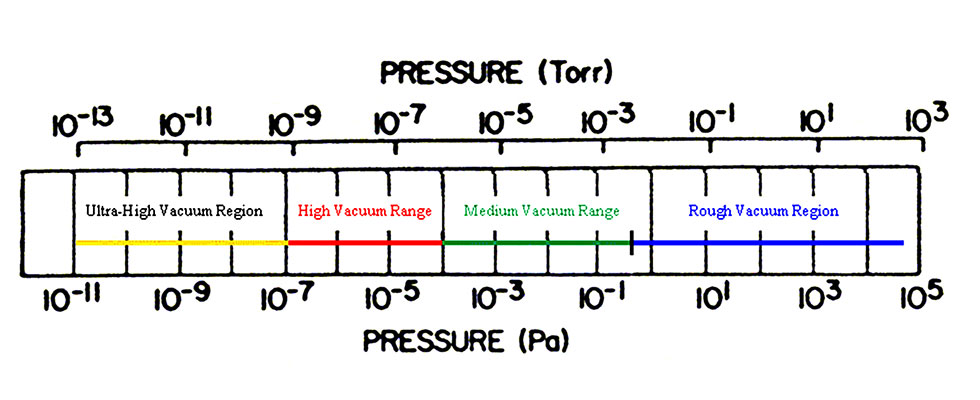
Vacuum is usually the term used when measured pressure is below atmospheric pressure. Atmospheric pressure varies—from the pressure measured in Denver, Colorado, which averages 843 millibar (mbar), to sea level in Houston, Texas, where the average is 1,013 mbar.
In the industrial, chemical and medical fields, a vacuum usually involves a sealed chamber, piping and a vacuum pump. The vacuum pump’s job is to remove molecules from the chamber.
System leaks in a vacuum system are also a challenge. A vacuum pump can be working properly, but if air is leaking into a system faster than the vacuum pump can pump the air out, the vacuum pump will likely be blamed. System leaks in a vacuum system can be difficult to find. As an example, a gasket or O-ring could have been left out during assembly of the system’s piping.
Leaks become more of a challenge depending on the vacuum range. The deeper the vacuum level, the more a leak can affect a process.
There are many different types of vacuum pumps. Choosing the right one to fit the application is often critical to the long-term success of the installation. Each type has pros and cons.
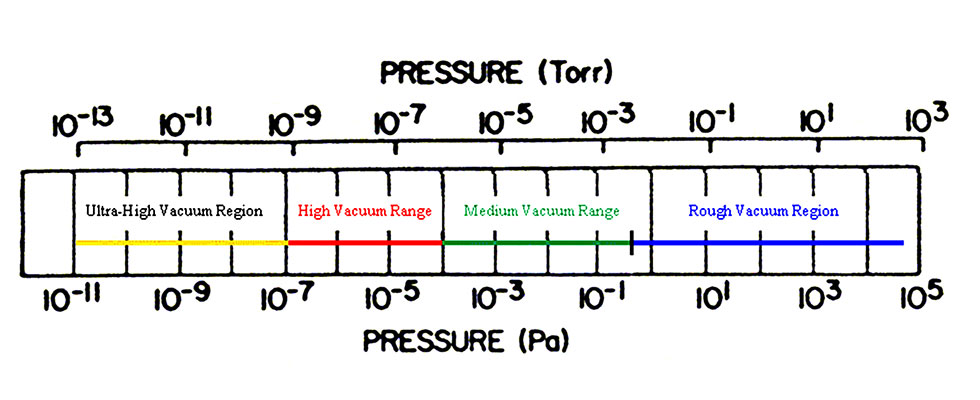
Thermal Electrical Power Generation
Regardless of the source of heat, electrical generating power plants use large vacuum pumps in two different parts of their operation; however, they do not call them vacuum pumps. Power plants use hogging pumps to remove the air from the turbine generator and steam condenser prior to starting up the plant from a cold start. Power plants also use condenser-exhausters or holding pumps to keep the steam condensers operating at peak efficiency (under vacuum).
Most commercial power plants were built between 1950 to 1970, some using inexpensive steam jets to create vacuum. Many are now in need of upgrades to operate at peak efficiencies. Steam jets create vacuum at specific conditions using a high velocity jet of steam. If a power plant starts and stops frequently, as is the case for a peaking plant, various piping welds, fittings, etc., may develop leaks and degrade the quality of the vacuum attainable with steam jets. A peaking generating plant is generally only brought online during times of peak power demand. The real operational problem is the longer pump downtime of the turbine and condenser, which causes there to be more time needed before the power plant can be brought online. In the case of a peaking plant, that time difference is directly related to selling the electrical power generated.
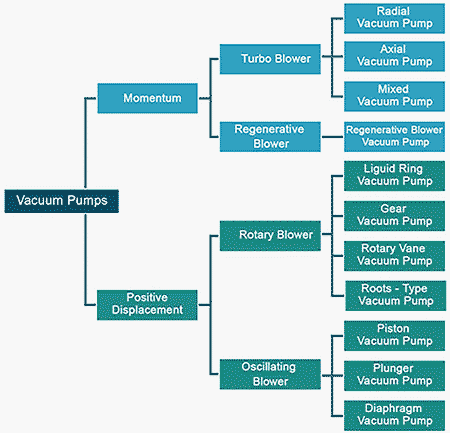
During normal steam condenser operation, the high-pressure steam (gas) is being condensed into water, and the subsequent lowering of the condenser water temperature creates voids in the condenser, lowering its surface contact and decreasing its efficiency. The objective of the condenser exhauster (vacuum pump) is to remove these voids, reestablishing the full efficiency of the steam condenser.
Typically, vacuum pumps are sized based on data from the published Heat Exchanger Institute steam tables. Because the total system volume is not known, the data on which the original steam jets were sized is usually no longer available. If the total volume is known, the pump down calculation is simple.
Large liquid-ring vacuum pumps are another option compared to steam jets. These condenser exhausters or holding pumps’ main purpose is to lower the condenser operating pressure and keep the steam condenser operating at the highest efficiency. Liquid slugs entering the vacuum pump from the condenser are generally absorbed without major issues. Large liquid-ring vacuum pumps are reliable, typically lasting five to seven years between overhauls (bearings and gaskets). After three to five overhauls, replacing major parts may be required to further extend the vacuum pumps’ service life.
When a vacuum pump and the process are matched well, a directly interchangeable unit would work best when a replacement becomes necessary.
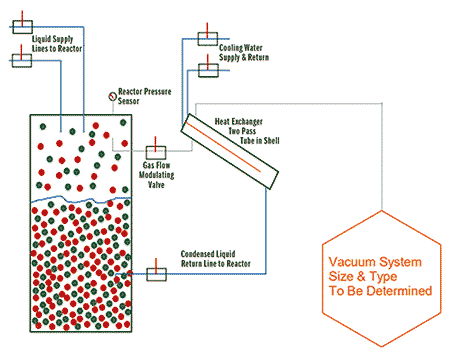
Vacuum Distillation
Vacuum distillation is used to separate two liquids that have similar vapor pressures or when heating liquids that could cause safety issues. For instance, ethanol production for use as a fuel additive relies on vacuum distillation to enhance and improve the ethanol yield from the fermentation process.
Ethanol production requires a source of glucose, which can be sugar cane, sugar beets, molasses, corn, wheat or grains. The fermentation process involves yeast converting the glucose into carbon dioxide (CO2) and ethanol. The CO2 gas can easily be vented or captured, and the ethanol is often stripped off the original biomass slurry via vacuum distillation.
The vacuum pump is an essential part of a system. If the vacuum pump is failing too often, experts are frequently called in to diagnose the cause of the failures and to recommend solutions.
Should a larger volumetric capacity vacuum pump be installed to shorten the overall process time, an unintended consequence may be the larger liquid volume traveling past the system condenser. The size of the condenser and the gases dwell time are important factors in the time it takes to recondense the gas to a liquid. Moving the gas through the condenser quicker by using a larger volumetric capacity vacuum pump can change the composition or ratio of the materials and the amount of liquid entering the vacuum pump.
Thinking of switching to a dry vacuum pump? Not all dry vacuum pump designs are the same. Some do not handle liquid contamination ingestion well and may fail frequently when 10% to 15% or more of the material entering the vacuum pump is a liquid (vacuum pumps are only designed to process gases).
Vacuum pumps are at the heart of many industrial, medical and chemical applications. Sometimes a simple vacuum pump or blower replacement is the best solution, but when faced with a more complex reliability issue, a systems approach will be needed to determine the best solution for the user. A systems approach may require changing the type of vacuum pump (utilities, piping, etc.) to meet the user’s needs.