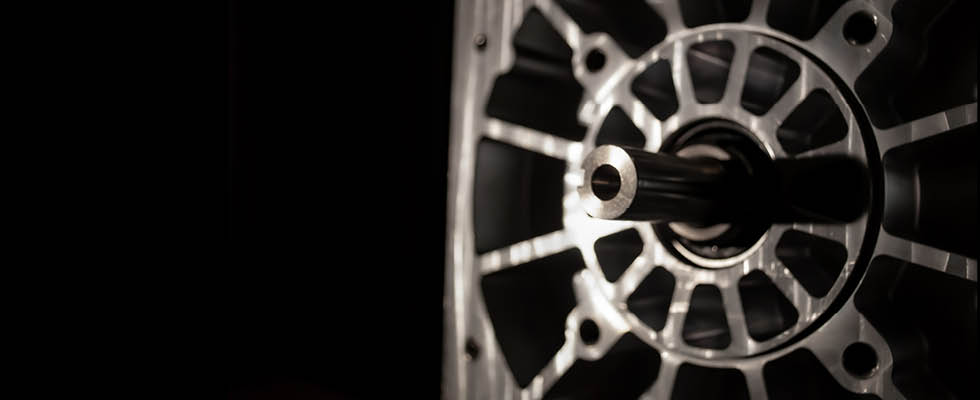
High-efficiency electric motors are now being created that use static forces, instead of magnetic fields, to create torque. Founders of this technology learned of Ben Franklin’s work in the late 1700s with electrostatic motors and decided to embark on a challenge to bring the technology back to life. Franklin’s original design relied on spokes of glass rods and brass thimbles interacting with positively and negatively charged Leyden jars arranged opposite of one another. The machine was only able to reach speeds of 10 to 15 revolutions per minute (rpm), making it unable to be used for any practical application. After almost 300 years of being known as nothing more than a founding father’s science experiment, electrostatic motors are now capable of replacing traditional electromagnetic motors in a wide array of industrial applications.
Modern electrostatic motors function by applying medium voltages to sets of printed circuit board plates that make the machine’s rotors and stators. Printed circuit boards are remarkably ubiquitous, making them easy to source and low cost to manufacture. Each trace on the rotor is charged with alternating positive and negative voltages that create an electric field. The stator functions similarly, but with three phase A, B and C voltages. By applying medium voltage sine waves around the stator, a rotating electric field is created, pulling the rotor along.
The number of rotors and stators is one factor in determining the torque output of the motor. With a larger stack of plates, an electrostatic motor can create higher levels of torque output. Changing the voltage also alters torque output, making the machine capable of generating torque levels necessary for a wide range of applications, all without a gearbox. The electrostatic motor technology is suited to deliver full torque and efficiency in low speed applications, thus eliminating gearboxes and active cooling. The resulting systems are simpler to design, install and maintain.
In engineering, it is often emphasized that systems are built around motors rather than the other way around. Electromagnetic motors are designed for high-speed, low-torque operations, which may not be suitable for certain stationary industrial applications. In scenarios such as powering a conveyor belt that only needs to move at a few feet per second, a motor operating at its designed speed of 1,800 rpm (for example) would need to be paired with a gearbox to adjust its speed accordingly. With the implementation of an electrostatic motor, users can customize a motor to suit their specific application without the need to add on additional components for functionality.
Traditional motors use electric current passing through copper windings to create magnetic fields and produce torque. Electrostatic motors, on the other hand, use voltage to generate electric fields, which then produce torque. Electrostatic machines pass orders of magnitude lower current through the machine to reduce heat generation and therefore offer higher energy efficiency. The newer electrostatic motors also leverage a multiplicative effect that comes from the use of a dielectric fluid. The liquid fills the volume between the plates, insulating the stators from the rotors and acting to increase the strength of the electric fields on the plates. With a liquid that acts as an insulator, electrostatic motors can operate at higher voltages than they would in air and achieve maximum efficiency. The dielectric fluid is developed with a team of chemists testing different fluid formulas and tailoring different blends for different application needs. A unique control system for the electrostatic motors is also being developed in order to create the high levels of voltage necessary to operate the machine.
The absence of magnetism in this motor eliminates the need for rare earth metals, a group of elements that can be costly and environmentally damaging to mine and refine, while also having a costly and narrow supply chain base. Substituting rare earth metals in motors represents a substantial step toward enhancing sustainability and improving the overall supply chain for motor technology. Electrostatic motors also are not heavily reliant on copper, reducing the total copper needed per motor by at least 90%. With these two core raw materials eliminated (permanent magnets) or heavily reduced (copper), there is a clear potential for electrostatic motors to become extremely low cost to produce and thus help consumers save on both the upfront cost for electric motors as well as the ongoing electricity costs from higher energy efficiency.
The compact size and lightweight design of these electrostatic motors make them ideal for space-constrained environments and applications requiring precise control. With further research and development, electrostatic motors show promise in powering larger applications like wind turbines and electric vehicles. In wind turbines, electrostatic motors can capture more wind energy due to their high torque and efficiency, contributing to increased renewable energy generation.
Ultimately, work on these motors not only resurrects an ancient concept but also pioneers a much-needed transformative shift in motor technology. By revisiting and innovating upon Benjamin Franklin’s initial experiments, a future where electric motors are more sustainable, efficient and versatile is possible. Modern electrostatic motors showcase a new era of cost efficiency and reduced energy consumption.
As these electrostatic motors continue to be refined for a broader spectrum of applications, their impact could change energy efficiency standards across multiple industries. This technology could push the industry toward a more sustainable and energy-efficient future.