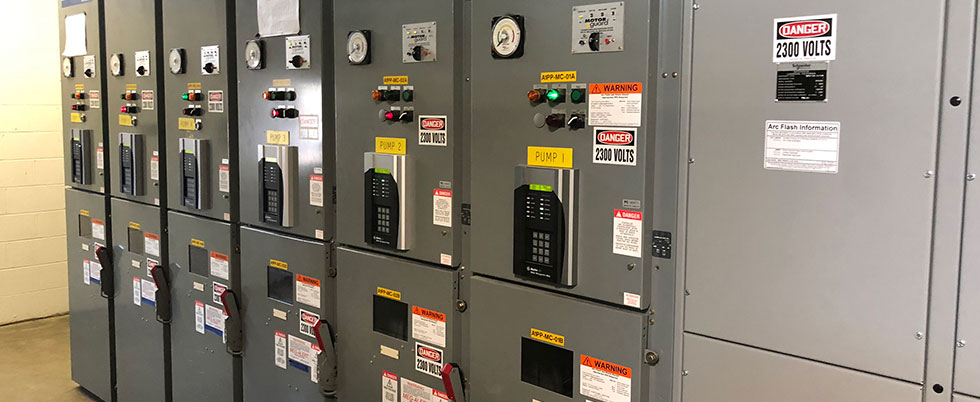
For decades, pulp and paper plant personnel have performed manual insulation resistance (I/R) tests with handheld megohmmeters to prevent motor failures that can lead to unplanned shutdowns and expensive rewinding repairs. These manual tests only provide a snapshot of the motor’s health. Between tests, even in a matter of days, motor windings and cables exposed to moisture, chemicals, contaminants or vibration can become compromised and fail at startup.
Portable megohmmeters also require electrical technicians to manually disconnect the equipment cables and connect the test leads on potentially energized or damaged equipment to perform the testing. The manual tests expose technicians to potential arc flashes when they access the cabinet.
Another solution is to employ continuous megohm testing and monitoring of insulation resistance, which initiates the moment the motor is off until it is restarted again. Permanently installed automatic testing devices also allow for hands-off monitoring without having to access cabinets, keeping technicians out of harm’s way. Armed with real-time information from continuous monitoring, maintenance personnel can take corrective actions ahead of time to avoid a catastrophic failure that would interrupt production or incur expensive repair fees for rewinding.
Motor Protection at Pulp & Paper Plants
Pulp and paper mills use thousands of motors, with about a third of them being considered critical. Critical motors are those that could impair the ability to safely meet business objectives or affect production levels if unexpectedly offline. Such motors can range from feedwater pumps and forced draft fan motors for boilers, to water pumps and paper machine pumps. Typical paper mills have 3,000 to 4,000 horsepower (hp) motors for boiler feedwater pumps or paper machine fan pumps to spread the pulp out. Critical motors can be as large as 15,000 hp for some boiler feedwater pumps.
Most companies attempt to maintain their critical motors through time-based preventative maintenance (PM) programs. I/R tests are typically scheduled on a semi-annual basis, or at the start of annual overhauls or planned outages; however, given recent reductions in personnel, it may be less frequent. The results of these tests are needed so corrective action can be scheduled before a failure occurs. Despite using PM programs, motors that are offline or are frequently cycled can be quickly compromised. Preventing failures such as downtime is crucial to maintaining maximum plant reliability and a healthy bottom line.
While pulp and paper plants attempt to keep an adequate supply of spare motors on hand, if purchasing a new critical motor is required, it can typically take 16 to 20 weeks, or even six to nine months, of lead time before receiving a large synchronous motor. To best avoid such scenarios with critical motor failures, one paper company in South Carolina initiated a policy that requires any motor shut down for four hours or more be tested by a megohmmeter before it is started.
One challenge they found with using manual megohmmeters to do this type of testing is that the devices did not always provide the necessary consistency due to subjectivity between technicians. Another problem was that the devices could only provide spot-checking, which lacks accuracy as soon as environmental conditions, such as temperature or humidity, change.
Engineers decided to install an automatic continuous megohm testing and monitoring system, on a critical standby pump that required the ability to start immediately, if needed. Testing initiates the moment the motor is off until it is restarted again. These permanently installed automatic I/R testing devices allow for hands-off monitoring without having to access motor control center (MCC) cabinets, keeping technicians out of harm’s way. Armed with real-time information from continuous monitoring, maintenance personnel could now take corrective actions ahead of time to avoid a failure that would interrupt production or incur expensive repair fees for rewinding.
Hands-Off Monitoring
The unit is permanently installed inside the high-voltage compartment of the MCC or switchgear, and directly connects to the motor or generator windings. The unit senses when the motor or generator is offline and then performs a continuous dielectric test on the winding insulation until the equipment is restarted. The continuous monitoring system also allows for a hands-off approach that does not require service technicians to access control cabinets to perform a manual insulation resistance test.
Instead, an analog megohm meter outside on the control cabinet door shows the insulation resistance megohm readings in real time. The meter also visibly indicates good, fair and poor insulation levels through a green/yellow/red color scheme. When predetermined insulation resistance set point levels are reached, indicator lights will turn on to signal an alarm condition and automatic notifications can be sent out to the monitoring network.
Continuous monitoring can also show if the heaters used to maintain thermal temperatures and prevent condensation are working properly. Most motors use heaters to maintain the temperature inside the motor so it does not vary drastically from operating temperature or ambient temperatures outside the unit. If it goes below the dew point, the motor will start picking up condensation while offline. However, if these heaters fail to operate properly or the circuit breaker is tripped, plant personnel may not be aware of it until the motor fails on startup. Although these motor heaters are checked regularly, critical motors can remain unprotected for weeks or even months.
Maintenance Savings
Manual megohm testing before each startup will help prevent failures. However, that type of testing requires operations to set aside time for the motor to be locked and tagged out and man hours are expended to perform the testing. Automatic continuous I/R testing eliminates both requirements.
Increased Personnel Safety
Enhancing employee safety and preventing potential harm from arc flash was another key factor behind the decision to install the continuous insulation resistance testing and monitoring devices.
Arc flashes are an electric discharge that travel through the air between conductors or from a conductor to a ground. The flash is immediate and can produce temperatures four times that of the
surface of the sun. The intense heat also causes a sudden expansion of air, which results in a blast wave that can throw workers across rooms and knock them off ladders. Arc flash injuries include third degree burns, blindness, hearing loss, nerve damage, cardiac arrest and death. Among the potential causes of an arc flash listed by the National Fire Protection Association (NFPA) 70E includes improper use of test equipment.
Although deenergizing equipment before testing and wearing appropriate personal protective equipment (PPE) is recommended, a solution is to eliminate the need to access control cabinets to perform insulation resistance tests.