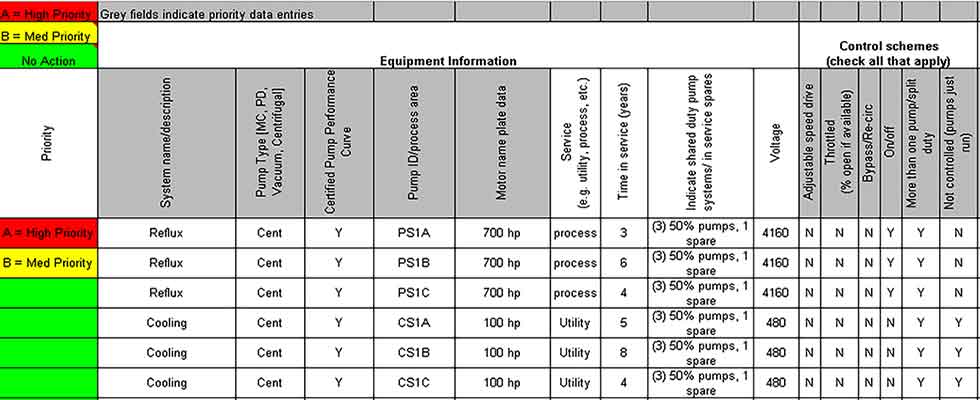
When pump systems are not optimized to their fullest, it impacts a facility’s bottom line with increased maintenance, operation, lost production and higher energy costs. Full system optimization improves reliability and reduces energy consumption while improving the end user’s control to meet the process requirements.
However, it is not always apparent what systems need optimization, and expertise may not be available on staff to make that determination.
To decide if a system can be optimized cost effectively, engage a certified pump system assessment professional (PSAP).
They can evaluate the system to see if it is amenable to a pump system assessment (PSA). The PSAP certification—only a few years old—is a first for the industry. The certification verifies candidates’ education, experience and knowledge to ensure they meet the requirements. PSAPs must meet the requisite education and experience criteria and pass a certification exam covering 34 knowledge areas required to conduct a PSA.
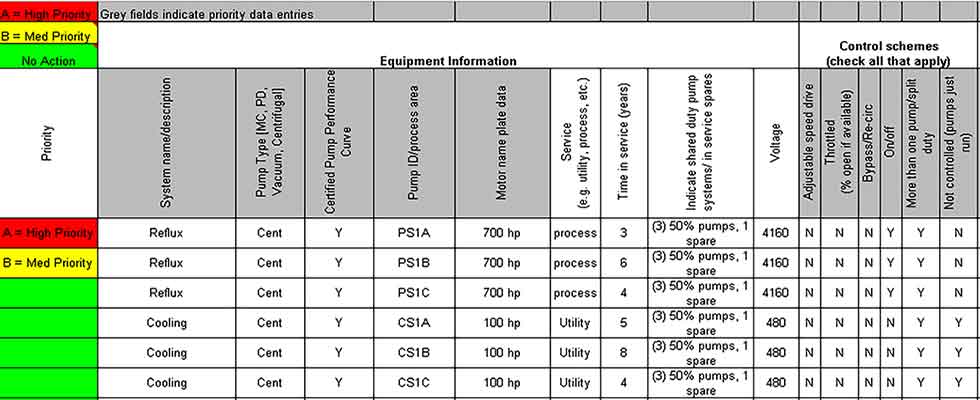
The PSAP follows best practices in PSA by adhering to a 13-step pump system assessment and optimization process (see below).
13-Step Pump System Assessment & Optimization Process
- Determine if the system is amenable to a PSA.
- Obtain and analyze initial information about the pump system (i.e. prescreening).
- Define the PSA team, roles and responsibilities, project scope and boundary conditions.
- Visually assess the pump system, obtain additional information and finalize the project scope.
- Interview stakeholders to provide additional information.
- Obtain real-time pump system operation data.
- Cross-validate the pump system data collected to ensure accuracy.
- Analyze data based on the project scope and boundary conditions.
- Interpret the analysis, establish initial findings and options for optimization.
- Formulate specific recommendations.
- Prepare PSA report with sufficient data and prioritized recommendations about costs and benefits.
- Present the report to stakeholders and assist in the transition from assessment to implementation.
- Perform post-implementation measurement and verification and generate a report.
To implement properly, the system owner should have an advocate who communicates the importance of the assessment and helps coordinate plant resources in support of it. The advocate, along with the PSAP, will communicate with management the opportunities, pull in the right plant personnel, equipment manufacturers, and specialists to ensure the desired outcome is achieved.
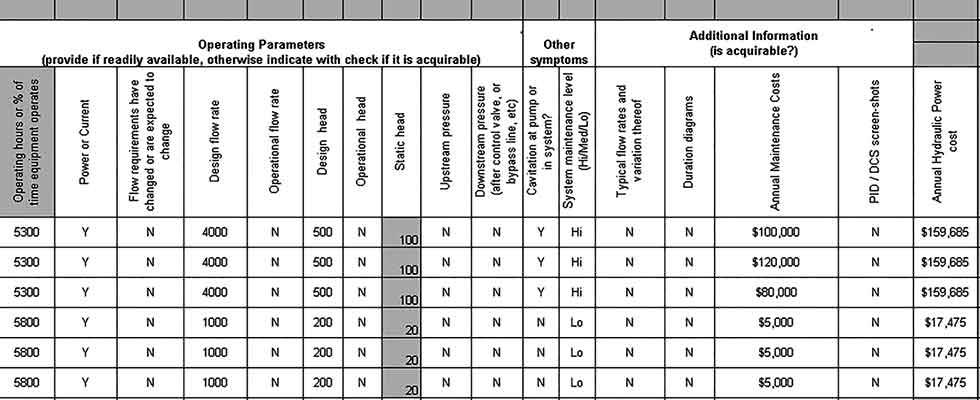
The best practice to determine what systems should be assessed is through prescreening. The team will analyze some easily attainable information about the pumping systems. The prescreening is important because plants can have tens, hundreds or even thousands of pumps, and system assessments require an investment of time and resources. It is not wise or practical to assess all pumping systems or to select some randomly.
The prescreening helps determine what systems are most likely to benefit from and provide a return on investment if an assessment and optimization efforts are made. The prescreening also provides information that helps the PSAP determine the level of assessment required to understand how to properly optimize the systems. A free prescreening tool and other free flow modeling software tools can be downloaded from the Hydraulic Institute at pumps.org/training.
Typical prescreening data that will help prioritize opportunities are:
- pump system description
- system history (unplanned failures, lost production, process changes, etc.)
- observed system conditions, such as noise, cracked foundation, etc.
- design conditions and operating condition (if known)
- installed motor horsepower
- yearly operational hours
- control method(s)
- available instrumentation
- maintenance records and costs
Other information may be important and easy to gather during the screening process, such as downtime and lost production, safety related incidents or near misses of failure. The prescreening data helps the PSAP prioritize which systems have the highest operating and maintenance costs, followed by systems with known red flags such as cavitation, change in duty without modification, throttle control and frequent cycling.
The PSAP should:
- make a qualitative ranking of pumping systems with the largest savings potential
- list the pump systems and solutions that can be implemented without detailed field analysis
- list pump systems that need additional field analysis and determine the level of assessment required
Images 1a and 1b show an example prescreening for some sample pumps. Note that in part two of the prescreening form there is an annual maintenance cost and annual cost of hydraulic power. Both provide an indication of the opportunity for savings. These numbers along with other system red flags prioritize the systems for assessment and optimization.
It is sometimes hard to justify assessments and optimization based on energy cost savings alone.
Assessments are typically easier to justify by examining a combination of factors gathered during the prescreening, with unplanned failures resulting in system downtime, lost production, safety or environmental incident, or high maintenance costs topping the list.
After rationalizing what systems should be assessed in greater detail, the PSA team and assessment plan can be developed. It is important that the team have people in defined roles to provide leadership, and with authority, to allocate resources and coordinate logistics. Moreover, qualified assessment engineer(s) are needed with an understanding of the system processes and functions, maintenance practice and history, and cost data.
The assessment team will need to review the available information and determine or confirm the assessment scope, boundary and level of assessment required. Three levels of assessment may be appropriate. A Level 1 assessment is a qualitative review or paper audit. Level 2 is a quantitative review based on steady-state operating conditions requiring limited infield measurements. Level 3 is a quantitative review of a variable system that requires measuring data over time and long enough to characterize the various operating conditions.
In systems with little or no variability, a Level 2 assessment may be used to determine savings potential and optimization recommendations. In this level of assessment, the team gathers the appropriate data taken from plant information systems or by using portable measuring devices, giving a snapshot of conditions at the time of measurement.
In systems with variability and with high potential savings, a Level 3 assessment may be implemented. In this level, a more complex investigation is conducted over an extended period of time to develop a system load profile. More extensive use of monitoring and a more complex data analysis is associated with this level. Detailed component failure analysis and/or hydraulic system modeling may also be included. For example, if unexpected bearing failures are an issue, a detailed analysis of bearing temperature(s) along with system operating conditions and an inspection of the failed bearings may be required.
Once an assessment is completed, the results should be documented and reported to the management team. The final assessment report should include the following sections:
- Executive summary
- Introduction including facility information
- Assessment objectives and scope
- Description of systems studied and their deficiencies
- Assessment data collected
- Data analysis
- Annual baseline costs of operation, maintenance, downtime and production loss
- Prioritized performance improvement opportunities
- Implementation steps
- Data appendices
The report and other documentation should include sufficient raw data from the assessment so the analyses can be confirmed by a third party. This format provides an effective summary in the beginning for management, and the background and detailed analysis required to justify the recommendations.
It is important to economically validate the optimization opportunities and effectively report the assessment results.
The presentation of the report should be tailored to the purpose of the assessment, which may take different forms depending on the reason for the assessment and the personnel it is presented to. Lastly, follow through on the recommendation and perform after measurements to verify the improved operation, which will provide confidence in repeating the process on other pump systems.