Manufacturers in a wide range of process industries from petrochemical to oil and gas distribution, power generation and water utilities, are adopting new maintenance techniques to improve their bottom lines. These new strategies, built around tracking the conditions of equipment in real time, are helping asset owners boost reliability, availability and throughput while better managing costs, safety considerations and regulatory compliance throughout an asset’s life. Some of the most dramatic benefits are realized by companies adopting predictive maintenance strategies, in which service providers can track asset health by collecting multiple data sets, including real-time and historical sensor data. Service providers analyze the data by looking at rates of change or comparing values to moving averages or norms. They create algorithms from the data collected on assets and predict the future health of equipment based on comparisons to similar pieces of equipment. Additionally, service providers can use advanced pattern recognition modeling tools to analyze data and detect anomalies in critical assets early in the performance degradation process. These predictive maintenance strategies play a key role in optimizing maintenance schedules, avoiding production shutdowns, reducing capital costs and extending asset life cycles.
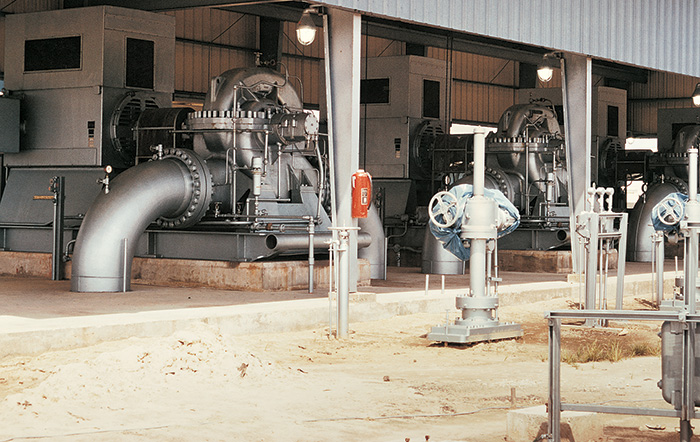