
The United States is the world’s largest producer of natural gas. Production levels in 2020 were approximately 33.5 trillion cubic feet and came from the two mainstays in the industry, the Appalachian region and West Texas. Companies in this industry rely upon supervisory control and data acquisition (SCADA) systems to help communicate important information, monitor equipment, improve efficiencies and avoid unplanned downtime.
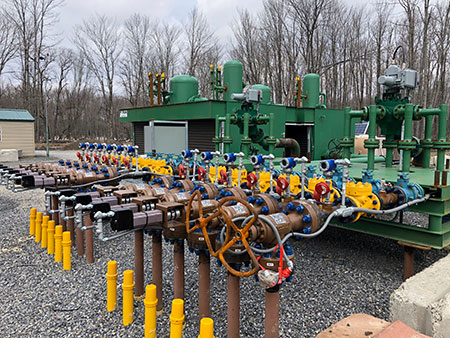
SCADA System & the Natural Gas Industry
Accurate, real-time data is key to succeeding in the oil and gas industry. Engineers need operational data from the field to calibrate equipment, schedule maintenance activities and coordinate with third-party logistics to keep the flow of product moving. SCADA systems help the oil and gas industry improve operations by managing equipment remotely and overseeing critical processes. It gives operators more control over equipment and processes, including controllers, input/output devices, communication equipment and systems as a whole. It typically involves several subsystems that manage assets dispersed in remote locations, often with limited connectivity.
Management uses information analyzed by SCADA systems to calculate production values, generate trends for decision-making and project company profits. Environmental, health and safety (EHS) aand regulatory compliance personnel are constantly on the lookout for potential environmental issues and pipeline integrity.
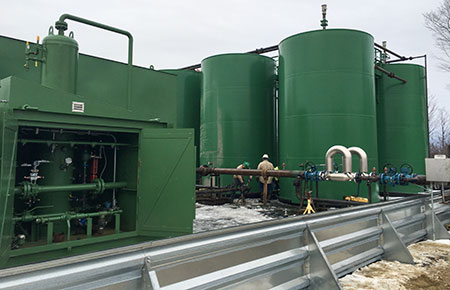
Case Study: Houston
A natural gas producer headquartered in Houston, Texas, is the exploration and production segment of a large national gas company. The company has evolved amid periods of changing regulation, supply scarcity and industry consolidation and is now playing a role in the industry’s rebirth. It has set specific technology goals of streamlining and standardizing the flow of information from its pads and wells into its back office information systems, and to make this information more visible and available to operations and engineering teams as well as other stakeholders.
To achieve these goals, the natural gas producer, with operations that span a large geographic region of northwest Pennsylvania and require a large team of operators to support its assets, depends on a robust SCADA system. In 2009, they standardized the company on a single solution integrated with remote alarm notification software. Monitoring gas production and processing equipment is critical to ensuring ongoing and efficient operations. The SCADA system monitors well pressures; gas measurement data including flow rates, pressures and temperatures; tank volume levels; and gas processing units, which takes the produced gas and fluid stream from the well, heats it and separates the water from the gas, sending the water to the production tanks and gas to the sales line.
To accommodate the various production processing methods on the company’s well pads, its automation and SCADA team designed a comprehensive template in their SCADA system to standardize the collection of data from wells, tanks, meters and transducers.
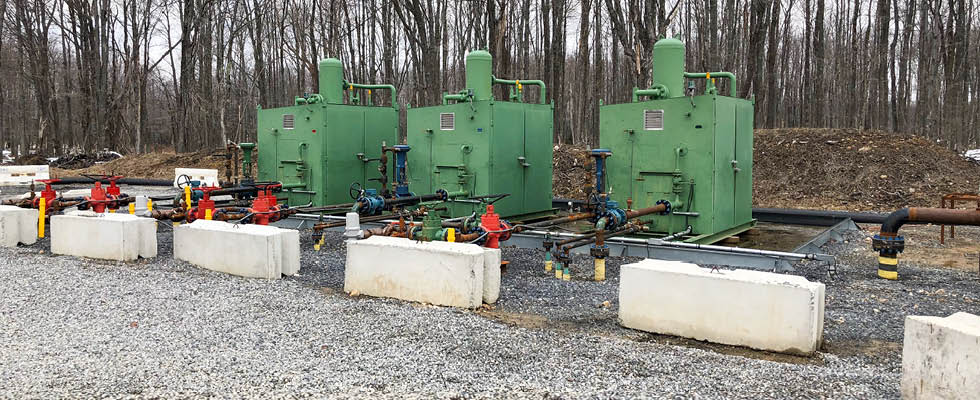
Utilizing consistent nomenclature standards for the SCADA objects and attributes was key for integrating the information collected from the system platform into the remote alarm notification system, other business applications and reporting solutions. The alarm subscription and labeling methodology in the alarm software appealed to the company because it aligned with the asset model in its SCADA system. In previous versions, tags had to be manually exported from the SCADA system and imported into the software. This caused interruptions to the alarm system each time new tags were added, and there were limitations to send alarm notifications to specific groups of operators. The SCADA system had to be designed to support the alarm software, whereas the newest software version is flexible and can support any configuration.
The alarm subscription feature allows the company to write specific alarm queries and tag them with labels to group alarms by facilities, geographic regions and other criteria. The alarm notification policy feature provides the capability to assign rules to initiate callout notifications and route the resulting alarms to contacts associated with specific labels.
When a contact is set up in the system, applying the appropriate labels makes it easy to ensure the contact is receiving the proper set of alarms from the system.
The remote alarm notification software lets the company quickly organize alarm notifications based on alarm types, severity, worker roles or other chosen criteria. The notification software supports numerous alarm notification methods such as SMS, mobile app and email notifiers.
It is imperative there is virtually no downtime associated with the system. The software’s redundancy features provide the functionality for the company to set up a hot standby backup system in their secondary data center. When there is a disruption in the primary data center or maintenance on the primary software environment, the backup system can quickly be switched to active mode without a disruption in alarm notifications being sent to operations staff or contractors.