HI Pump FAQs
Hydraulic Institute
10/26/2016
Q. What primary and secondary containment considerations are recommended for canned motor pumps? A. A canned motor pump (CMP) is a type of sealless pump that has a common shaft to link the pump and motor in a single sealed unit (see Figure 1). The pumped liquid is circulated through the motor, but it is isolated from the stator by a corrosion-resistant stator liner. The motor rotor is protected by a corrosion-resistant rotor liner.
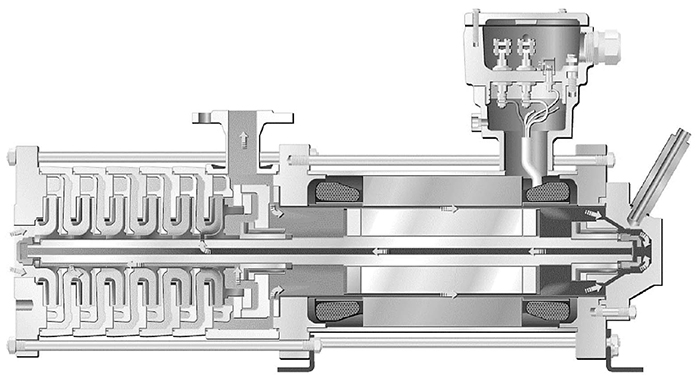
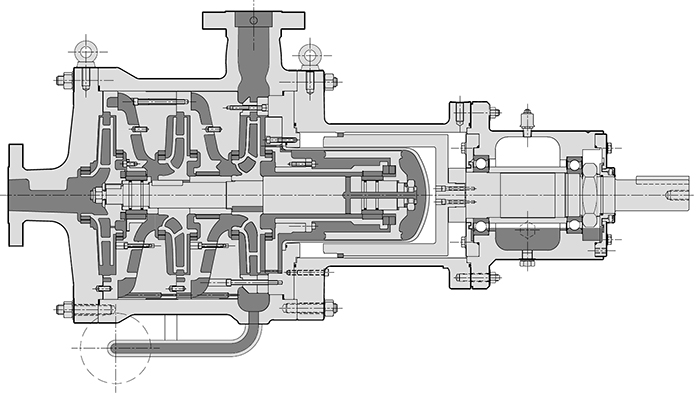
See other HI Pump FAQs articles here.