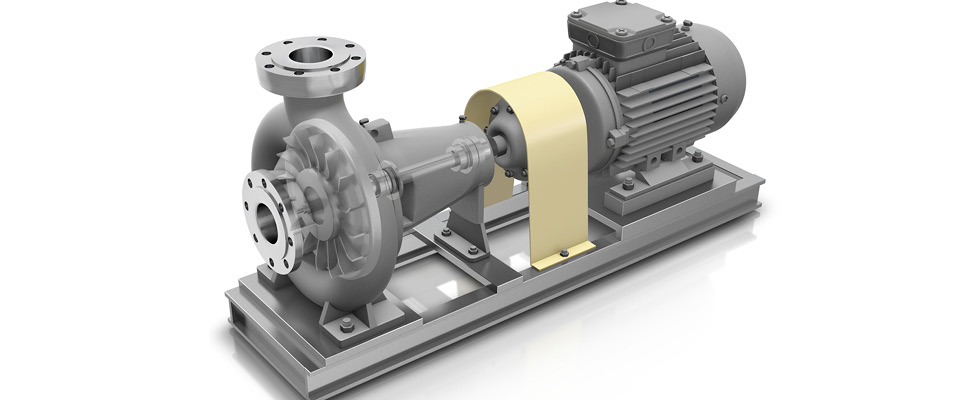
Significant amounts of energy are consumed by pumps, motors and their surrounding systems. As energy usage continues to increase, it is critical to sustainably manage these systems for the benefit of both present and future generations. For example, water and wastewater treatment plants provide people all over the world with clean water for agricultural and industrial production. As global demand within these sectors continues to grow, the devices powering them need to become more efficient, last longer and be easier to maintain. This article will explore strategies for using bearings in pumps and motors more sustainably by focusing on three categories: system performance and efficiency, system life and maintenance/downtime costs.
Improving System Performance & Efficiency
In basic terms, motor and pump efficiency can be described as how well electrical energy is converted into mechanical and hydraulic energy. High-quality ball and roller bearings that feature honed raceways, optimized geometries and premium quality bearing steels can help improve these efficiencies by generating less heat, extending the life of the grease, reducing energy consumption and allowing for higher possible speeds. In addition, analyzing the type of bearing selected can also offer performance benefits.
For example, some applications that historically used matched tapered roller bearings may now be suitable for modern angular contact ball bearings that generate less friction and deliver higher speed ratings. Bearing manufacturers can assist in selecting bearings for optimal performance and efficiency benefits.
An important area of efficiency improvement within electric motors—albeit not directly attributable to bearings—is the efficiency improvements offered by variable frequency drives (VFDs). While these VFDs can deliver as much as 30% higher motor efficiency, they often induce shaft voltages within the motor that discharge through the bearings in the form of stray currents. With conventional bearing designs, these stray currents can damage the bearing, leading to premature failure. Current-insulated bearings—such as bearings featuring ceramic-coated rings or hybrid ceramic bearings whose rolling elements are made of ceramic material instead of bearing steel—can be used in electric motors to reduce this risk due to the ceramic material’s nonconductive properties.
Improving System Life
In addition to improving operational efficiency, selecting the right bearing can improve the life of the system. A bearing may fail early if it is either under- or overengineered for an application, as either condition can negatively impact the life of the bearing.
In addition to bearing selection, a qualified bearing manufacturer can offer engineering support—such as bearing clearance calculation assistance, performance simulations and failure analysis—to help continuously improve the bearing application. For example, pairs of single-row angular contact ball bearings, which are often found in centrifugal and other types of pumps, should have optimized axial clearance for the application to extend life and reduce the risk of early failure in the bearing or seal. Properly setting the axial clearance for the application helps to ensure optimal pressure distribution in the bearings and surrounding elements. Excess axial clearance can lead to shaft deflection, which may cause the mechanical seal to fail due to wear. Moreover, excessive axial clearance can lead to early bearing failure resulting from rolling element skidding or a failed cage on the unloaded bearing.
As mentioned, hybrid ceramic bearings can be used for their electrical resistance benefits to increase the efficiency of electric motors controlled by VFDs. Additionally, the ceramic rolling elements inside hybrid ceramic bearings have significantly reduced mass and greater stiffness when compared to traditional bearing steel. These properties improve friction, running accuracy and operating temperatures in the bearing and lubricant, leading to longer life in more demanding electric motor and pump applications.
Bearings with special coatings can also be used to improve life in various applications in and around pumps and motors. Ceramic coatings can provide electrical current insulation, often more economically than hybrid ceramic solutions. Black oxide coatings can protect against failures from roller skidding or white etch cracking, and zinc-nickel-based coatings can protect against corrosion from moisture—all of which can lead to early bearing failure.
Reducing Maintenance & Downtime Costs
Like any other component with moving parts, a bearing will eventually need maintenance. Sustainably managing the bearing’s life cycle involves mitigating unplanned downtime through condition monitoring and proper bearing lubrication and, when downtime is required, reducing its total cost.
Unplanned downtime caused by bearing failure can be reduced by utilizing condition monitoring as part of a predictive maintenance program to repair or replace components before they reach critical failure. Condition monitoring devices—available with cloud-based connectivity for easy installation and setup—measure vibration and temperature of the bearing and surrounding elements to alert the user of changes in the bearing’s condition.
Insufficient or excessive lubrication is one of the most frequent causes of bearing failure. Compared to traditional lubrication devices, such as manually operated grease guns, automatic lubrication systems can help conserve bearing lubricant consumption by precisely controlling bearing relubrication intervals and volumes. By optimizing grease delivery amounts, the overall lubricant consumption within a facility is more sustainably managed. These systems can deliver the right amount of grease at the right time, extending the life of the bearings and reducing overall costs.
Because manual bearing lubrication is often difficult to prioritize within maintenance schedules, it is a task that is often overlooked, which further contributes to decreased bearing life. Looking toward the future, developments in artificial intelligence (AI) and machine learning will allow for intelligent automatic lubrication systems that can combine bearing condition monitoring with historical data analysis to optimize for the current operating conditions.
When downtime is required, its total cost is most impacted by its duration, since longer downtimes result in more lost production. Machinery components, such as pump drive shafts or impeller shafts, are often supported by cylindrical or spherical mounted roller bearings. To reduce the cost impact of downtime related to these bearings, they can be replaced with “split” versions that are often quicker to install in the application. Split cylindrical and split spherical roller bearings are manufactured in halves, resulting in a quick mounting process that avoids disturbing other machinery elements. Utilizing split bearings can reduce the total overall duration and cost of the downtime by up to 60%.
If the downtime involves repairing machinery off-site, such as servicing a motor in a rebuild shop, it is especially important for bearing efficiency and life that the machines are properly aligned before they resume operation. Even minimal alignment deviations can lead to increased friction and vibration, as well as reduced bearing life from damage caused by the misalignment. Advanced laser alignment guidance tools are available to ensure precise and accurate alignment, providing overall energy and cost savings in the application.
Sustainable Motion
Using bearings sustainably involves selecting the optimal bearing for the application, continuous improvement using the latest design features and applying the many solutions available for reducing maintenance and downtime costs. Advanced bearing technologies such as precision raceway honing, coatings and cloud-based condition monitoring—alongside the many other sustainability initiatives present throughout manufacturing—will continue to push the industry toward more sustainable motion.