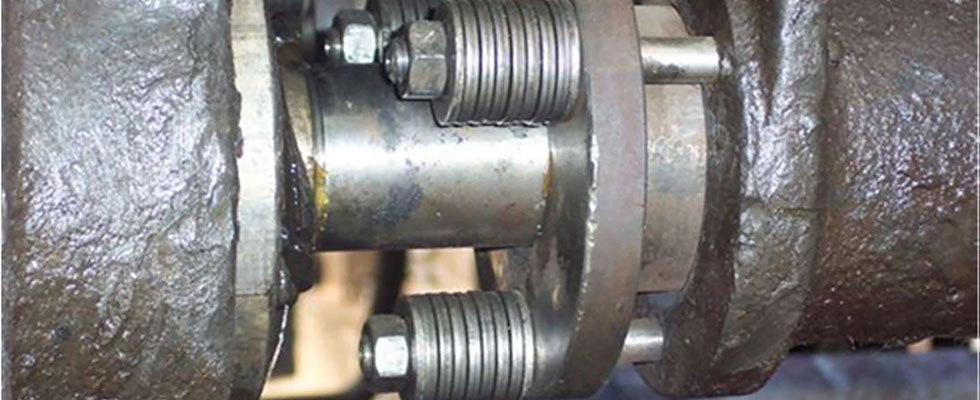
Modern day industrial operations utilizing rotating equipment are facing new challenges with a limited workforce while striving to increase productivity. Facilities are pushing production to perform at optimal levels while trying to achieve less downtime, lower cost of ownership and increased equipment availability. With technology rapidly advancing each year and the uprising of the internet of things (IoT), advanced sensors and new protocols have been created to monitor equipment remotely. Condition monitoring is becoming a widely practiced process to mitigate costly downtime and drops in production; however, it is often overlooked with rotating equipment sealed using conventional packed stuffing boxes. Taking advantage of remote sensor technology to monitor parameters such as vibration, temperature, power consumption and pressure can detect early signs of packing failure (thus decreasing unplanned shutdowns) and decrease the number of regular on-site inspections.
Figuring out these concepts and their relation to packing can get confusing. With all of the different sensors and parameters that need to be monitored, it is important to consider the needs of the specific facility and find the right solution adapted for the application. Outlined below are some of the parameters that can be monitored and their relation to performance of a packing set.
Gland Temperature Monitoring
- over-compression of the packing set
- overheating (glazing) of the packing
- gland nut adjustments during break-in
- troubleshoot packing failure
Temperature monitoring is considered an important practice to detect failure caused by bearings and seal faces but is often overlooked when mechanical packing is installed. Packing is compressed axially in the stuffing box by tightening the gland bolts (Image 3, C); this produces a radial force between the packing and the shaft/sleeve and stuffing box bore. This radial load produces a contact pressure on the shaft and bore that creates the seal, but it also creates frictional heat throughout the packing set. The temperature the frictional heat produces is an indicator that can help detect over compression, glazing or burning of the packing material. Sudden temperature changes can help predict potential product failure or allow for preventative maintenance. The temperature can be expected to increase during adjustments. It is important to have a good understanding of the packing material being used and the application it is being installed in to set limits as to what temperature is considered unstable or damaging to the product. The temperature at the gland does not often reflect the overall upper limit the packing is rated to since it is only seeing the temperature of the top rings. The frictional heat would be highest where the packing touches the rotating shaft, but it cannot be monitored easily. Typically, packing manufacturers recommend monitoring the packing gland temperature as it is relatively easy to do so. Note, in applications with higher temperatures, it is not possible for the operator to manually check the gland temperature. A laser pyrometer can also be used for maintenance checkups and during adjustments. Refer to the packing OEM for any questions about rated limits.
Installing a temperature probe with data acquisition into the gland for consistent monitoring of the equipment can be helpful in monitoring. Certain systems allow for alarms to be set once the temperature reaches a certain level. Increased measurements minimize the need for the operator to get close to the equipment posing potential safety hazards.
Gland Load
- over-compression
- loss of gland load and excessive leakage
- gland nut adjustments
Packed pumps rely on a loaded gland to maintain a compressive force on the packing in order to create a seal around the shaft and require periodic adjustments to the gland bolts to maintain consistent stress on the packing (Image 5). Over the duration of the packing’s life, the packing will consolidate due to wear and creep and can quickly lose load without periodic monitoring and adjustment. This can directly result in excessive leakage, solid embedment and premature packing failure. As the packing consolidates, maintenance crews are required to adjust and tighten the packing gland follower to bring the shaft seal back to a sufficient load.
It is not common practice to use bolt load measuring acquisition systems on rotating equipment. Instead, there is scheduled, in-person maintenance to observe leakage and adjust as necessary. This leads to costly downtime, safety concerns and overtightening of the packing gland. In many cases, the application may require the equipment to be shut down entirely to make an adjustment for safety reasons, e.g., personnel cannot be next to rotating equipment or the gland location is in a confined space.
There are bolt load measurement systems that exist but are rarely used on rotating equipment due to the fit and cost of the equipment. These systems are most commonly used on gasketed joints which are not considered in this article. For rotating equipment applications using packing, there are methods to reduce the loss of load over time and standard practices that can be followed to ensure even loading of the packing set is being applied.
The use of Belleville disc springs and flat washers under the gland nuts can help store elastic energy for when gland load is lost due to consolidation and help maintain the proper gland load (Image 4).
New hydraulic and pneumatic systems are being implemented and installed into the field that provide automatic and uniform gland adjustments remotely. These systems aid in preventing production losses due to premature packing failure and increase mean time between failure (MTBF).
Ensuring proper installation and tamping of the packing set can help reduce any risk of non-uniform gland loading. Good practice is to measure the gland engagement after installation to ensure it is uniform in different clocked positions.
Pressure
- pump upset conditions
- flush consistency
Pump systems work with a fixed amount of fluid that circulates through suction and discharge locations in which pressure can fluctuate, causing buildups of pressure beyond the rated limits of the pump and compression packing. Monitoring stuffing box pressure can aid in understanding the pump’s behavior and the exact conditions the packing is subject to. Many times, the stuffing box pressure is calculated based on the suction and discharge pressures, but these can only be calculated at a certain instance of the pump’s operation.
Increases of stuffing box pressure can lead to more leakage from the packing set if the gland is not adjusted to maintain a consistent leakage rate. Decreases in stuffing box pressure can lead to reduced or even zero leakage. This can eventually lead to overheating of the packing if a proper flush system cannot be installed, or the gland is not adjusted quickly after the change in system conditions. Acquiring this data will be able to troubleshoot packing failure and ensure proper selection of packing material is made.
Vibration
- equipment imbalance issues
- bearing damage
- shaft/sleeve misalignment
Rotating machines all vibrate while in operation with each producing its own baseline level of vibration. Changes in vibration levels or frequency can mean that the equipment is developing a degradation of a component or nonstandard operating condition. Over time, excessive vibration can damage the equipment and lead to potentially hazardous operating conditions.
There are many sources that cause vibration in pumps including bent shafts/shaft runout, change in pump alignment, operating off the pump curve, and contact between rotating surfaces and cavitation, among others. This can eventually lead to bearing damage and permanent indentations in metal components that then lead to increases in vibration. If these are severe enough, it can cause packing to wear and excessively leak. There have also been severe cases of the gland nuts loosening leading to the gland coming off entirely. Imminent pump packing failure can be detected by monitoring the overall vibration which will improve machine reliability, safety and MTBF.
There are a number of technologies and systems that have been invented to measure vibration. These systems typically measure change in vibration frequency, displacement and acceleration. It is recommended to source a system that stores the data which makes it easier to review patterns and changes over time. There are some sensors that can guide the technicians through the process of the equipment failure.
Power Consumption
- over-compression
- catastrophic failure
Most pumps operate off a motor that utilizes electrical current and converts it into mechanical energy. The radial loads and frictional drag of a packing set causes the motor to work harder. The stem/shaft drive mechanism has to adjust and overcome changes to dynamic friction due to increased load. Higher friction can affect performance and efficiency of the equipment and in excess can lead to increased power consumption and operating cost. Monitoring power consumption is indicative of early signs of increased friction which can eventually lead to damaged pump shaft or sleeves. This could also be used to monitor overloading of the equipment drive mechanism during startup and break-in.
Packed pump motors tend to have the most demand and friction during startup of the equipment. If the friction exceeds the maximum power of the pump motor, catastrophic failure and harm to the operator may occur. There are companies who supply pump load controls that are set for monitoring current, output and other operational parameters.
With all of these parameters taken into consideration, it is vital to select where and when to install a condition monitoring program. Target applications to start with are those with bad historical issues such as a pump with consistent leakage and MTBF with the packing set. Critical equipment to the facilities operations should also be considered as well as equipment that is in remote territories where normal maintenance is difficult to perform. Once properly implemented, it is important to properly interpret the data in order to have a successful condition monitoring program.
There are third-party automation sensors or data analysts that can be utilized if the resources are not readily available at the facility. Subject matter experts and packing OEMs can always be referenced for any questions pertaining to the material’s limits and behavior. Use this guide as reference to improve all equipment in the facility and to create a suitable condition monitoring program for packed rotating equipment.
We invite your suggestions for article topics as well as questions on sealing issues so we can better respond to the needs of the industry. Please direct your suggestions and questions to sealingsensequestions@fluidsealing.com.