Outside lubrication experts help improve protocols and minimize downtime.
08/19/2014
Few industries can tolerate the unscheduled downtime of critical equipment. In refinery operations, it can have particularly serious implications. For an operation that runs 24 hours per day year-round, the losses—in both production and profitability—can be staggering. Rotating equipment—pumps, motors, compressors and pillow block bearings—represents a key refinery component that, without proper planning, can become a refinery’s Achilles heel. This article presents six tips that help prevent unscheduled downtime because of rotating equipment failure.
1. Invest in the Right Equipment
Flexibility is the key. What may have been the right equipment in the past may not be the right equipment today. Many facilities were originally designed to handle a certain fluid and have pumps and peripheral systems designed to accommodate that fluid. Today, different feedstocks in a wide array of viscosities offer price and profitability advantages. A refinery must accommodate the diversity.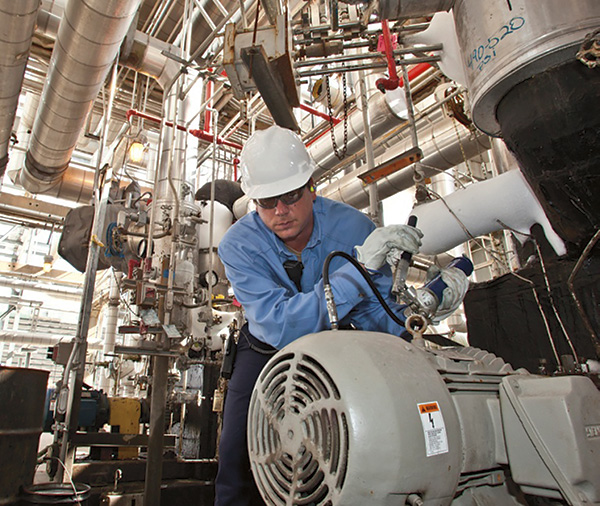
2. Decontaminate Lubricants
Every piece of rotating equipment in a refinery needs lubrication. At some point, flushing, varnish removal, reservoir maintenance and fluid replacement will be required. Particle contamination is the biggest threat to rotating equipment lubrication and a leading cause of bearing failure. A refinery’s maintenance staff is responsible for its lubrication program, but these specialists also have other duties. A lubrication program can divert time and money from operations. Successful refineries often partner with a firm specializing in lubrication maintenance. External lubrication experts have experience that allows them to anticipate issues before they occur.3. Be Honest with Outside Experts
Any partnership with an external maintenance firm should be based on candor and trust—like that of a patient and doctor. A lubrication expert can only help a refinery if the facility’s maintenance personnel willingly shares information on current and past equipment operations.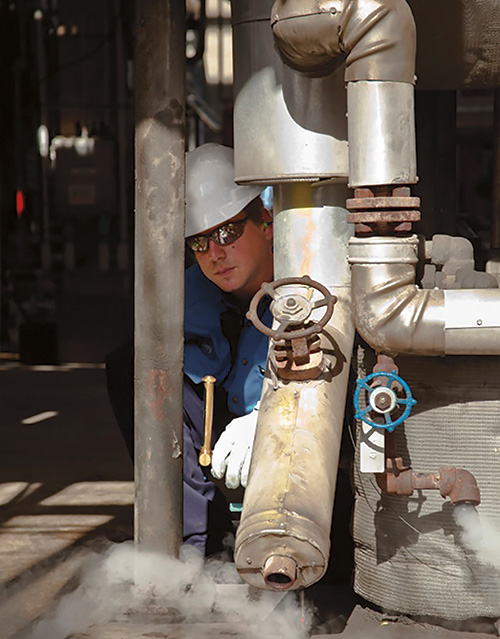
4. Think Outside the Box
Facility maintenance managers often understand their lubricant needs. However, an expert may recommend new lubricants that can help optimize rotating equipment operation. Changing to oil mist lubrication is an example. Oil mist is not new. The lubrication method has been around for nearly half a century. Newer oil mist systems have replaced their older, more wasteful ancestors, delivering precise lubrication that extends bearing life compared with alternative lubrication methods. Refinery owners and personnel should consider outside suggestions. At the same time, they should pay more attention to the ordering, storage, handling, disposal and recycling of the facility’s lubricants. Often overlooked, improper storage and handling can introduce contaminants to the lubrication system that may cause facility-wide problems.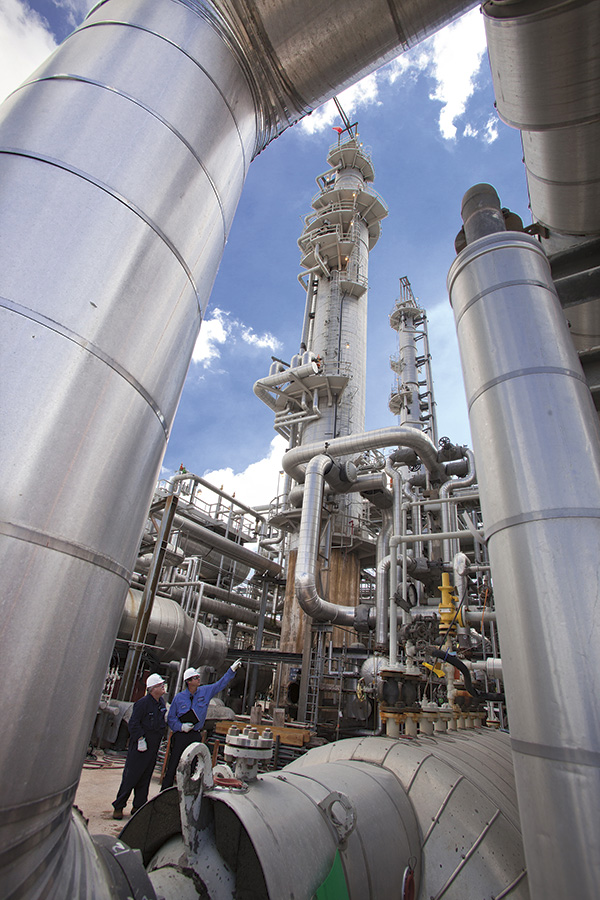