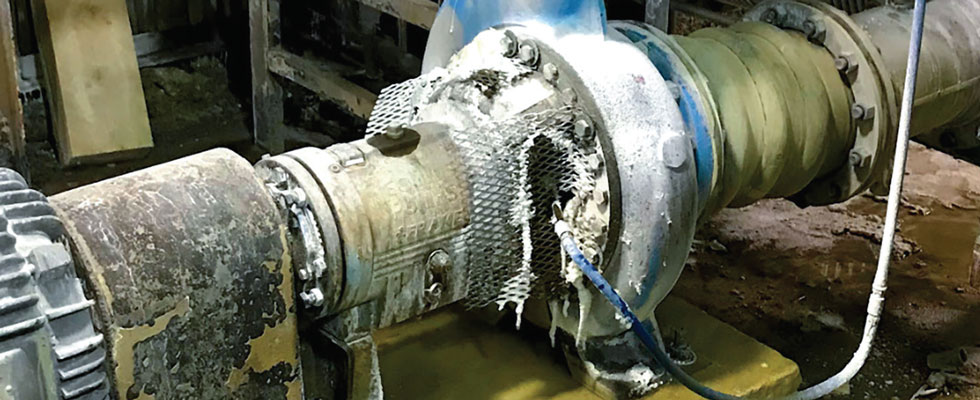
In the world of safety, many accidents occur because people assume they fully understand how to respond or use equipment during an emergency. After reviewing some high-profile incidents, it becomes clear that their assumptions are often incorrect.
In reality, training and understanding was insufficient, resulting in damage. A term called “the illusion of explanatory depth” (IOED) is being used in many circles to show how this assumption of knowing has caused harm. It affects all industries, so it is important to recognize. In the world of packed pumps, IOED is seen many times because people believe packing is basic, and make wrong assumptions because of its supposed simplicity.
Recently, an end user reached out to the Fluid Sealing Association (FSA) regarding the calculation of flush pressure for a slurry pump. The pump manufacturer directed the engineer to set flush pressure 1 bar—14 pounds per square inch (psi)—above the discharge pressure on the pump. This kind of directive is often due to limited knowledge of the system. While it may seem like a safe assumption for a broad set of applications, this actually can lead to shorter packing life and more downtime for the plant. For this particular end user, there was the added issue of obtaining the required pressure in the plant.
This may cause headache and despair for some, but to others it can be an exciting challenge. By diving into a system and understanding the data behind a process, accurate flush pressures can be determined to optimize packing life and performance.
When dealing with flush water for slurries, it is crucial to ensure the process is not coming into the stuffing box. If particles entrap themselves within the packing, damage of the packing and shaft are likely to occur. This will also lead to reduced sealing quality.
Rather than assuming flush pressure to be 1 bar above discharge pressure, having flush pressure be 1 bar above the stuffing box pressure can be a better option. To determine stuffing box pressure, take the reading directly off the pump using a pressure gauge with the flush turned off. This may not be a possibility in all plants. This means that a calculation based on the system will determine this pressure.
Total Differential Head Pressure = (Pressuredischarge – Pressuresuction)
Equation 1
The type of pump and system will determine how the stuffing box pressure is calculated. Using actual data from a process will ensure more accuracy. A good starting place is to take 25 percent of the total dynamic head and add it to the suction pressure of the pump.
This formula may not be valid for end suction pumps that have balance holes in the impeller and split case pumps with double suction. In these cases, stuffing box pressure is usually equivalent to suction pressure. In the case of vertical pumps that do not have pressure breakdown systems in place, the stuffing box pressure is usually close to discharge pressure.
Depending on the pump and system, this equation may require modification. Using engineered throat bushing to help limit flush required in the system will further help lower the flush pressure needed. A full understanding of the system and equipment is key in determining optimal flush pressure, allowing flush pressure reduction and longer packing life.
The risks associated with assuming understanding of a system can be great. Believing higher pressure requirements are necessary when they are not will cause the gland to bottom out sooner. The lubricants will squeeze out of the packing as the packing over compresses. This can lead to high pressure leakage—a major safety hazard. Understanding the intricacies of a process will ensure that risks are avoided.
This formula may be found in the FSA’s Compression Packing Technical Manual, 4th Edition. The manual may be found at fluidsealing.com.
We invite your suggestions for article topics as well as questions on sealing issues so we can better respond to the needs of the industry. Please direct your suggestions and questions to sealingsensequestions@fluidsealing.com.
Read more FSA Sealing Sense articles by clicking here.