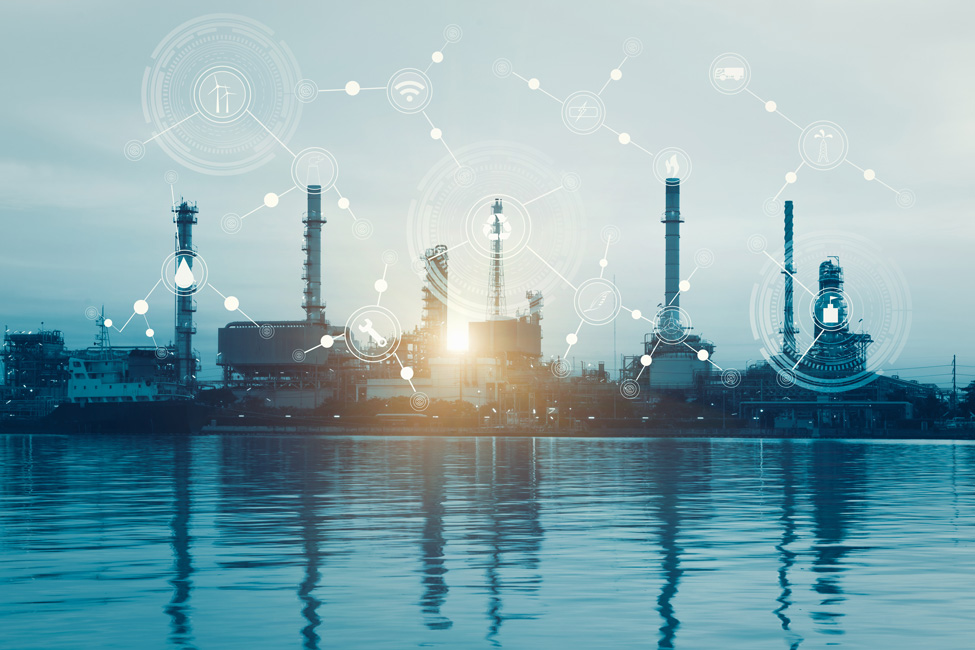
Effective pressure and temperature measurement of process media ensures efficiently run facilities. A key component in high-quality measurement is the implementation of smart pressure and temperature transmitters with leading-edge functions for high-speed network communication.
Historically, transmitters in industrial and process environments would rely on an analog output variant to send pressure ratings or temperature information further upstream to a programmable logic controller (PLC) or process automation controller (PAC). A common output type is 0-10 volts of direct current (VDC). This communication type is simple to implement, readings are easy to take and 0-10 VDC input devices are mainstream and embedded in many electronic devices. However, when it comes to durability, the preferred choice among automation specialists is a milliamp (mA) signal, typically 4-20 mA output. Again, the installation architecture’s advantage is that it can travel long distances without causing signal degradation and is robust against electrical noise (often induced by surrounding electric equipment).
While considering more integrated internet of things (IoT) communications, digital platforms will need to be considered for full integration of field devices. Of the options available, the fieldbus network with the longest legacy and open infrastructure is Modbus RS485 (Modbus protocol defines the messaging structure used in the data exchange, while RS485 defines the physical level of electrical signals and wiring between the host and the field devices). There are many advantages of this protocol, including wide global acceptance with low cost of implementation, serial communication tolerant to electrical noise, cables that run up to 1,200 meters or4,000 feet, capacity for multiple field devices on a single rung (up to 32 nodes can be connected on one network or up to 127 devices on a multi-drop network), and the offer of fast data transmission speed.
Another popular fieldbus network and one installed across the process world is HART (Highway Addressable Remote Transducer). This is a hybrid analog and digital open protocol that can communicate over existing 4-20 mA communication platforms, allowing the user to upgrade to a “smart” protocol without the cost of rewiring. Other advantages of implementing HART include:
- simplicity with programming and network setup
- speeds up the time for troubleshooting between identifying and solving issues
- real-time detection of connection problems in device and/or process
- uses remote diagnostics to reduce unnecessary field checks
- improves regulatory compliance as sophisticated diagnostics increase the safety integrity level (SIL) with automatic safety shutdown
- seamless and continuous integration, allowing existing process plants to be continuously expanded
Once the communication network has been determined, there is a plethora of application opportunities for these smart transmitters to be integrated into. Industry, location and ambient conditions of the installation will often dictate the type of communication output that is selected.
For newer green field process installations, the default network is usually HART. However, often missed installations are in remote areas. For example, in the oil and gas market, well pads, pump jacks and compression stations (to name a few) are not considered in the overall networking scheme, as they typically operate as decentralized systems. These installations are typically interfacing both analog and digital signals at remote sites and communicating through remote terminal units (RTUs) by radio, telephone lines, cellular signals, microwave and satellite to a central controller, commonly a supervisory control and data acquisition (SCADA) station. Remote locations with challenging environments have the potential for transient electrical noise and lengthy distances, the legacy network most often requested is Modbus RS485. With the loss of implementation and some allowable field devices, once this network is installed, especially in a remote location, it is difficult to convince a field operator to upgrade.
Upstream oil and gas facilities can generate their power through renewable energy such as solar, wind or geothermal. These sources can often power small e-houses but have limited power supply, therefore the power consumption of installed devices needs to be considered. Standard smart transmitters with 4-20 mA analog signal outputs or even the RS485 models with digital protocols rely on large amounts of power consumption. In these installations, the better choice is a low voltage 1 to 5 VDC analog output. This will ensure continuity for the remote location while adhering to the power consumption requirements.
A classic application, found in both commercial and process segments, is a heat exchanger. A heat exchanger is a device that allows heat from a fluid (or gas) to pass to a second fluid (or gas) without the two having to mix. This equipment, with age or misapplication, can suffer from leaks through cracking or blockages, and clogs due to an irregular maintenance schedule. If these issues arise, the heat exchanger will not properly perform and result in inferior quality product, unregulated climate control or personal harm. The installation of a smart differential pressure transmitter will allow for proper monitoring of the inbound and outbound pressure and display critical differences while sending the analog or digital information upstream for proper processing and control.