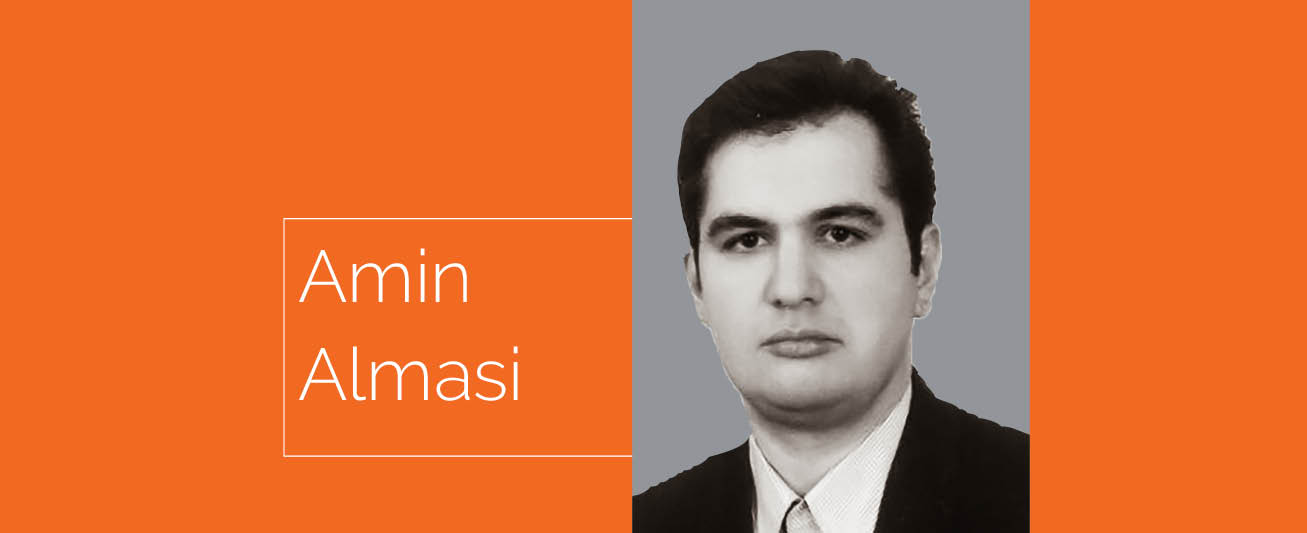
The best efficiency point (BEP) is the point along a pump performance curve where efficiency is the highest. In other words, BEP is the point at which the pump efficiency peaks. In any pumping system, operating at or around BEP of the pump is desired. However, there are many things to consider and issues to avoid in order to achieve this ideal operation.
BEP & Performance Curve
The performance curve shows how deviation from BEP, working to the left side or right side of the BEP, would affect the operation and performance of the pump. The pump characteristic curve is the head (discharge pressure) versus flow rate (capacity) curve. The preferred operating range is typically defined as 70% (or 75%) to 110% (or 115%) of flow at BEP for most centrifugal pumps. However, this is just an indication, and the actual pump curve and its behavior in the system should be carefully considered.
There have been various types of curves for different centrifugal pumps. However, there are typically four different curve profiles:
- So-called normal curves, where the head decreases as the flow rate increases. A typical (normal) performance curve head decreases relatively rapidly as flow rate increases.
- Steep curves, where the head decreases rapidly as flow rate increases.
- Flat curves, where the head decreases slowly as the flow rate increases. These curves are actually relatively flat.
- Drooping curves, similar to the normal profile except at the low flow end, the head rises then drops as it gets to the shut-off head point.
A normal curve has an angle, say 25 or 35 degrees on average; therefore, it is more or less inclined. A steep curve has a steep angle (just as indicated), say above 40 or 50 degrees on average. A relatively steep curve can be desirable from the control point of view for some pump applications since a small reduction in the flow will result in a large pressure rise. Therefore, it can help to recover the lost flow. For example, if there is a flow restriction by partial plugging in the downstream, this large pressure rise can help to overcome the problem (partial plugging in this case) and restore the desired situation. The steepness of the curve depends on many details of the pump, such as the number of vanes and the specific speed. However, a steep curve is not suitable for every application.
A relatively flat curve is sometimes desirable, such as when a change in flow should only result in a small change in head. In some applications, as more liquid consumers are turned on, added or connected in the discharge side, the head will tend to just slightly decrease. In other words, because the pump’s curve is relatively flat, in the event of a larger flow rate than expected, the head will decrease only a small amount, which means that the pressure at the consumers will drop only a small amount. Therefore, for such applications where many different consumers can come on and off, a relatively flat curve works better. A good example of such an application is the fire water pump.
A drooping curve shape should usually be avoided because it is possible for the pump to hunt between two operating points that both satisfy the head requirement of the system. This is known to happen when two pumps are operated in parallel. When the second pump is started, it may fail to get to the operating point or hunt between two points that are at equal head.
Theory vs. Practice
The BEP data and the pump performance curve are usually only theoretical values until the shop or site performance test. The actual BEP data and performance curve are determined by the pump test. They may be slightly different than the theoretical BEP and curve.
There have been many sources for such deviations or differences. For instance, actual dimensions and details of the impeller and casing might be different from theoretical ones, or the simulation of the liquid flow inside the pump was not accurate. The impeller details play a major role in the BEP and curve. Any change or modification of the impeller will change the BEP and curve of the pump. The casing usually has less of an effect.
Trimming of the impeller, or slightly changing the impeller (slight modifications on vanes, etc.), can be used to make some changes on the performance curve and BEP. However, these changes need to be made with great care.
Control Valves in Pumping Systems
The flow rate through a pump is usually determined by the pressure (head) in the downstream (discharge) of the pump. A control valve in the pump discharge piping is most often used to control the flow rate and overall operation. If the system is set up properly, the control valve might help to keep the pump operating near BEP. However, there are some important factors that should be considered. The control valve has a pressure drop across it, which represents a waste of energy. Operational conditions regulated by the control valve may push the pump to operate sometimes far from its BEP if the system is not designed and operated properly. This can directly affect the reliability, performance and efficiency of the pump.
BEP, Vibration, Heat & Noise
Vibration of a centrifugal pump almost always varies with flow and operating point. Usually, the vibration is the minimum in the vicinity of BEP and increasing as flow is increased or decreased. The rise of vibration as the operating point is moved from BEP to another point depends on many factors such as the pump’s energy density, its specific speed (Ns) and its suction specific speed (Nss). Higher energy consumption per unit of capacity is one of the key effects of inefficiently operating far from BEP. The wasted energy shows itself as heat, unwanted vibration, noises,
damaging forces inside the pump and other adverse effects.
Pumps should be selected and operated to work as close to BEP as possible. However, there are many practical considerations and challenges to overcome in order to achieve this goal. When a pump operates at BEP, it is at its most efficient. This means it uses the driver power as efficiently as possible and reduces energy costs, energy waste and potentially damaging effects. When a pump operates at BEP, it usually produces the lowest vibration readings and lowest temperature readings. Therefore, pump reliability/availability is increased and maintenance costs are decreased.