These recommendations can help end users prevent equipment degradation in pulp and paper applications.
07/08/2015
Market forces and increasing regulatory demands have exerted considerable pressures on pulp and paper operations. As a result, mills are striving to achieve maximized equipment uptime and optimized plant productivity by focusing on process efficiency and machine reliability. Turning to critical components that will influence the efficiency and reliability of pumps and machinery, pulp and paper plants are realizing the vital part rolling element bearings play in the papermaking process.
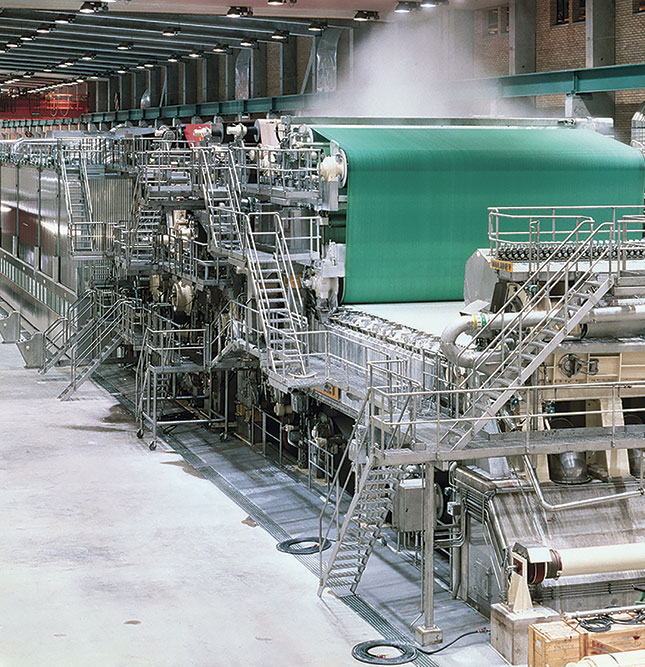
Abrasive Wear
Abrasive wear is caused by the ingress of debris particles or inadequate lubrication. The nature of the foreign particles (hardness and size) and the severity of the contamination will influence the degree of material removal caused by abrasive wear. This wear results in removal of the original bearing surfaces and, at a macro level, a change to the internal bearing geometry. Increased friction and elevated operating temperatures usually accompany abrasive wear, resulting in bearing failure from surface initiated fatigue. Similarly, inadequate lubrication can result in asperity contact between rolling elements and raceways.
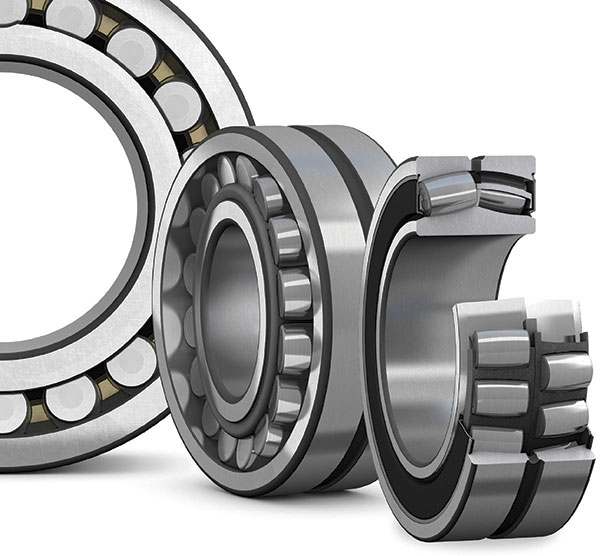