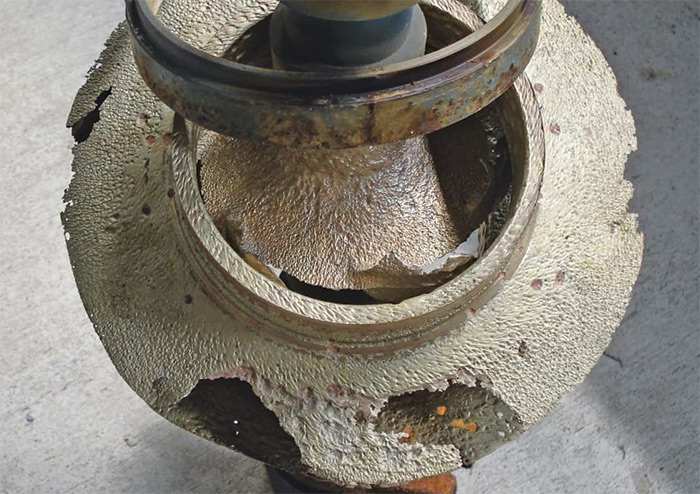
1. Composite materials extend pump life because they are inert, corrosion-resistant and withstand cavitation better than metallics such as bronze.
An evaluation of the performance curve of any pump will show a huge drop in efficiency once a metallic impeller begins to wear, cavitate and/or corrode. Even if the starting efficiency of a pump appears sufficient when a pump is new, tests demonstrate rapid deterioration of efficiency and performance as a pump continues to operate more inefficiently. Engineered structural-composite impellers and rings can help prevent these heavy losses of efficiency and performance. Pump inefficiency contributes heavily to increasing energy, maintenance and repair costs. In some cases, structural composites can provide five to seven times the lifespan of metallic pumps and impellers in corrosive applications.2. Structural composites provide a reduction in energy costs through pump optimization.
In many cases, a facility purchases a pump for one specific performance, but once the pump is put into service, system requirements cause it to operate at another point entirely different from the pump’s original design point. When a pump operates away from the original design point or best efficiency point (BEP), problems occur, including higher loading; excessive noise and vibration of the pump; shaft oscillation; cavitation; and premature wear and failure of the mechanical seals, bearings, rings, sleeves and impellers. In extreme cases, the pump shaft will break right behind the impeller from the excessive radial forces that occur when a pump operates away from the original design point. Operating a pump away from the BEP has a detrimental effect on efficiency and performance, and it wastes energy and money. Operating the pump in this way also severely reduces pump life.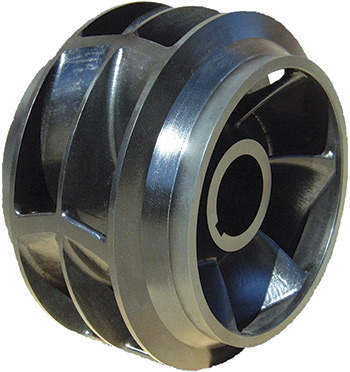
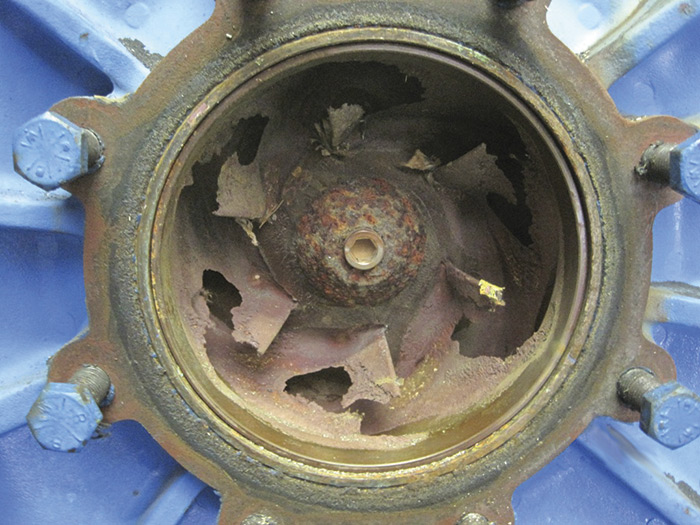
3. Completely machined structural-composite impellers experience less vibration and lower radial and axial movement as a result of better mechanical and hydraulic balance.
Engineered structural-composite impellers are completely machined from a center position out of a solid block of structural composite on both the inside and the outside. As a result, the vanes are all equally spaced and the impellers are well-balanced and remain well-balanced for the life of the pump, leading to increased longevity and enhanced performance as a result of less vibration. A very similar type of technology has been employed for propeller design and manufacture. Propellers that are machined on five-axis machining centers not only produce less vibration, but they also pay for themselves in fuel savings.4. Composite impellers are lightweight and reduce shaft deflection.
Structural-composite impellers and casing rings are only 15 percent the weight of traditional metallic materials. The lower weight reduces startup load and shaft deflection, which allows the rotating element to run with tighter clearances between the rings and the impeller. The tighter ring clearance reduces leakage, and the reduction in shaft deflection enables bearings, sleeves, mechanical seals and rings to last much longer, which saves on repair and maintenance costs.5. Composite impellers and casing rings reduce leakage and prevent pump “wash-out.”
Because of the excellent lubrication qualities of many structural-composite materials and because of the low coefficient of friction, the ring clearances in operation are less than metallic rings and allow less leakage between the impeller casing rings and the impeller wear ring. The smoother surfaces and less leakage between the casing rings and impeller wear ring result in a 2 to 3 percent increase in efficiency. Additionally, the structural-composite rings seal against the pump casing similar to a gasket, preventing the fluid from wearing or corroding the landing areas under the casing rings.Estimated Operational Savings
Because of the many benefits listed above, structural-composite impellers and casing rings can outlast metallic impellers and ring sets, especially in corrosive environments. Table 1 demonstrates the estimated operational savings that structural-composite materials can provide.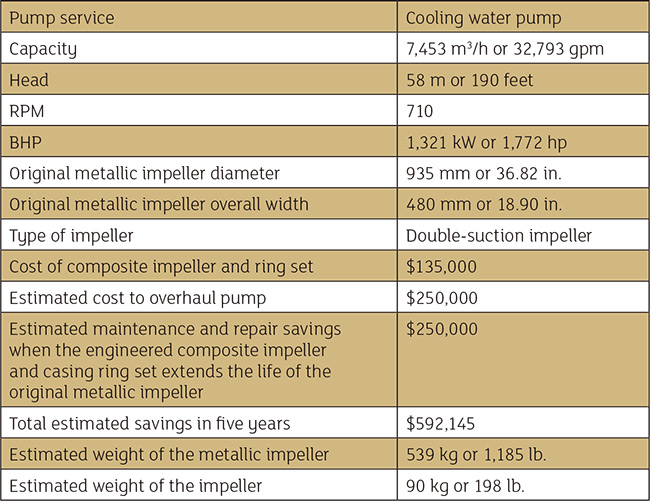