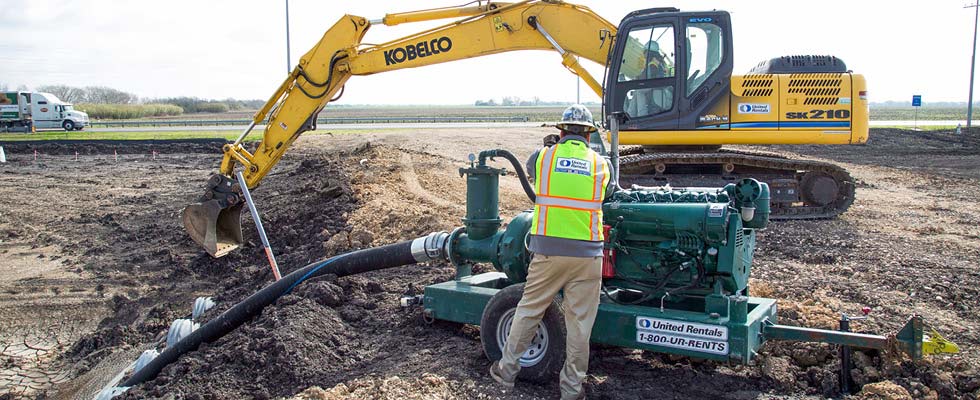
Most construction projects that involve excavation require the removal of groundwater or surface water. Without proper dewatering, the subgrade could become unstable, making it difficult to install a solid foundation or causing damage to work already performed.
Wet or muddy ground can pose a slipping hazard, threaten the integrity of building materials such as lumber and cause equipment and metal tools to rust. Areas of flooding can limit crew access or halt work altogether. Contractors who know how to efficiently remove water from a jobsite have a higher likelihood of keeping a project on schedule and budget.
Avoiding dewatering problems begins with understanding the characteristics of the site and choosing the most appropriate pump type and size. There are many pumps available that can handle the large-scale movement of liquids, and no one-size-fits-all solutions.
Following these eight steps can help ensure the selection of an effective dewatering system design.

1. Consider the Water Source
The pump needed to dewater a site that gets 2 or 3 inches of standing water after a heavy rain is likely to be different in type and size from the one required when water is constantly seeping into an excavation or running along the ground due to a high water table. A more powerful pump designed for long-term use may be required for continual operation.
2. Check the Solids Content
The water on a construction site will never be completely clear, but the type and amount of debris and solids it carries will vary greatly from location to location.
The solids content influences the type of pump needed. For example, a trash pump, or solids handling pump, can generally move liquids with a solids concentration of 3% to 5%, with solids up to 3 inches in diameter. A sludge pump is designed to move liquids with a solids concentration of up to 6% to 7%. Using the wrong pump to move water with a heavy concentration of sludge or other materials will likely result in system failure.
3. Determine the Flow Rate Required
The maximum flow rate needed is one of the critical pieces of data necessary to properly size a pump. The gallons per minute or cubic meters per minute of water entering the site will determine the required flow rate and pump capacity.
When it comes to maintaining the outward flow of water, the closer a pump can be located to the water source, the better. If the distance between pump and water is greater than 100 feet, the dewatering system may require larger piping or conduit.
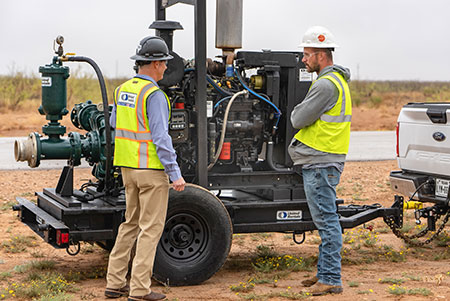
4. Measure the pH
One factor often overlooked in dewatering pump selection is the pH of the water. Water that is acidic or basic can damage pumps and cause project delays. Many factors can affect the pH of groundwater and surface runoff. Groundwater may contain dissolved minerals from rocks or contaminants in the surface layers of soil. Rainwater can pick up airborne contaminants from nearby industries.
When the pH is outside the normal range, pumps made with corrosion-resistant materials are the ideal choice. They are less likely to break down as a result of issues such as seal failure and will perform better long term.
5. Measure the Pumping Distance
Pumping over large distances typically requires a pump with more horsepower, as well as larger hoses or pipes to reduce friction losses. Depending on the distance, multiple pumps may be necessary.
6. Calculate the NPSH
The net positive suction head (NPSH) also influences the required pump size, but contractors sometimes fail to factor it in.
NPSH is the difference between the pressure available at the suction port of the pump (NPSHa) and the pressure required to keep the pump operating properly (NPSHr). The NPSH calculation factors in the temperature and vapor pressure of the water being moved, the atmospheric pressure and friction losses. Using a pump with insufficient NPSH can lead to cavitation and pump breakdown.
7. Calculate the Required Static Suction Lift
The vertical lift from the lowest point of the water being pumped to the center or eye of the impeller is known as the static suction lift. The greater the suction lift, the lower the pump flow capacity.
A good rule of thumb is that at sea level, a properly operating vacuum-assisted priming pump can perform a static lift of 28 feet to the eye of the impeller. For every 1,000 feet of elevation, deduct one foot of priming capability.
A typical 6-inch, diesel-powered vacuum-assisted pump is designed to lift fluid 28 vertical feet to the impeller. If the required suction lift is greater than 25 feet, a different type of pump, such as a submersible pump, may be needed.
8. Rely on Expert Advice
When it comes to construction site dewatering, there is a lot riding on proper pump selection. If the dewatering system fails or a pump breaks down, water can start collecting on the site, slowing operations or bringing them to a stop.
Pump selection is more complicated than it may seem. A temporary equipment vendor with deep knowledge of pumps and experience in designing dewatering systems for a variety of jobsites can help contractors perform the necessary measurements and calculations, choose an appropriate pump and design a system that does the job efficiently and at the lowest cost. If the pump will need to handle both high and low flows, for example, the vendor may suggest using two pumps instead of one, with the second pump kicking in only when the flow is high, instead of oversizing the pump, which wastes energy and increases costs.