Q. What is the allowable pump/motor operating speed range when a variable frequency drive (VFD) is used? A. VFDs are used to vary the speed of the pump in order to optimize system efficiency and/or process control. Adjusting the frequency applied to the motor allows the speed of the motor and pump to be changed, usually to a lower speed than the base revolutions per minute (rpm) stated on the motor nameplate or lower than the speed the pump would operate with utility power. Operating a pump at reduced speeds is usually acceptable within a specified range, but operators must consider certain mechanical design features such as bearing lubrication and natural frequency interactions. Anyone considering reduced-speed operation should consult the pump original equipment manufacturer (OEM). Operating the motor at lower speeds usually results in a reduction of the motor cooling system capability, because motor cooling fans produce less airflow over the motor at reduced speeds. Operators must ensure that the motor can withstand the added heat that is created by operating below base speed. The operating speed range should be defined and applied to motor capability requirements. In many cases, the pump and motor can be sped up to 10 percent above base speed without adverse effect, but operators should first consult the OEM to evaluate electrical and mechanical design considerations. In rotodynamic pump applications, the load is governed by the pump affinity laws, which state that a change in torque is proportional to the square of the speed change and that change in horsepower is proportional to the cube of the speed change. This type of load is known as a variable torque load (VT). Most motors are capable of operating 10 times slower than the nameplate rpm of the motor (10-to-1 speed range, or turndown) when driving a rotodynamic pump. Positive displacement pumps present higher relative loads at reduced speeds, which will have a more significant impact on the motor and drive. Most motors can operate with a 2-to-1 turndown speed range with this type of load, which is commonly considered a constant torque (CT) load. For best results, define the load type and operating speed range in advance. Provide this information to the pump, motor and drive manufacturers and discuss it with them to ensure the motor and drive selection is the best fit for the pumping application. For more information on VFDs, refer to HI's guidebook Variable Frequency Drives: Guidelines for Application, Installation, and Troubleshooting. Q. What type of motor and motor enclosures are recommended for wastewater application pumps? A. In wastewater applications, the pump driver can be a motor- or engine-driven unit. The most common pump driver in a wastewater treatment plant is an electric-powered induction motor. Engine-driven pumps are typically used in emergency or standby service when electrical power supply is not available. Synchronous motors can also be used, but they are normally provided for kilowatt requirements above 750 (horsepower requirements above 1,000).
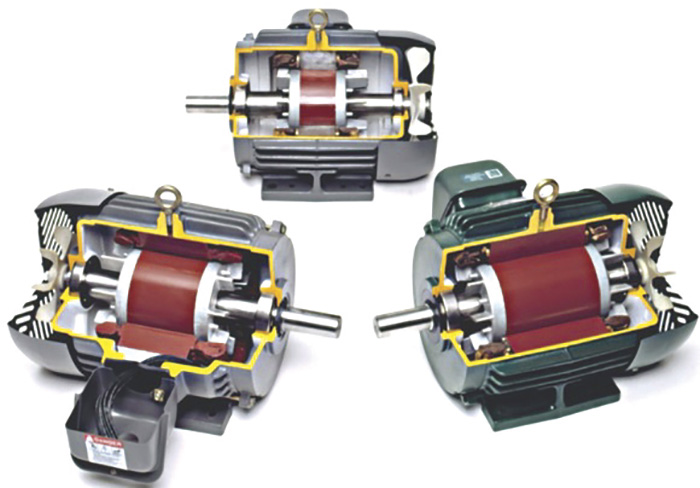