Consider reuse and power consumption when assessing centrifugal and positive displacement pumps.
Verder Inc.
09/20/2018
A slurry pump typically refers to a rubber-lined centrifugal pump. Generations of use in mining slurry pumping has earned the rubber-lined centrifugal pump the reputation as the first choice for this application. But recently, emerging technology and increased awareness of positive displacement (PD) slurry pumps have broadened the landscape of pumping options for slurry applications. The traditional centrifugal slurry pump consists of a pumphead or volute, usually split vertically. Within the pumphead are two rubber liners that mate together once the volute is assembled.
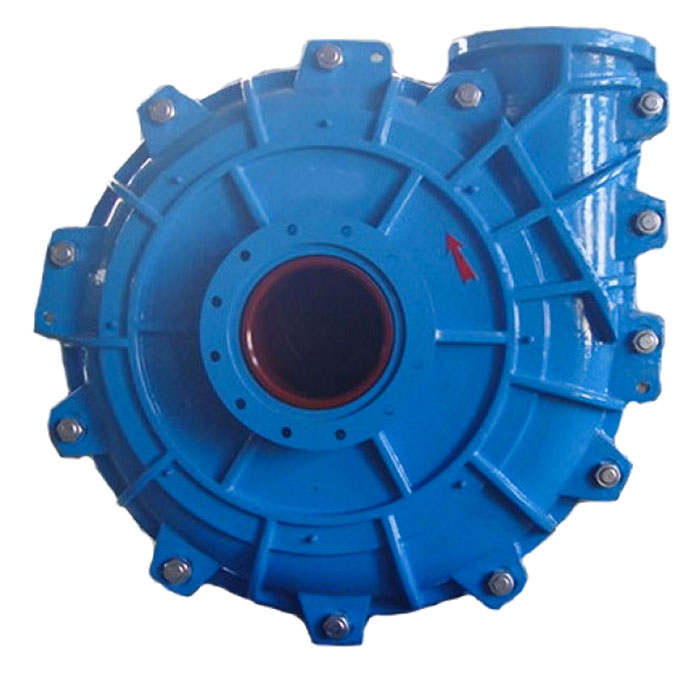
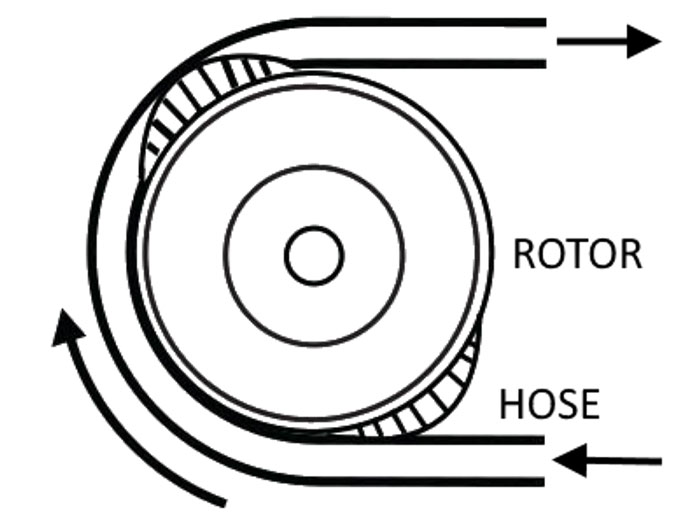
Water Use
Peristaltic hose pumps can circulate slurry with up to 80 percent solid content, with specific gravity of 1.6 to 1.8. Traditional centrifugal slurry pumps typically operate around 1.3 specific gravity, but can pump 50 percent solids in some services before suffering wear or hydraulic issues. Given a 75 tons per hour (TPH) ore processing rate, using the above slurry concentrations, a peristaltic hose pump will need to pump 210 gallons per minute (gpm), while the centrifugal pump moves 457 gpm—a difference of 247 gpm. This calculation shows that to process 75 TPH of ore, a centrifugal pump will require 130 million additional gallons of water over the course of a year. Depending on the mine location, the cost of industrial water can range from 0.4 cents per gallon in the U.S. to 1.6 cents per gallon in Australia, and several times more in arid, remote locations. Consider water reuse in this analysis. Reclaiming used water carries inherent cost in electricity, equipment, maintenance, etc. However the cost is much lower than purchasing new water. Most U.S. mines are at about 90 percent reuse, with some mines approaching 100 percent reuse. This means (not accounting for the cost to clean used water) that a mine with 98 percent reuse paying $0.04 per gallon for new water would save about $104,000 per year in water usage by operating a peristaltic hose pump.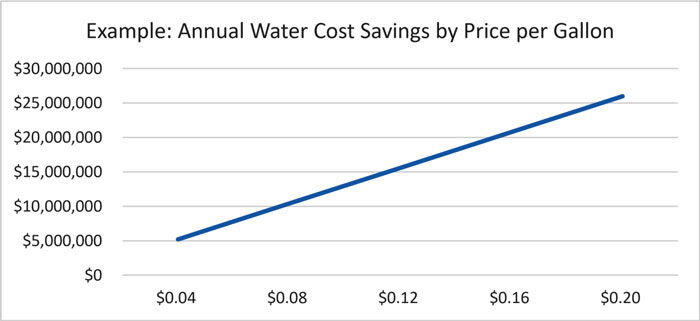
Power Consumption
On the same 75 TPH process operating at 90 pounds per square inch (psi) system pressure, a properly sized peristaltic hose pump requires 28.5 brake horsepower (bhp) for operation. By comparison, a centrifugal slurry pump requires 39.8 bhp (assuming 60 percent hydraulic efficiency). Power consumption varies between the two technologies with the centrifugal pump requiring up to 30 percent more power to operate. Electricity rates vary. Power in the U.S. costs around $0.10 per kilowatt hour (kWh). Images 3 and 4 are based on assumptions that a peristaltic hose pump (or other PD pump) can operate at 80 percent solids concentration and that the centrifugal slurry pump operates at 50 percent.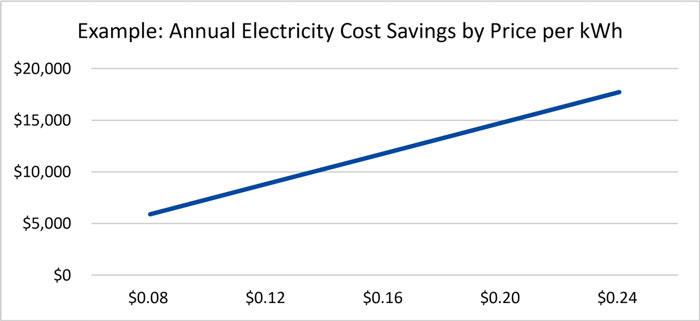