Sealing Sense
Fluid Sealing Association, W.L. Gore & Associates
08/31/2017
Editor’s Note: This article contains Information from ESA Members Stefan Schulz and Oliver Zach.
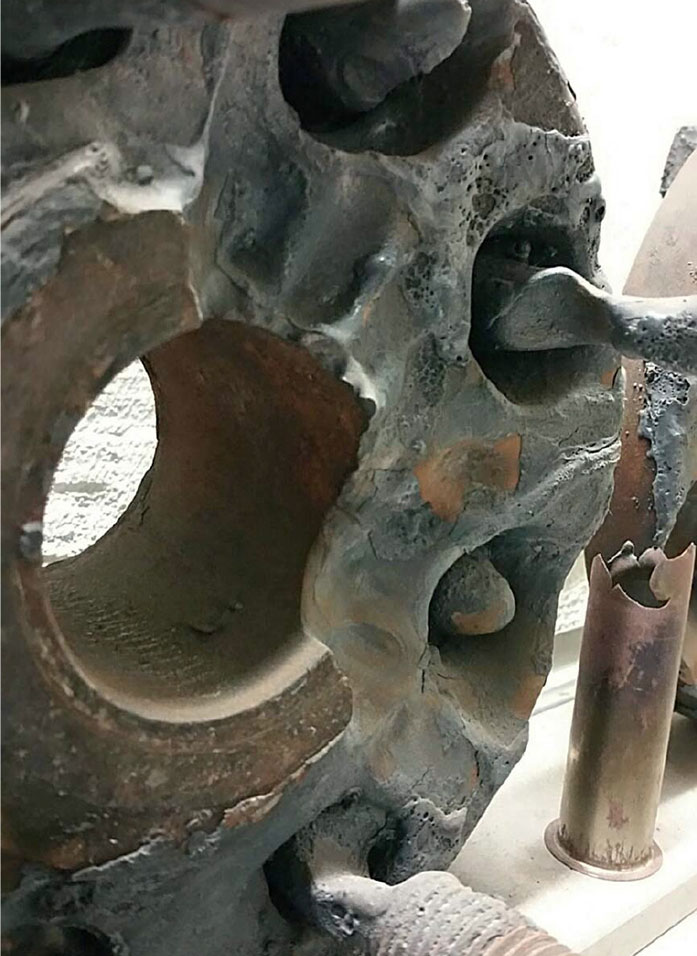
Material Selection
In the industrial market, it is important for safety that the proper construction materials, both metallic and non-metallic, are used for equipment. Contaminants such as oils, fats or organic particles can create unsafe conditions in operation and must be avoided (see Image 2). Additionally, stable processes are needed to avoid pressure surges or very high flow velocities.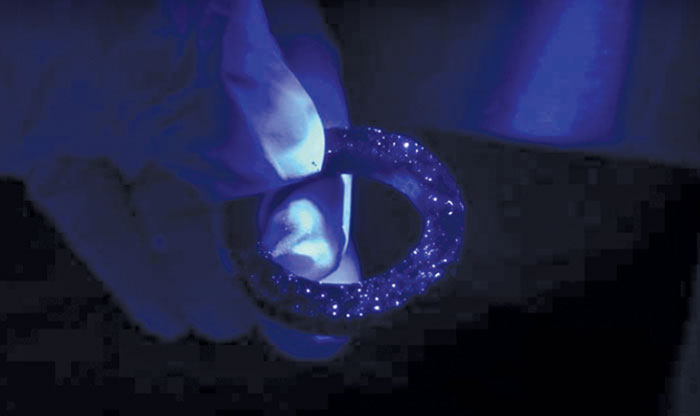
Information Is Key
End users must ensure that the gasket manufacturers and packing braiders are explicitly informed about the intended oxygen application during the order process and that the gland packings and gaskets are handled as carefully as possible in the production process of the manufacturers. It is also their responsibility to check whether the safety assessment meets the requirements of the end user or operator. Usually gland packings and gaskets for oxygen use are separately manufactured (free from oil, grease and other sources of contamination), checked and individually packaged following special precautions. This information must be indicated on the packaging as an imprint, or on the label. In order to ensure the safety and availability of oxygen service valves and components, a continuous chain must be created. Starting from the production of the materials through their further processing into components and safety assessments, the chain ends with usage in the plant. The production processes and test procedures currently differ significantly from manufacturer to manufacturer, as does the handling of these issues by the end users. In fact, there are no standards or rules that regulate this process except for the national and international standards specifying the test procedures for the safety assessment of the materials, valves and components. To address this less-than-desirable lack of regulations, working groups with participants from packing and gasket manufacturers have already been formed and include end-user participants. In the field of safety and environmental protection a significantly increased awareness needs to be created of the danger of industrial oxygen applications. This includes careful selection of gland packings and gaskets to ensure the implementation of the best available techniques. Next Month: Formulating materials for dynamic sealing over a wide range of operating conditions We invite your suggestions for article topics as well as questions on sealing issues so we can better respond to the needs of the industry. Please direct your suggestions and questions to sealingsensequestions@fluidsealing.com.
See other Sealing Sense articles here.