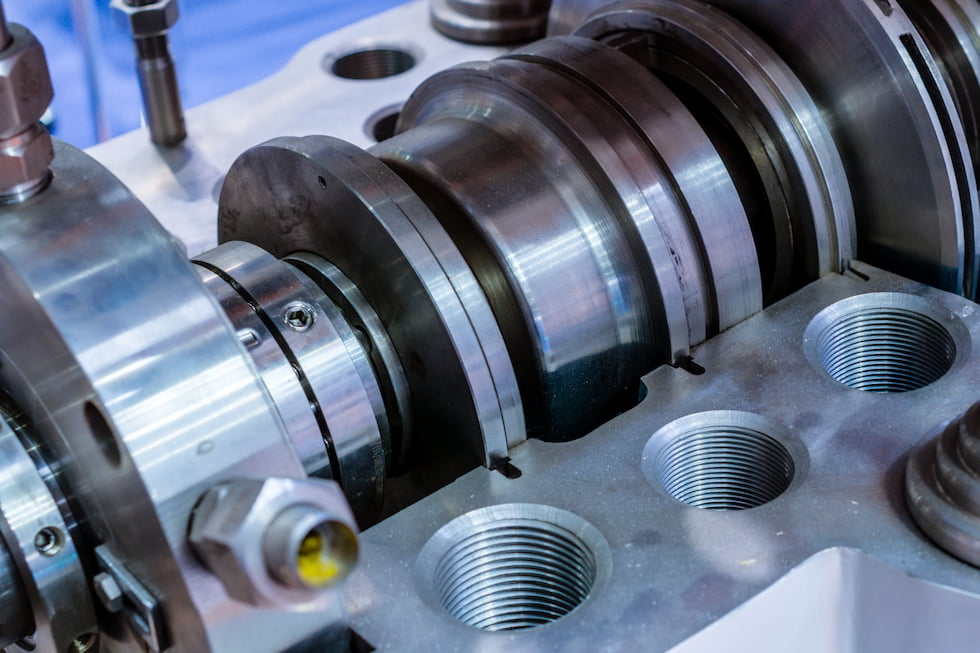
In the beginning, water ran freely over the Earth. Then, man made pumps to make water run where he wanted it. Then came leaks. Then, man made pump seals. And as time went on, man still continued to struggle with leaking pump seals.
For those who are new to pump maintenance and repair, mechanical seals can be intimidating—given their reputation as temperamental devices that fail frequently. In fact, they are simple devices that are often misapplied and sometimes poorly installed or used on pumps that are ill-suited for the application. For many applications, mechanical seals are robust enough to tolerate less-than-optimal handling and operating conditions. For more demanding applications, though, everything must be right.
How a Mechanical Seal Works
It is important to review how a pump mechanical seal works. First, its main components are the rotating and stationary face rings that form the primary seal (Image 1). The face rings have flat, precision-smooth contact surfaces that are held in tension against each other by mechanical springs.
The rotating face ring and its assembly have to be sealed to the shaft. The stationary face ring has to be sealed to the housing. These two sealing points are called secondary seals and typically use elastomer O-rings or boots (Image 2).
Pump Seal Materials
Selecting the proper materials for the primary and secondary seal components is important. For common water pumping applications, carbon-ceramic face material and Buna-N secondary seals are standard and work well. Alternate materials work better for pumping sewage or strong chemicals, so many technicians seek outside help on these applications.
Precautions Ensure Success
By following a few precautions, it is not difficult to install pump mechanical seals during the repair process. For example, to ensure the elastomer secondary seals will slide into place undamaged, always use the proper lubricant. Some seal providers offer water-soluble lubricants designed for this purpose. Make sure the lubricant is water-soluble (except with oil-filled seal chambers), so that it will be washed away by pump operation.
In all cases, avoid damaging the elastomer secondary seals on the edges of shaft shoulders, keys or housings. A good way to accomplish this is to wrap a sheet of mylar paper around the shaft to protect the seal as it is slid into place.
While the amount of tension the seal spring assembly applies can be a concern on some special applications, the tension adjustment on common utility pumps is preset by the pump and seal design. Just observe during disassembly if there are any tensioning provisions and, if so, document the measurements.
When a seal leakage problem occurs, carefully inspect the seal to determine the cause. Is it leaking at the primary seal or at one of the secondary seals? The wear pattern of primary seal faces should be smooth and slightly shiny, and the elastomer secondary seals should be pliable but not soft. The shaft and housing contact surfaces should be corrosion free; corrosion at those contact points would indicate a leak.
Seal Providers
If the cause of a problem is difficult to determine, many value-added seal providers can analyze seal failures, ask critical questions about the application and recommend products that will perform best. Their prices may be more than some alternatives, but their value added is the knowledge to spec the right product.
If unsure about how to find a good, value-added seal provider, do an internet search for “industrial pump seals” in the required zip code. In major metropolitan areas, there are probably three or four likely prospects. Ask each of them for a seal for a boiler feedwater pump (or other tough application). If they only ask for the pump ID or the dimensions but not the temperature, pressure or other application parameters, they probably will not be much help. Users may get a great price, but on the wrong product.