Many chemical companies have aging assets. With this comes the risk of equipment failure and unscheduled stoppage. Take a look at the root causes of that downtime and there is a high chance that vibration fatigue, bearing failure or inadequate lubrication will feature prominently. The effective maintenance of assets plays a crucial role in meeting the universal challenge of maximizing the reliability and efficiency of assets to optimize profit margins, while ensuring the safety of end users who work in potentially hazardous industrial environments. It is fair to say that the companies negotiating these operational demands most successfully are those that have recognized that a “fix it when it breaks” reactive maintenance approach is no longer a viable option. They have embraced technology as a key driver for embedding proactive condition based maintenance (CBM) into their maintenance plans. Operational technology has advanced at a rapid pace in recent years, bringing with it advanced CBM methods.
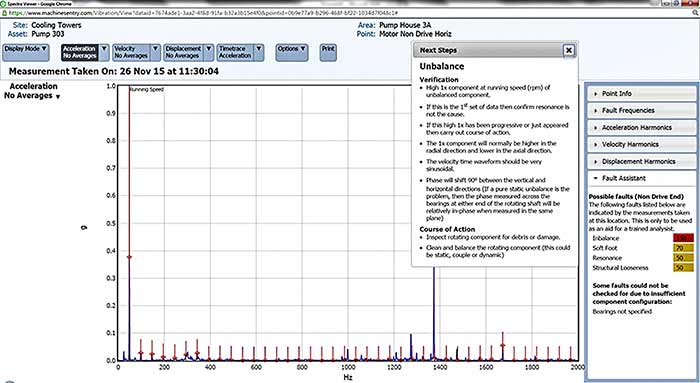
Taking Maintenance Online
Whether a multinational or a smaller-scale independent chemical company, the efficient management of business and safety of critical assets is a key priority. Advanced cloud-based technology allows those assets to be managed online, employing high-speed wireless connections to provide continuous real-time monitoring. Multiple web connections means that diverse data—in vibration and oil analysis for example—can be collected and consolidated on one platform, where it can be securely accessed from anywhere via a standard web browser.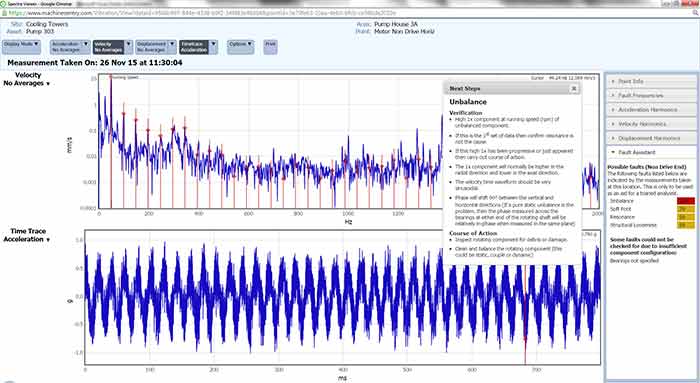
Preempting Causes of Downtime
The chemical industry can be applauded for its efforts to combat unscheduled stoppages by adopting a more predictive approach to asset management in recent years. What advanced technology offers is the ability to take this a step further and create a culture of truly proactive, operator-driven reliability. Many solutions are now on the market that can identify the subtle changes which might indicate a potentially production-halting problem is on the horizon, and offer data-driven insight to inform decisions on how to avert it. The continuous availability of data also provides a bedrock of in-depth knowledge on which to base an ongoing maintenance plan.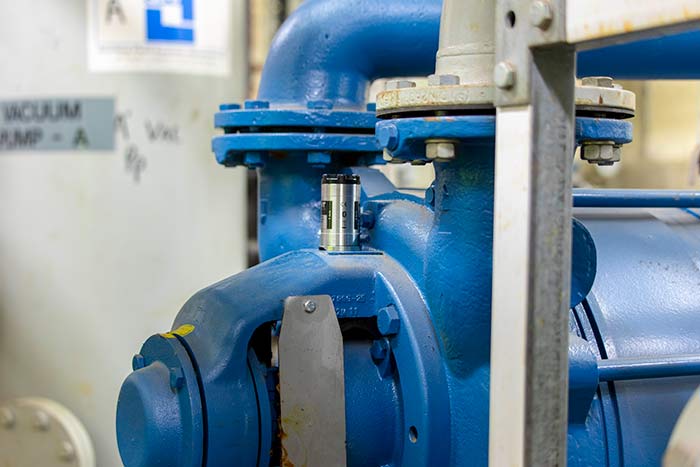
Automated Fault Diagnosis
Excessive vibration is a key indicator of a developing fault in rotating machinery. Although it should be a central pillar of any reliability program, vibration analysis is one of the least understood elements of CBM practices. This is largely due to the variety of potential faults that can indicate excess vibration. At the simple end of the scale, it could be a result of misalignment or the need to replace rolling element bearings—both easily remedied. At the other end, it could forewarn of a complex issue such as poor rotor bar conditions or soft foot. Certified vibration analysis can be costly and time-consuming. A web-hosted, algorithm-based condition monitoring system could provide the answer when cost or recruitment challenges are proving prohibitive to effective vibration analysis. Powered by thousands of hours of vibration data and years of extensive in-the-field expertise of vibration analysts, an automatic diagnostic assistant can automatically detect and report on more than 20 conditions commonly known to reduce equipment reliability or, at worst, halt production. A tri-axial sensor attached to rotating machinery provides periodic monitoring, and the visibility across three axes means it is unlikely for risks to go undetected. Standard wireless technology connects it to the software via phone or tablet, meaning a maintenance engineer can collect data easily, even from large, infrequently running or hard-to-access assets, and from a safe distance of up to 50 meters—a crucial consideration in hazardous environments. This automated diagnostic assistant can offer real-time analysis 24/7. It will either pinpoint the single most likely problem, or present up to four potential points of failure, ranked in order of greatest likelihood, and outline the next steps to take. This could be anything from cleaning and rebalancing a rotating component, to dealing with structural looseness. The responsibility for complex data analysis is removed—the automated diagnostic assistant employs a traffic light system, where green means no issue is detected, rising to amber and red where problems are identified—so any maintenance engineer can use it.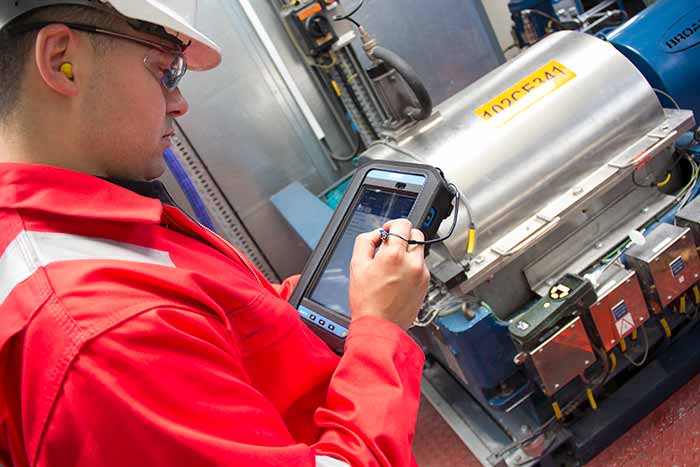