Inspections can identify undetected issues to prevent sanitary sewer overflows and the fines that can accompany them.
03/11/2014
Wastewater utility organizations have been caught in the same budget constraints as most other public services during what some refer to as “The Great Recession.” After years of coping with staff reductions, a limited budget for outsource services and deferred maintenance, the use of the run-to-fail strategy by some sanitary districts increased for assets such as lift station pumps. Of course, there are exceptions among wastewater utility managers who follow preventive maintenance practices. The reasoning is simple. Pump station failures usually translate into contingent federal and state environmental violations and penalties in the wake of sanitary sewer overflows (SSOs).
A Proactive Maintenance Case Study
Although the Costa Mesa Sanitary District continues to stretch its operating budget, it has not compromised the California utility’s proactive—rather than reactive—maintenance strategy. The utility strives for reliability from the duplex pump stations along the 224-mile long collection system that cross-stitches the 16-square-mile service area. General Manager Scott Carroll has practiced annual preventive maintenance (PM) inspections since joining the district four years ago. The district then outsources repairs on an incremental basis as they emerge throughout the following year to the contractor awarded the initial inspection work.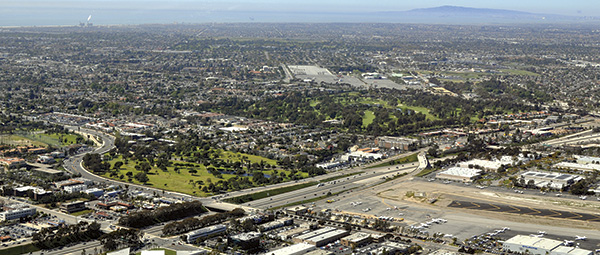
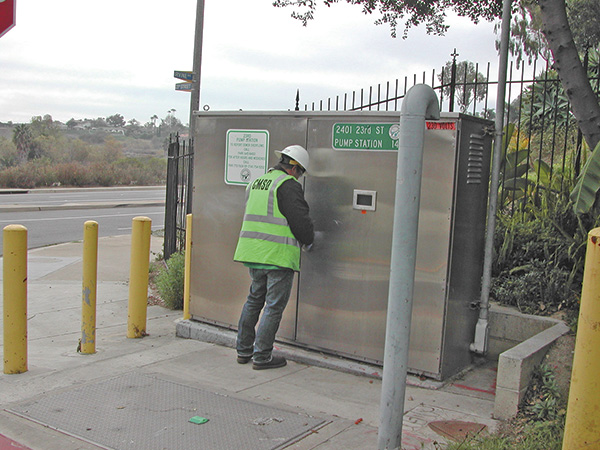
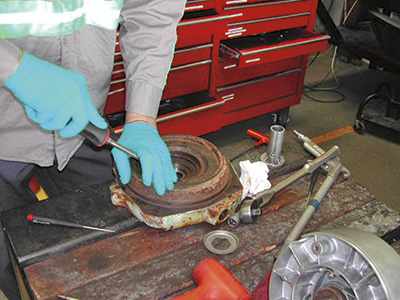
The 20-point Checklist Applied at Costa Mesa Sanitary District
- Check electrical condition of insulation on power cables and all phases of the motor
- Identify any loose or faulty connections with the pump control panels
- Examine voltage between phases on the load side of activated pump control panel
- Check amperage draw on the pump motor
- Inspect condition and operation of any motor thermal protection control system
- Remove and physically inspect the pump from the lift station
- Check upper shaft seals and condition of motor/stator housing
- Identify the condition and operation of any motor/stator leak detectors
- Check lower shaft seals and condition of the lubricant oil
- Change oil annually
- Inspect for worn or loose impellers
- Check impeller wear ring, both rotating and stationary
- Listen for any bearing noise indicating damage or wear
- Inspect pump power and control cables for possible damage
- Clean, reset and test operation of any level control system
- Inspect for correct shaft rotation
- Reinstall and check operation of the pump
- Test pump cycle under submerged load
- Check valve operation and any associated equipment