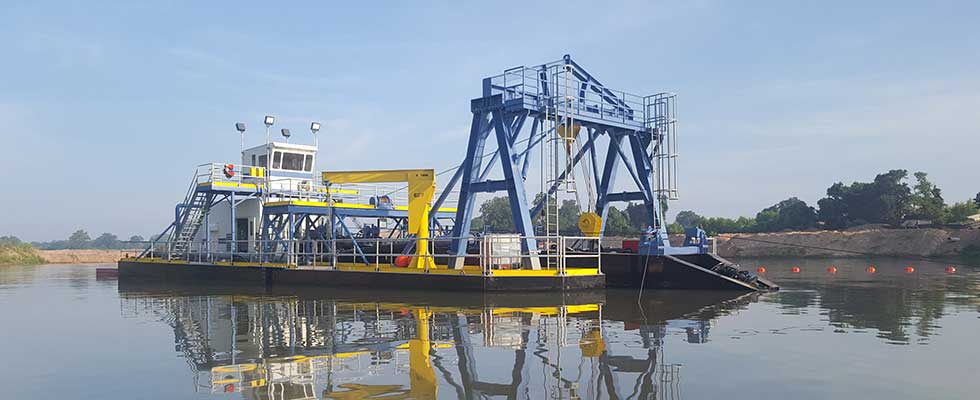
Dredging is the removal of sediments and debris from the bottom of lakes, rivers and other bodies of water. Dredging is often focused on maintaining or increasing the depth of navigation channels to ensure the safe passage of boats and ships. Dredging is also performed to reduce the exposure of fish, wildlife and people to contaminants and to prevent the spread of contaminants to bodies of water.
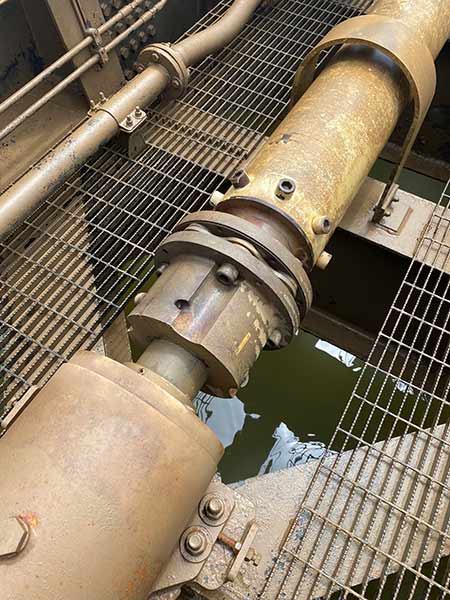
The pumps on a dredging vessel are critical to the operation of a dredge. The main pump of a dredge is a heavy-duty slurry pump. The dredge also has at least one service pump that is used for main pump packing, hydraulic cooling, water blasters and jet-assist if needed. The service pump is either a vertical turbine or a centrifugal pump. There are also various hydraulic pumps used on a dredging vessel.
Dredging vessel manufacturers are focused on designing and manufacturing dredges that offer high value and strong return on investment. To achieve this, the manufacturers often partner with suppliers to bring different areas of expertise together to arrive at an optimal solution. This is especially true for driveline development for dredge pumps.
Specifying the Pumping Requirements
It is helpful to answer several questions when specifying a pumping system for a dredge.
1 - How deep does the dredge need to operate?
For shallow depths, it is most efficient to install a pump in the hull of the vessel. For deeper requirements when a ladder dredge is used, a jet-assist for the suction of the pump may be required. Alternatively, the pump can be placed near the end of the ladder, so the pump does not have to work as hard to get the material up the ladder.
2 -How far does the material need to travel to reach the processing plant?
If there is a long distance between the dredge and the processing plant, a second or third pump called a booster pump may be needed to help move the material to the plant.
3 - How much material is required to move through the plant?
This usually determines the size of the pump. The material flowing to the plant is measured in tons per hour.
4 - What type of material is being pumped?
The type of material can affect how well the material flows through the piping.
Challenging Operating Environment
Underwater pumps operate in wet, dirty environments with sand and grit often surrounding the pumps. In-hull pumps have cleaner environments on the outside, but the environments the pumps experience on the inside are just as harsh. Along with the material going through the pumps, which act like aggressive sandblasters, there can also be large rocks, tree branches and other miscellaneous material that can impact the pumps.
Selecting the Drive System
After the style of dredge and pump are determined, the driveline can be selected. If the dredge is in-hull, there are several options: use a direct drive through a gearbox; use a marine transmission; or use a belt drive. If the dredge is a ladder design with the pump on the ladder, the driveline design will require torque tubes with couplings on either end of the tubes supported by bearings, all suitable for underwater usage.
Ladder Dredge: Driveline Considerations for the Dredge Pump
The driveline allows mechanical power to be transferred from the engine or motor to the dredge pump. During operation, the driveline faces a harsh environment just like the dredge pump. The driveline needs to operate under conditions with periodic shock loading, dynamically changing misalignment, and a sandy, abrasive underwater environment. In addition to operating reliably in a harsh environment, the installation of the driveline needs to be efficient and cost effective.
Coupling Selection for the Driveline
Disc couplings are the primary couplings chosen for driving a dredge pump on a ladder dredge. The nonlubricated design of the disc coupling does not require any special sealing. In addition, the use of corrosion-resistant materials and coatings is relatively economical. The following are several areas considered when selecting a disc coupling to drive a dredge pump on a ladder dredge.
1. Torque density
The torque density of the disc coupling is an important factor to consider. The most common definition of torque density is the continuous torque rating of the coupling divided by the mass of the coupling. The higher the torque density, the lower the coupling mass for a given torque. With higher torque density and resulting lower mass, the coupling causes less of a bending moment on the driveline. This reduces vibration levels and can increase the life of bearings and seals. Torque density is critical to ensuring the driveline has a long, useful life and the uptime of the dredging vessel is maximized.
2. Durability
The disc coupling must be able to handle the shock loading and vibratory torque the driveline will experience. At the same time, the coupling must be able to handle the dynamic misalignment of the driveline during operation. The disc coupling must do this while operating underwater, so proper materials and corrosion-resistant coatings must be selected. The disc coupling also needs to be sized appropriately. The torque rating of the disc coupling along with the appropriate service factor are important when selecting a coupling size.
3. Ease of installation & ease of service
Ease of installation and service of the disc couplings are also critical aspects to consider. The first consideration is how the disc couplings will be integrated into the torque tubes. The disc couplings will either be welded to the tubes or attached to the tubes with fasteners. Fasteners offer several advantages over welding during initial installation. These advantages include improved driveline quality with less material deformation due to heat and less installation time. Also, a coupling installed with fasteners is significantly easier to manage in the field if the driveline ever needs to be serviced. It is preferred to use standard fasteners in these applications since standard fasteners are readily available and relatively inexpensive.
4. Cost factors
Cost is an important factor when making the driveline design and disc coupling selections. The opportunities to improve costs can be seen in several areas such as initial coupling cost, installation time, driveline quality and field maintenance of the driveline.
Collaborative Driveline Design & Vessel Integration
With new dredge applications, it is helpful for the dredge manufacturer and the disc coupling manufacturer to work together to integrate the disc couplings into the driveline design. This will ensure the performance, reliability, cost and all other requirements of the driveline are considered. It is important to analyze the driveline as an entire system since all components must work together seamlessly. This includes the disc couplings as well as the other components of the driveline.