Achieve savings with pump efficiency testing.
Hazen and Sawyer
11/27/2018
The following case studies, performed by the author, paint a picture of the savings that can be achieved with properly executed pump field testing.
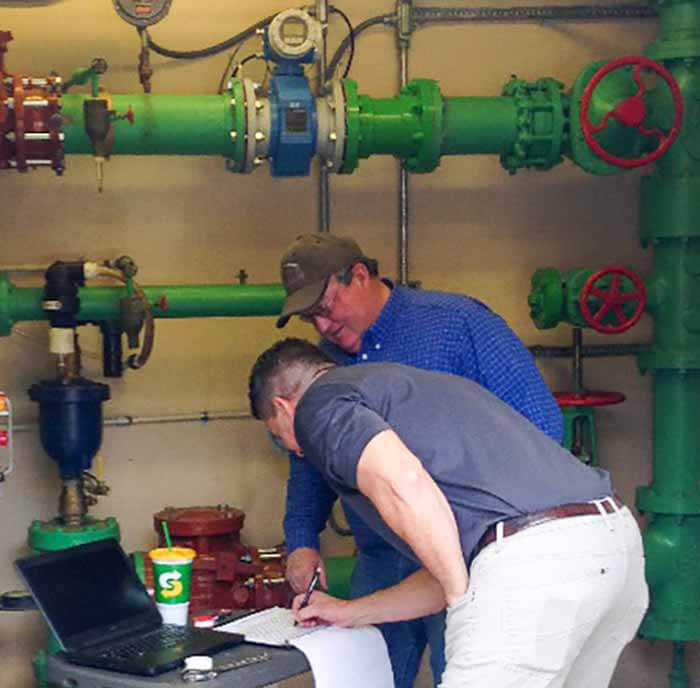
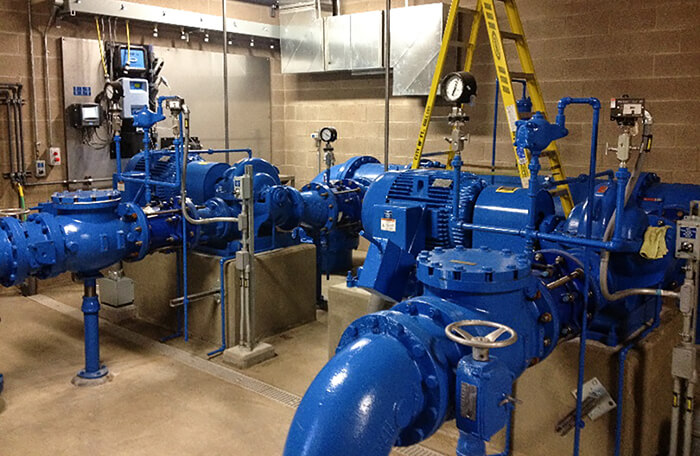
- replacing a pump’s isolation butterfly valve, which was protruding into the cavity of the swing check valve immediately downstream, with a gate valve to allow the swing check to fully open
- installing a combination air valve on an air-locked pump discharge on end suction centrifugal pumps
- increasing the speed of the VFDs to a frequency that allows the pump system to overcome the backpressure of the system curve and provide flow at a substantially greater efficiency
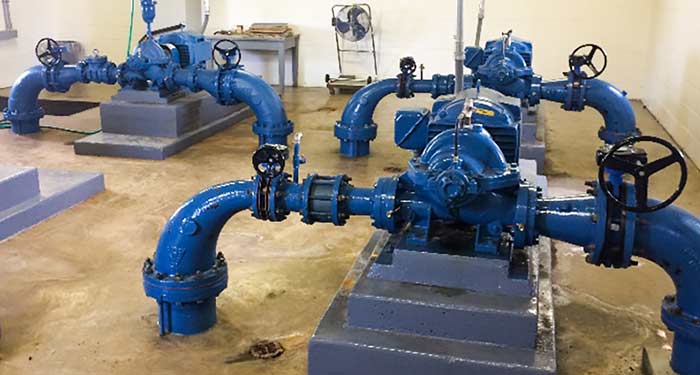
- Increase the speed of a VFD so it pumps water and does not just spin in the casing.
- Increase pumping level in the clear well to reduce the kilowatts per millions of gallons per day (kW/mgd) by 15 percent.
- Add air release valves at top of split case pump casing and at several intermediate pipeline highpoints.
- Replace leaking check valve allowing 60 to 80 gpm to flow backwards through the pump.
- Install straightening vanes on split case pump suction to improve suction straight pipe lengths and balance impeller force load distribution.
- Lock out maximum hertz for certain pumps that cavitated at high speed.
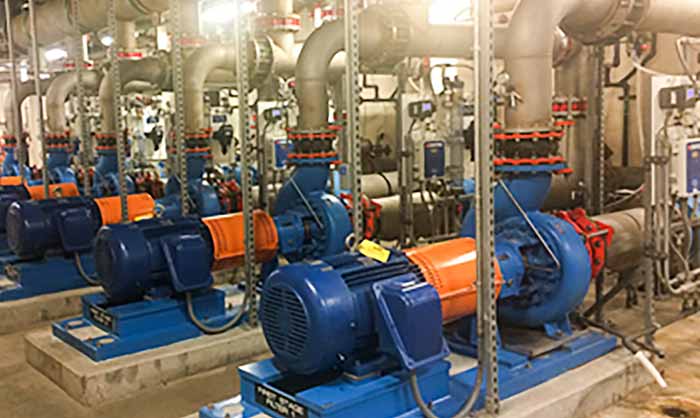