New to working with bearings? Start here.
SKF USA Inc.
02/21/2018
Industrial rotating machinery relies on rolling bearings to reduce friction, power consumption and heat generation, while supporting heavier applied loads at higher speeds with more accuracy. Regardless of application, basics remain constant to achieve optimized performance and service.
Mounting Bearings
When the wrong tools or improper mounting techniques are used, bearings can easily be damaged or installed incorrectly. The environment should be clean and free of any contaminants or corrosive fluids. This includes the working surface, hands/gloves and tools.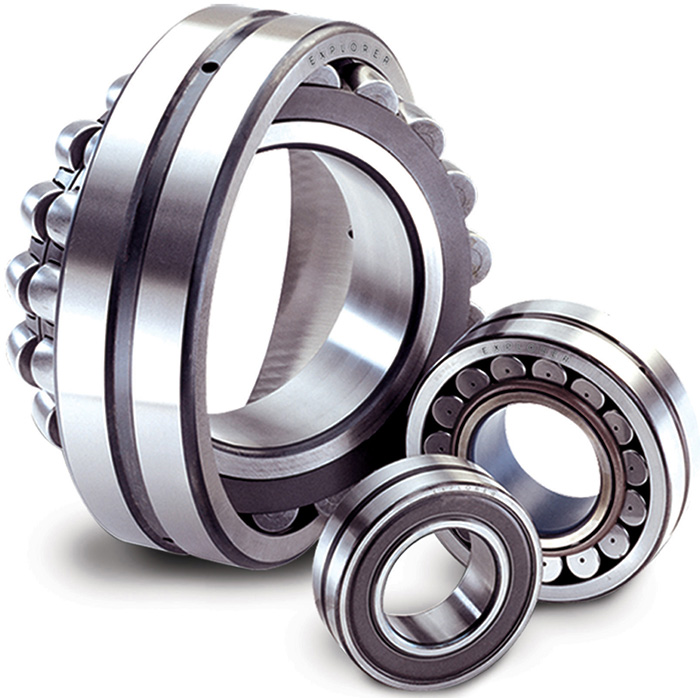