Combined monitoring and control software options help provide flexibility and improve uptime.
05/14/2015
We live in uncertain times when the price of oil can drop by 50 percent in a matter of months. To combat this uncertainty, the pump industry must focus on maximizing efficiency and throughput while maintaining health, safety and environment (HSE) standards. Because rotating equipment is so prevalent in the oil and gas industry, this can be achieved, in part, by increasing the uptime of the pumps and rotating equipment producing and refining oil and gas.
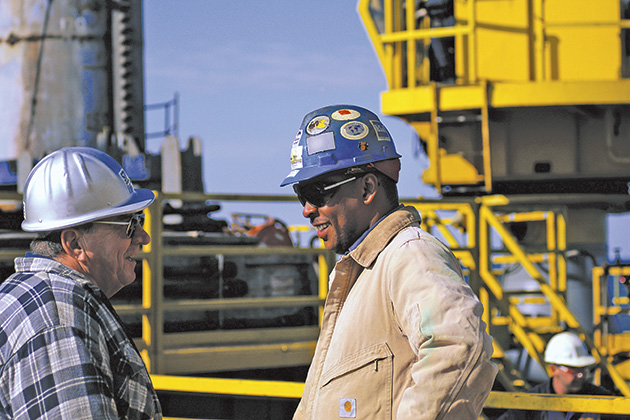
Scheduled Maintenance
Most people are conditioned to follow a regularly scheduled maintenance program as the best way to keep equipment in pristine working order. Employing a regularly scheduled maintenance program to save money on expensive equipment repairs and improve machine efficiency should be easy. The reality, though, is that the cost of these programs is sometimes higher than running the machine to failure because, time and effort are wasted fixing something that is in perfect working order. The costs of safety problems caused by catastrophic failures is also significant. Although the likelihood of the failure is lessened by scheduled maintenance, an unplanned or even catastrophic machine failure is still possible if a part of the machine fails before its manufacturer's recommended repair time.The Cost of Maintenance
To understand the costs associated with maintaining rotating equipment, the Electric Power Research Institute (EPRI) calculated the comparative maintenance costs for different techniques per horsepower (HP) per year. Researchers discovered that a scheduled maintenance strategy is actually the most expensive to run at $24 per HP. A reactive maintenance strategy (run to failure) is the second most costly at $17 per HP, but this method has the additional cost of potentially compromised personnel and equipment safety. Drawing a parallel to pumps used within stimulation and hydraulic fracturing, a 1,500-HP motor would cost approximately $36,000 per year while a reactive maintenance strategy would cost $25,500 per year, according the EPRI study. That amount does not seem like much, but when multiplied by the number of stimulation and fracturing units across the entire fleet (in some cases, around 1,500), the cost skyrockets to $54 million per year for a scheduled maintenance plan and $38 million for a reactive strategy. The equipment must be maintained, but a better strategy is needed. Equipment maintenance has become such an important topic that, according to Forbes Magazine, "one out of every three dollars spent on preventive maintenance is wasted." Examining the maintenance costs and mismanagement of large assets across a fleet can provide an understanding of the maintenance costs, but it only begins to tell the story of the true cost of equipment mismanagement.Mismanagement Example
To identify the true cost of equipment mismanagement, a production-level view of the issue is required. Although repairing a pump may cost $36,000 and the capital costs of a new triplex or quintaplex mud or hydraulic fracturing pump can cost approximately $350,000, the true loss is in production. Because cash flow is directly tied to production in the oil and gas industry, a negative economic impact occurs when drilling stops at a wellsite. This is further compounded if the failed equipment is a hydraulic fracturing pump, which may halt the work of the fracturing crews on site. Reliability is critical, and companies often bring several backup trucks that may or may not be needed because they do not know if their pump will fail, even if it has just been serviced. Rather than trying to extend pump life by simply having backups in case machinery failes, pump users must employ a better strategy—incorporating remote monitoring into their maintenance program.A Condition Monitoring & Control Solution
One software-designed controller tightly integrates a real-time processor with a user-programmable, field-programmable gate array (FPGA) and modular input/output and is programmed with system design software. End users can embed their algorithms into hardware using software techniques without the difficulty of custom design. With this approach, users can build control and monitoring systems that are unique to their applications but flexible enough to be deployed on a broad scale. By using a single hardware and software platform, one company's engineers were able to control and monitor every aspect of the well servicing and stimulation equipment commonly found in their industry. The company had a highly reliable control system that could measure a multitude of sensors, perform high-speed analysis and transfer that data back to the main hub through the Society of Automative Engineers (SAE) J1939 communication protocol. A platform-based approach can help end users meet today's needs and future requirements and deploy a network of predictive maintenance systems designed to communicate with each other in real time to keep their machines operating longer and more efficiently.3 Ways to Get More Years from a Pump
- Use Vibration Monitoring. Vibration monitoring allows end users to gain insight into the health of their pumps. Through proper analysis, vibration monitoring can serve as a core element to a predictive maintenance strategy. In the EPRI study, researchers found that this new option costs only $9 per HP and nearly eliminates the risks of secondary damage from catastrophic failures. A predictive maintenance strategy should not replace safety systems but should work alongside them. This strategy also extends pump life by detecting small anomalies before they become catastrophic failures.
- Go Beyond Vibration. Vibration measurements act as the best indicator for the health and life expectancy of a pump, but they are not the only indicator. Monitoring measurements such as temperature, strain, power quality, pressure and deflection also gives insight into a pump's health. When vibration monitoring and operating parameter monitoring are combined, they can provide a much clearer picture. Going beyond vibration is typically the second phase of condition monitoring. If it is not planned for, however, condition monitoring becomes difficult and expensive to add later. A platform-based approach that can adapt to changing requirements is needed.
- Integrate with Control. The final step for end users to regain control of their assets is to completely integrate the condition monitoring solution with a control platform. By choosing a flexible platform in step one, all the elements measured in steps one and two can be used to adjust the control algorithms in real-time, based on the operating conditions, to improve efficiency and extend the life of the pump.