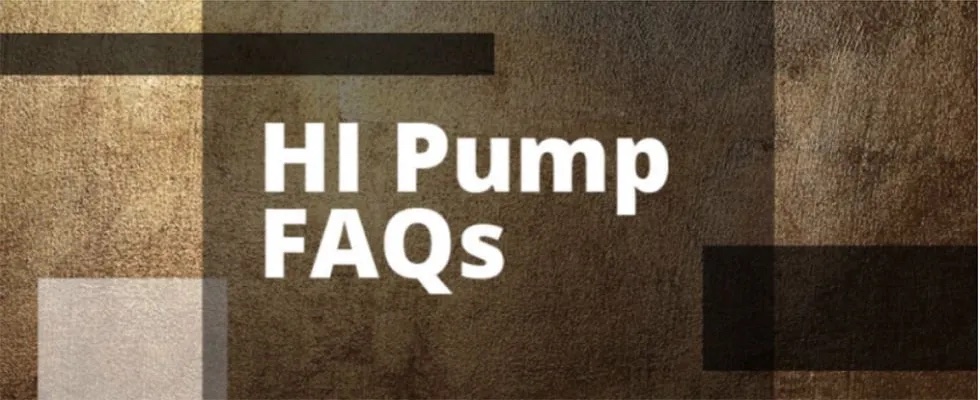
Mechanical seals are a technology that dynamically control leakage along a rotating shaft. In pumps they are primarily responsible for preventing the fluid or medium being pumped from leaking out along the rotating shaft, and they are generally mounted in a gland between a pump shaft and impeller. Proper selection, installation, support systems and pump operation are vital to their performance and longevity.
A basic mechanical seal and its primary components are illustrated in Image 1. The red section represents the fluid in the area of the seal chamber that is being sealed due to contact between the rotating face and the stationary face that are in axial contact. In an overhung pump, the fluid being sealed is at the back of the impeller, and the pressure in the gland depends heavily on the pump’s suction pressure and other design and application considerations. A mechanical seal also has secondary seals that provide static sealing (which are O-rings in Image 1) and provide sealing along the rotating face and the shaft and between the stationary face and the gland. The last item to note is that there are metal drive and spring components that attach the rotating face to the shaft and provide a closing force between the seal faces.
While it may seem counterintuitive, mechanical seals require a minuscule gap (sometimes as small as 1 micron) between the rotating and stationary faces, allowing just enough fluid to escape to form a lubricating film at the interface. This film allows the seal faces to slide against each other without being in full contact, known as dry running. Dry running can cause rapid catastrophic failure in a seal due to friction. Conversely, too large of a sealing gap will result in excessive fluid escaping through the seal gap. When a seal is functioning properly, the fluid that does escape usually exits in a vapor form due to the intense pressure in the seal gap and therefore does not damage the seal or pump.
There are a large variety of seal designs to meet the wide-ranging application requirements in pumping systems. A categorization of seal types include: single or dual, pusher or bellows, balanced or unbalanced, stationary or rotating spring, inside or outside mounted, split face and component or cartridge types.
The purpose and reason for choosing one design over another is application specific. For more information on the design, application, selection, function and maintenance of mechanical seals, refer to Hydraulic Institute Guidebook Mechanical Seals for Pumps at pumps.org and training course Mechanical Operating Principles, Types and Classifications at training.pumps.org.