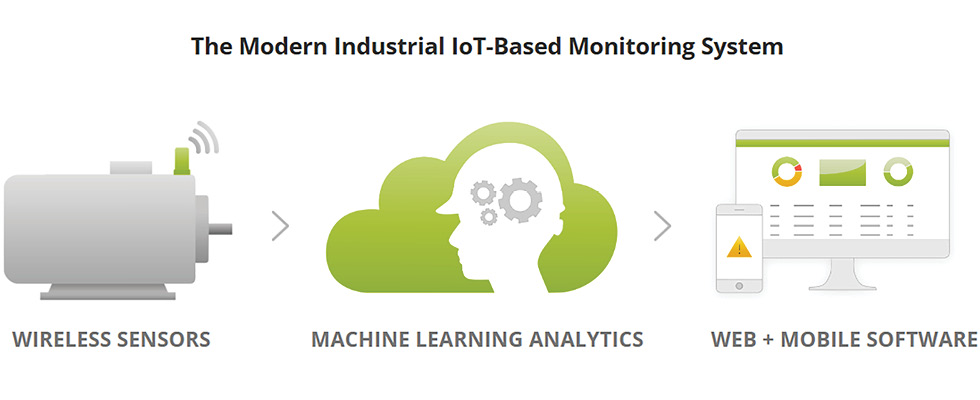
Industrial pumps are the backbone of countless operations across various industries. They are essential in processes requiring fluid movement, including water treatment, chemical processing, oil and gas extraction and pharmaceutical manufacturing. Pumps ensure the efficient and reliable transfer of liquids, making them indispensable in maintaining operational continuity and productivity.
When pumps experience issues such as cavitation, seal leaks, misalignment, bearing failures or impeller wear, it can lead to significant disruptions. In critical water and wastewater treatment operations, any deviation in pump performance can compromise the effectiveness of the process, leading to environmental and public health risks.
A malfunctioning pump in a pharmaceutical plant could compromise the entire production batch, leading to substantial financial losses and regulatory penalties. To mitigate these risks, regular condition monitoring and predictive maintenance are vital to detect and address issues before they escalate. By doing so, companies can ensure reliable pump operation and safeguard the integrity of their processes.
Modern Solutions in Pump Monitoring
Monitoring industrial pumps presents challenges due to their widespread presence and sometimes remote locations within facilities. For water and wastewater utilities, remote pump stations are often spread across wide geographies with little to no on-site staff to monitor the machinery on a frequent basis. These hurdles have traditionally prevented continuous condition monitoring and predictive maintenance for pumps across industries.
The advent of industrial Internet of Things (IIoT) technologies is helping industries overcome these challenges, enabling effective predictive maintenance of pumps and other critical equipment. IIoT-based monitoring systems use state-of-the-art sensors that transmit data wirelessly for real-time analysis. These systems enable comprehensive condition monitoring for pumps by integrating various types of sensor data, including vibration, ultrasound, motor current and differential pressure.
With the popularity of variable frequency drives (VFDs), many pumps now operate at variable speeds and loads. Some advanced systems are able to monitor the motor’s running speed—with a magnetic flux sensor, for instance—in order to correlate with vibration and temperature trends for more accurate machine health insights. The most cutting-edge solutions go a step further to provide automated analytics and fault diagnostics to support reliability and maintenance programs. This approach ensures precise, reliable data collection while providing a holistic picture of pump health and facilitating proactive maintenance to maximize uptime.
This article will explore two case studies from real users of advanced pump monitoring systems, demonstrating the transformative impact of wireless monitoring technologies. It will look at real-world examples of fault detection and the seamless integration of these technologies into traditional maintenance practices. These case studies will illustrate how IIoT-based condition monitoring empowers facility managers and reliability professionals to make informed decisions, mitigate risks and maintain the integrity of critical infrastructure.
Case Study 1
The first case study is from a water treatment plant in California, where the benefits of a wireless asset monitoring system were realized when a developing defect was detected in a critical water pump. After several months of monitoring, the system flagged a progressive vibration trend primarily in the axial direction with a prominent 1x component, which is often indicative of misalignment issues.
An automated email alert was sent to the maintenance team, enabling them to schedule an immediate inspection. Upon investigation, site personnel confirmed the motor and pump shafts were improperly aligned due to a loose coupling in between.
The early detection provided by the wireless monitoring system allowed the site team to take proactive measures before a major failure occurred. They performed a realignment during a scheduled shutdown period, thus preventing potential operational disruptions and minimizing repair expenses. In this case, the water utility company spent nearly 86% less than the amount they typically had allocated for pump repairs. This incident highlighted the advantages of using advanced monitoring technologies to maintain the reliability and efficiency of essential infrastructure.
Case Study 2
Another case study takes place at a gold mine and processing facility in Nevada, where an IIoT-based vibration monitoring system was employed to monitor critical rotating equipment. Due to the rugged, remote nature of the site, as well as the long distances between critical machinery, wireless monitoring was the obvious solution for the site’s asset reliability program.
Soon after installation, the monitoring system identified a raised noise floor in the vibration spectrum of the barren booster pump, a clear indication of cavitation. Cavitation is a critical issue in pump systems caused as a result of energy released when vapor bubbles collapse, leading to operational inefficiencies and potential equipment damage. This prompted an inspection of the pump and the two feeder pumps supplying it.
The investigation revealed impeller wear in both feeder pumps, which was causing the cavitation. At the time, the system was only installed on the downstream barren booster pump, yet the data helped uncover the deterioration of the upstream feeder pumps without directly monitoring them.
The deployment of the IIoT-based vibration monitoring system proved instrumental in maintaining the health of critical equipment at the gold mine. Without advanced warning, the cavitation and impeller wear would have gone unnoticed for several months and could have potentially led to a sudden failure and loss of production. The system’s ability to provide real-time data and alerts enabled quick diagnosis and resolution of the pump cavitation, demonstrating the value of advanced monitoring technologies in the most challenging of industrial environments.
Effective monitoring of industrial pumps is essential for ensuring operational reliability and efficiency across various industries. Common issues like cavitation, bearing defects and seal leaks can impact pump performance if not addressed promptly. The case studies presented highlight the effectiveness of IIoT-based monitoring in identifying and resolving potential pump faults before they escalate.
Advanced monitoring solutions provide real-time insights, allowing remote monitoring of pump health from any location with internet access. Continuous 24/7 surveillance ensures constant oversight and timely responses to emerging issues. Additionally, wireless monitoring systems are typically more cost-effective than hardwired alternatives, eliminating the need for extensive wiring and infrastructure. This cost-effectiveness makes a strong case for implementing continuous condition monitoring of pumps and other critical machinery.
By leveraging the capabilities of IIoT technologies, such as wireless sensors and predictive analytics, organizations can shift toward proactive maintenance strategies, optimizing equipment reliability and enhancing operational efficiency across industries.