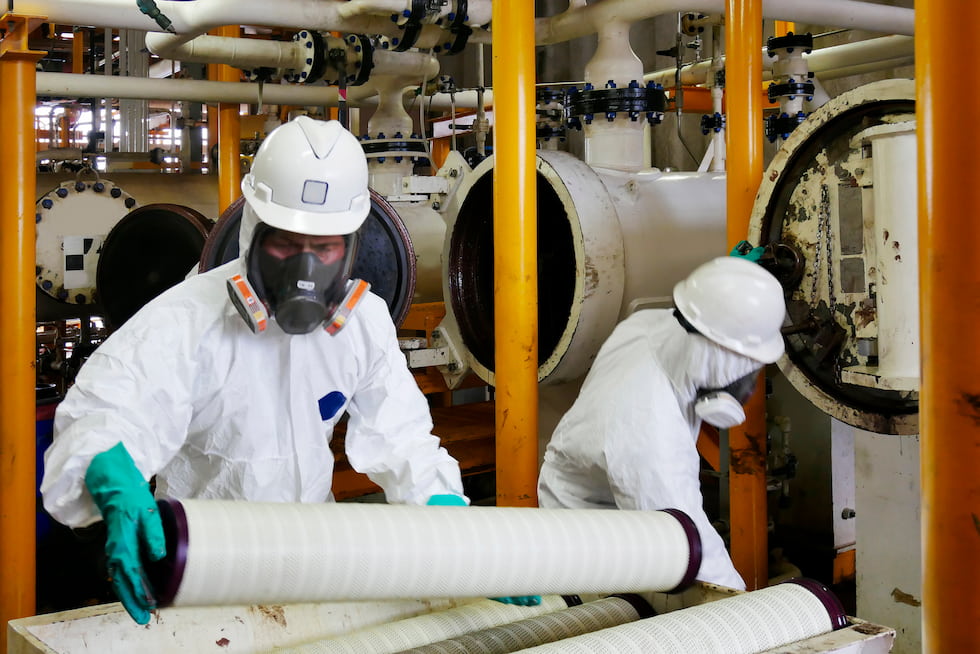
Liquid filtration is a vital part of all oil and gas processing systems. Liquid filtration works to remove a variety of different types and sizes of contaminants within a medium. These sediments and other materials should be removed during processing to prevent them from causing buildup issues or other contamination problems later down the line.
When it comes to using a filtration system during oil or gas processing, common mistakes are made that may
limit the effectiveness of the filter itself. This is a problem for different reasons, but mostly because it increases the
chance of efficiency reduction and solvent contamination.
1. Mistake: Failing to Remove Contaminants in Inlet Feeds
One common mistake made by those in the gas and oil processing industry is not removing contaminants within inlet feeds.
Once plants have a comprehensive and thorough understanding of their medium—be it gas or oil—and the contaminants present within that medium, they can better address the proper steps to take to remove those contaminants. It is vital that impurities are removed from the material coming in for processing, as their presence can cause many problems within the system, having a negative effect on the quality of the gas or oil being produced.
The best way to keep contaminants from entering the plant system from inlet feeds is to use a filtration process on all oil or gas coming into the system. Filters can eliminate a number of contaminants within a medium, and different filters have varying effects on the oil or gas being processed.
When used and maintained correctly, filters are an asset for many plant systems, often lowering operations costs as well as keeping the gas or oil plant and its many processes stable and running smoothly. When it comes to capturing contaminants within inlet feeds, the hardest contaminant to remove is aerosols. For trapping those types of contaminants, consider a particle filter with microfiber submicron coelescers (MSCs).
2. Mistake: Improper Contamination Control During Processing
Another common mistake is processing with subpar contaminant control, which can be detrimental to the plant’s success and has a significant effect on the final state of the processed product. Contamination issues can vary, and the first step that should be taken to prevent this contamination is using a filtration system.
Too often, processing plants are reluctant to or do not use a filtration process. However, installing a filter within a plant’s processing system can improve the state of the end product by removing any contaminants present, as well as eliminating many common issues that arise when filters are not used.
Filters are designed to remove solid material and other contaminants from a liquid or gas stream. Filters can be a great option for oil and gas processing plants. They easily remove contaminants from the gas or oil being processed, which purifies the end product and helps ensure that equipment does not become clogged or damaged. Lack of filtration can lead to equipment failure and higher maintenance costs. It is also important to use a good filtration system, along with feed and effluent separation systems, to properly remove any contaminants that may be present.
3. Mistake: Incorrect Equipment for the Application
For those installing or deciding to use a filter system, take a step back and assess exactly what type of system will be required. This is especially important for large-scale or low-budget systems, as using the correct filter equipment can save time and cost. Not thoroughly understanding the application may cause problems with equipment down the line and can result in costly repairs. Those with a low budget may not get the proper equipment needed in an effort to save cost; however, this tactic can be more costly long-term and have a negative impact on the product.
For example, using an automatic filter with metal-based media in amine units may seem like the proper protocol for that system. However, because of the types of contaminants found in amine units (often gel-like material), automatic filters tend to perform less effectively.
Cleaning and removing contaminants from the filter become an issue, which means the filter will require service more often, while also decreasing the efficiency of the filter as the contaminants cannot be completely removed.
4. Mistake: Insufficient Seals in the Filter System
Once filter systems have been installed within a processing plant, parts should be checked to ensure all parts are correct and working properly. One thing that needs to be checked is the seals. While this aspect of a system is often overlooked, tight seals can make a difference in the efficiency of the system. Sealing surfaces are typically at the meeting point of the internal element and the vessel. These seals work to keep contaminated flow from the flow of filtered material.
Gaskets and O-rings within the system should be checked to ensure they are the correct size. This equipment also needs to be replaced on a regular basis to ensure their seal. Any other sealing surfaces should be checked and maintained as needed.
5. Mistake: Wrong Internal Pieces & Media
Though it may seem obvious, incorrect internal pieces within a filter system are overlooked regularly. Pieces may be wrong due to a mistake or miscommunication with filter system suppliers, or more often, pieces are chosen due to a misunderstanding of the contaminants needing to be removed from the material flow. If incorrect pieces are chosen for the filter system, the system may not work optimally, and certain types of contaminants within the medium may not be removed by the filter. This is why it is vital to choose filter systems and components based on the specific contaminants to be removed.
6. Mistake: Incompatible Parts
Another mistake commonly made within oil and gas processing is using parts that are incompatible with one another. The thermal, chemical and mechanical needs of the media should be taken into consideration when deciding what filter parts should be used.
7. Mistake: Little or No Maintenance
Within any filtration system, regular maintenance will be a requirement. Maintaining a filter system is vital to the resulting performance. The internal aspects of the filter should be checked regularly and thoroughly to ensure they are being maintained properly. Maintaining and replacing parts of the filter system when needed is important for keeping the filter running correctly. Without maintenance, filters can become clogged, seals become loosened, and the results can affect production and decrease the quality of the end product.
When it comes to refining either gas or oil through a filtration process, many plants forget what is most important. Ensuring a system has the correct parts and maintaining proper materials and maintenance practices can help the system run smoothly for the long-term. Using the right filter system has not only the ability to increase system efficiency but can also result in a higher quality final product.