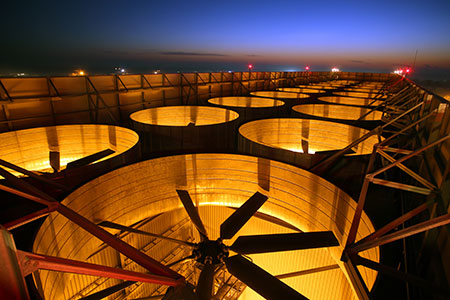
As the industrial and commercial cooling landscape evolves, the cooling tower industry faces challenges that call for innovative and efficient responses. From the increasing demand for energy-efficient designs and ever-changing regulatory requirements to the complexities of ongoing maintenance, cooling tower OEMs and their users must navigate numerous obstacles. Several key trends and emerging technologies are shaping the future of the cooling tower industry, helping to redefine performance, efficiency and sustainability for these systems.
Cooling Tower Basics
Many think of cooling towers as large, chimney-like structures outside nuclear power plants, but cooling towers can also be found at hospitals, shopping malls and factories. And these towers do not look or operate like the stereotypical structure.
Cooling towers are a necessary component of industrial facilities and other large buildings. They use large fans to chill water for air conditioning, power generation and other processes. The motor generates power to turn the large fans. The fan draws air over the water, reducing its temperature before distributing it back to the process for cooling. Cooling towers rely on components like gear drives, couplings and brakes. Large facilities may have dozens or even hundreds of cooling towers at a single site.
Challenges for Cooling Tower OEMs & Users
Cooling tower systems must be reliable and able to withstand harsh environments. Downtime for equipment maintenance, breakdowns and replacement can be costly. Consider these key challenges faced by equipment manufacturers
and users.
Lead times: Facilities cannot wait a week to get a quote when they need a new system or part replacement. They want solutions within days, not weeks, to keep systems up and running. Long lead times can result in downtime and costly long-term shutdowns.
Costs: Maintaining system performance and safety while also managing costs is a key priority for many facilities. They want reliable and durable solutions in a timely but also cost-effective manner.
Ongoing maintenance: Issues such as corrosion and scaling can impact the performance and longevity of cooling towers, necessitating regular maintenance. And as with all mechanical equipment, breakdowns happen in the field. Tower equipment failures happen year-round, but more failures happen during warm weather as the fans and supporting equipment work harder in higher temperatures. No matter the failure’s cause, cooling tower operators will eventually need to replace couplings or gear drives (or sometimes both). These vital components are responsible for transferring power to the fans. Equipment failure and downtime can cost facilities tens of thousands of dollars. When components like couplings or gear drives break, the best option is to get replacement parts from the manufacturer.
Safety: The large fans inside towers can be dangerous for workers who oversee and maintain them. When workers must go near or enter the tower, the spinning fan (or even the possibility that a fan can get up to speed) is a hazard. Tower cells do not provide much space, and workers are often right up against the fan. When a fan with a 12- to 35-foot diameter starts to spin, there is a lot of power behind it. And even when the motor is locked and tagged out, the fan can still drift.
Key Trends in the Cooling Tower Industry
The cooling tower industry is experiencing several key trends driven by technological advancements, regulatory changes and an increased focus on sustainability.
Trend 1: More focus on sustainability and energy efficiency
Cooling towers are significant energy consumers, and there is a growing demand among some system designers and facilities for more energy-efficient models to reduce operational costs and provide greener solutions.
Hybrid cooling towers are a response to this trend. These tower designs combine wet and dry cooling methods to enhance sustainability and conserve water. They also use more sustainable methods to return the water to the system. Hybrid cooling towers minimize the water lost through evaporation. With reduced evaporation, there is less concentration of dissolved solids in the remaining water, decreasing the need for water treatment and blowdown cycles and further reducing water waste.
Trend 2: The rise of automation and predictive maintenance
The adoption of Internet of Things (IoT)-enabled and automation technologies can improve monitoring, control and predictive maintenance of cooling towers. This makes equipment monitoring and predictive maintenance a growing demand among some system end users. Unplanned cooling tower failures can shut down a facility, and cooling towers can have undiagnosed issues that go overlooked until an unexpected failure occurs.
IoT-enabled capabilities—such as remote condition and predictive monitoring—can help facility managers proactively take action and avoid unplanned downtime by staying in tune with current conditions without needing to climb towers or expose teams to harsh environments. Solutions like remote condition monitoring and predictive maintenance can help industrial maintenance teams keep equipment up and running longer, schedule maintenance and avoid unplanned downtime, all while extending equipment life. In cooling tower applications, these solutions can be used for remote vibration and temperature monitoring of gear drives and motors as well as to monitor the basin pump area. This can provide early detection of fan or shaft imbalance, misalignment, water level drops and gearbox or motor bearing issues.
Trend 3: Increased use of modular designs
Modular cooling tower designs, which can provide greater flexibility and a lower threshold of entry cost, are growing in use. There are several types of cooling tower designs that fall into this category.
The first is often referred to as prepackaged towers. These are built by a manufacturer and then delivered to a facility in pre-engineered and factory-assembled sections. This reduces on-site installation time and costs. They often have plug-and-play designs with standardized connections and interfaces for quick setup and integration into existing systems. The scalable nature allows facilities to add more units as their cooling needs change.
Another category of modular cooling towers are air-cooled condensers (ACCs). These are also built by a manufacturer and then shipped to a facility to be assembled on-site. ACCs are closed systems that reject heat from a process by transferring it to the surrounding air, eliminating the need for water in the cooling process. Because ACCs don’t use any water, they are a popular choice for facilities that place a high priority on water conservation—often in drier environments where water is at a premium. However, they do require a lot of land, so that is a consideration to keep in mind. In addition, it may take many more ACCs to meet cooling requirements compared to a traditional cooling tower design, so that impacts a facility’s investment.
Trend 4: Changing regulatory and safety compliance
The cooling tower industry must comply with a variety of environmental regulations, including those related to water usage, chemical treatments and emissions. The Environmental Protection Agency (EPA) is updating regulations governing the cooling tower industry with the aim of improving safety and sustainability. Technology must be able to meet standards for safety and environmental compliance, as conservation becomes more critical now and into the future for the industry.
Addressing Trends & Challenges
In response to these challenges and changing priorities, cooling tower system designers and end users are looking for more efficient, more sustainable technologies. In some cases, this is driving design updates as well as placing even more importance on choosing reliable, cost-effective equipment and solutions.
Optimizing Cooling Tower Applications
Selecting the right cooling tower solutions for an application can help facilities increase energy efficiency, boost system performance and streamline operations.
Bundling components is a good way to simplify the purchasing process and lower shipping and logistics costs. Look for a solutions provider that offers a wide range of reliable solutions, from couplings and brakes to gear boxes, along with ongoing support for project and replacement as well as maintenance, repair and operations (MRO) business. Product availability and lead time is another critical consideration in product selection: Operations can minimize downtime by choosing products that are backed by short lead times and wide availability.
Today’s cooling tower solutions can be tailored to withstand the challenging conditions of these applications, where water, debris and harsh chemicals are present and continuous peak performance is critical.