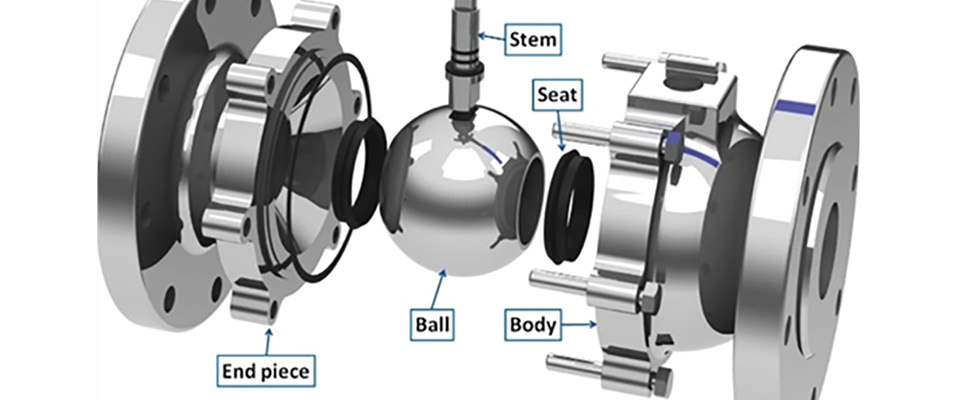
In the rapidly evolving landscape of the oil and gas industry, the need for robust and efficient components is paramount. For example, carbon graphite and its applications in industrial ball valves have altered aspects of oil and gas production facilities, enhancing both safety and efficiency.
For reference, a ball valve is a shutoff valve that controls the flow of a liquid or gas. It does this by utilizing a ball with a cylindrical hole in the middle. In the open position, the hole in the ball valve is aligned with the pipe to allow the media to flow through. In the closed position, the valve is rotated 90 degrees so the ball valve hole is perpendicular to the pipe path, preventing any media from flowing. Two seats cup the ball along the path of the pipe, creating a seal and preventing leakage around the ball.
Many of these ball valves have Teflon or metallic valve seats using outside lubrication like grease. When the media running through the ball valves is a harsh chemical or is at a high temperature, grease is not an option and engineered plastics will deform; therefore, carbon graphite is used. Carbon graphite’s self-lubricating properties, chemical resistance and high-temperature capabilities make it an ideal material for ball valve seats in these conditions. In addition to carbon graphite’s resilience in severe service, it is an impervious material, ensuring a leak-free design.
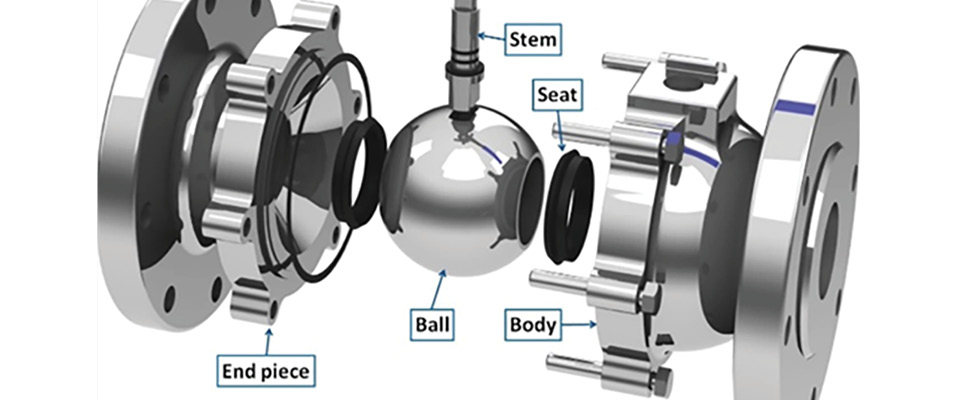
An example of high-temperature ball valves would be fire-safe ball valves used in oil and gas production facilities. Fire suppression systems use a network of fire-safe valves to move and disperse water as needed during a firefight. Fire-safe valves are widely used in the oil and gas industry because of their flammable nature. Refineries, tankers and rigs are equipped with a variety of fire-resistant valves that are subject to a rigorous qualification process. Each valve meets specific requirements set forth by the American Petroleum Institute (API), a trade association representing more than 650 companies involved in the refining, production and distribution of crude oil. API 607 is a standard that specifically focuses on the fire safety testing of quarter-turn valves with soft-seated (non-metal) components.
This particular standard mandates these valves must be capable of withstanding a specific level of pressure when exposed to temperatures ranging from 1,400 F to 1,800 F, which closely replicates real-life fire conditions. It is due to such demanding conditions that the utilization of advanced materials like carbon graphite becomes important in the manufacturing of fire-safe valves.
Carbon graphite is an alternative to plastic ball valve seats, as it remains unaffected by high temperatures, whereas plastic softens at approximately 350 F. Specifically designed graphite grades have been created to endure the extreme temperatures demanded by API 607, surpassing the performance of most other materials.
Despite the elevated temperatures, carbon graphite maintains its self-lubricating capability and structural integrity. The versatility of carbon graphite is not solely attributed to its resistance to high temperatures. Additionally, carbon graphite exhibits chemical inertness, enabling it to function effectively in highly corrosive environments without undergoing chemical degradation. Carbon graphite ball valve seats are frequently utilized in corrosive environments, such as chemical processing and distribution, due to these properties. Additionally, carbon graphite exhibits remarkable compressive strength.
Carbon graphite valve seats typically require a shrink-fit installation into a metal retaining ring and must be held in compression to ensure optimal performance. The interaction between the carbon graphite and the metal housing, along with the resulting compressional forces, enable the spherical sealing face to maintain its shape effectively during operation and withstand higher radial loads.
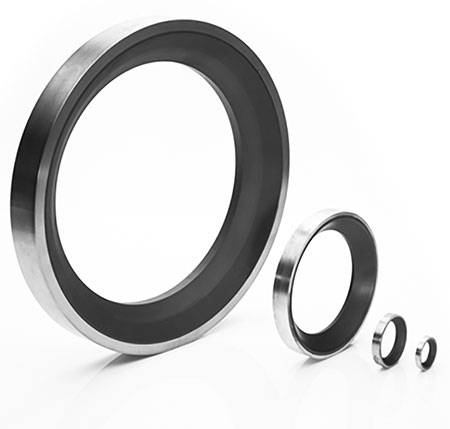
This interference also guarantees the containment of carbon graphite within the metal housing during thermal expansion at elevated temperatures. Given that the retaining ring and the ball are frequently composed of identical materials, the seat and the ball will likewise expand and contract at an equivalent rate as temperature fluctuations occur. This enables the ball and the seat to uphold a uniform sealing surface without any leakage—even under high-temperature conditions. During the assembly process, it is crucial to perform the final machining to guarantee the flawless alignment of the spherical sealing face with the ball. This meticulous step ensures a secure and leak-proof fit between the seat and the retaining ring. The outcome is a highly reliable ball valve that can effectively operate in environments where other ball valve seats may encounter difficulties.
Carbon graphite manufacturers continuously aim to enhance their materials, enabling valve designers to create solutions for increasingly challenging environments. To remain updated on these advancements, it is recommended to directly engage with a carbon graphite manufacturer.