What are the benefits of multistage pumps?
Multistage pumps use multiple impellers plus diffusing element stages for developing higher head through the series addition of head from one stage to the next. Types of multistage pumps include the between bearing types, which consist of the axially split BB3 and the radially split BB4 and BB5.
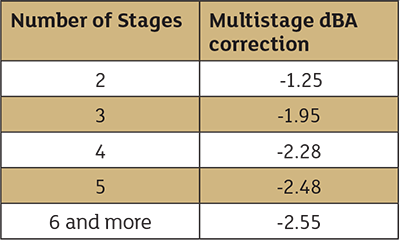
These pumps are typically used in applications for boiler feed, reverse osmosis, and other high pressure and temperature applications. Overhung impeller multistage pumps such as the OH7j, the OH1j and the OH13j are useful in low-flow, high-pressure applications and control hydraulic radial load through the use of diffusers.
For multistage pumps, a low NPSH required (NPSHR) first stage can be added to supply the second stage—especially applicable when the second stage has a higher NPSHR than the first stage.
Vertical and horizontal multistage pumps behave similarly to multiple single-stage pumps operating in series. This should be considered when designing a pumping system that calls for higher head requirements.
Multistage pumps may also be useful for noise reduction. For pumps of the same power, an increase in the number of stages lowers noise levels compared to a single stage. Estimates for sound pressure reductions for increased
stages at the same power level can be referenced in Image 1.
For more information about valves and multistage pumping, refer to ANSI/HI 9.6.6 Rotodynamic Pumps for Pump Piping, ANSI/HI 14.1-14.2 Rotodynamic Pumps for Nomenclature and Definitions and ANSI/HI 14.3 Rotodynamic Pumps for Design & Applications at pumps.org.
Read more HI Pump FAQs by clicking here.