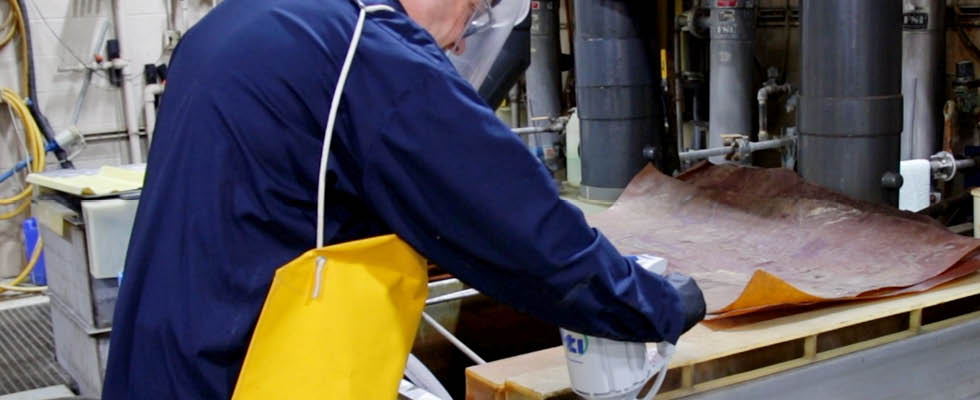
Power generation is a complex, demanding business that requires high levels of reliability to keep the electricity flowing and the lights on.
The vast majority of the world’s electricity is produced by steam turbine plants. Thermal power plants such as coal, natural gas, nuclear and geothermal rely on heat to turn water into high pressure steam, which is used to spin the turbine and create electricity. The steam is then cooled, condensed back into water and returned to the boiler to start the process over.
In a power plant, the primary functionof the boiler is to transfer massive amounts of heat from the source of combustion into steam to drive turbines. Once the water evaporates inside the boiler, dissolved salt leaves scale deposits on the heat transfer surfaces. Scale has much lower heat transfer capacity than a steel boiler. In the best case scenario, the scale buildup causes inefficiencies from reduced flow, but at worst, the scale can cause overheating and potential failure of the boiler tubes.
The cooling towers used to remove the heat absorbed in the circulating water system can develop organic growth. Cooling towers contain large amounts of water and are potential breeding grounds for Legionella bacteria if they are not properly disinfected and maintained. Water within cooling towers is an ideal environment for these heat-loving bacteria to grow.
Over time, if left untreated, organic growth, fouling, scaling and corrosion can reduce plant productivity, cause plant downtime and require costly equipment repairs and replacements. Plant operators must control these scale deposits as well as provide corrosion control in the boilers, condensers and heat exchangers. This requires the use of harsh chemicals.
Common Treatment Methods
Common treatment methods combine coagulation, flocculation and ion exchange resin to create high-purity water to be converted to steam. Cooling systems also require neutralization and descaling chemicals. These processes require reliable pumps to handle the harsh chemicals involved, which is where chemical pumps come in.
Some of the processes involved include:
- Neutralization – During this process, sulfuric acid, hydrochloric acid or a basic chemical like sodium hydroxide may be added to the water to achieve pH balance.
- Removing free solids – To help remove solid particles through a process of coagulation and flocculation, chemicals like polyaluminum chloride (PAC) and ferric chloride are used. Coagulation is the coming together or clumping of particles, and flocculation is the settling of coagulated particles.
- Disinfection – Sodium hypochlorite (bleach) is frequently used to disinfect the water.
- Descaling – As deposits build up in power plant equipment, corrosive chemicals like acids and bases are often used to break down and remove scale from boilers.
- Ion-exchange – Hydrochloric acid and sodium hydroxide are used to regenerate the resin beds.

Common Types of Chemical Pumps
There are a number of chemical pumps that can be used to handle the harsh chemicals used in power treatment plants.
Drum/tote/intermediate bulk container (IBC) pumps
These pumps can be hand powered, alternating current (AC) powered and use lithium-ion batteries or be pneumatically driven. The pumps are portable, easy to handle and ideal for transferring smaller quantities from 55-gallon drums or larger tote/IBCs that are capable of storing five or six drums’ worth of chemicals.
Centrifugal pumps
Using rotational energy supplied by an impeller, these pumps provide a smooth flow and are available in a wide range of sizes. They are ideal for efficiently transferring chemicals from bulk storage to smaller day/feed tanks.
They are available in a wide range of materials of construction to safely transfer even the most corrosive fluids. They are available in mechanically sealed or sealless magnetic drive. Sealless magnetic drive pumps offer increased reliability and safety.
Air-operated double-diaphragm (AODD)
An AODD pump is an air-driven, positive displacement pump. It displaces fluid at one end while suction occurs at the opposite end. These versatile pumps are self-priming, can be run dry and handle solids and abrasives.
Metering pumps
These pumps precisely transfer small volumes of chemicals into the process. They are frequently attached to day tanks that have been filled with the chemical being pumped from larger bulk tanks by one of the other pump types mentioned above.
Choosing the right pump
Once the type of pump or pumps needed for chemicals being used is identified, users must determine the specific pump to use. To determine this, there are several questions that need to be answered.
What type of container is available?
Is the chemical in a pail, a 55-gallon drum, a tote/IBC or a larger bulk storage tank? This helps to eliminate some pump types. For example, a drum pump is typically not the correct choice for a large bulk storage tank.
Is it a permanent or portable installation?
For example, will the pump be in a fixed installation or will it be moved from location to location? Drum pumps are easy to move from location to location. For permanent installations, a good choice is a chemical centrifugal pump.
What types of utilities are available?
Is there electric available? If yes, does it offer the correct voltage, phase and sufficient ampacity? Or, if an air drive pump is preferred, is there air in the area at the correct pressure that has sufficient standard cubic feet per minute (SCFM)? If there is no electricity but air is available, an AODD pump may be the best option.
What is the application information?
Create a detailed description of how the pump will be used, including the total head, the required flow rate, net positive suction head available (NPSHa), altitude and ambient temperature range (an important consideration in power plant applications). This information helps pump manufacturers, distributors or consulting engineers to spec the correct pump for the application.
What materials of construction are needed?
For each chemical being pumped, review the safety data sheet (SDS) to determine the chemical name, concentration, specific gravity, temperature the fluid will be pumped at and if the fluid is a flammable or combustible. Talk to the chemical manufacturer or distributor for specific recommendations about which materials are suitable. Another good source is the chemical pump manufacturer or distributor. Many chemical pump manufacturers have comprehensive chemical resistance guides to identify the best materials to use.
Installation and maintenance
The installation and maintenance requirements of chemical pumps vary by the type and manufacturer. Always refer to and follow the instructions for the installation, operation and maintenance of the pump found in the manual (IOM) that is supplied with the product.
Safe handling of corrosive liquids
It is critical that personnel working with corrosive liquids are properly trained in the specific hazards associated with the storage and handling of the chemical, conditions to avoid and proper personal protective equipment (PPE) to wear.
There are three ways to learn more about the specific hazards associated with corrosive chemicals.
1. Safety Data Sheets
Formerly called material safety data sheets (MSDS), the information in an SDS is largely the same as the MSDS, except they are presented in a user-friendly, 16-section format.
The Hazard Communication Standard (HCS) [29 CFR 1910.1200(g)] requires the chemical manufacturer or distributor to provide SDSs for each hazardous chemical to users to communicate information on hazards.
Sections one through eight of the SDS contain general information about the chemical, identification, hazards, composition, safe handling practices and emergency control measures.
Sections nine through 11 and 16 contain other technical and scientific information, such as physical and chemical properties, stability and reactivity information, toxicological information, exposure control information and other information.
Sections 12 through 15 (Ecological Information, Disposal Considerations, Transportation Information and Regulatory Information) are required to be consistent with the United Nations (UN) Globally Harmonized System of Classification and Labeling of Chemicals (GHS), but Occupational Safety and Health Administration (OSHA) will not enforce the content of those sections because they concern matters handled by other agencies.
2. Chemical Manufacturer Resources
It is always a good idea to speak to the company’s support staff or technical sales person. Users can also ask if they provide a guidebook.
Guidebooks provide additional technical information on the material. This can include more extensive details on the chemistry and properties, safe handling and storage information, system design and installation information and materials that are compatible with the chemical.
3. Pump Manufacturer Technical Staff
The pump manufacturer may have recommendations that take into account the material being transferred as well as the application/performance requirements. Users must make sure they deal with a reputable company that has years of experience in the application of the pumps for use with the chemicals being pumped.
There are multiple options when it comes to power generation, be it coal, nuclear, geothermal or natural gas. Similarly, there are multiple options when it comes to choosing the right pump system to support each of these. Selecting the right pump type, size and materials of construction is critical to having a safe and reliable solution for electricity production.