Keeping aging facilities and equipment maintained is an ever-changing task that can jeopardize the goal of maximizing uptime. Years of thermal cycling, vibration or foundation settling can disorient piping or pumps. Piping engineers will use rubber expansion joints to account for these types of challenges in a rigid piping system. Permanent misalignment can set in after years of operation. The original-size expansion joint could no longer be the best fit when it comes time to replace. Replacing a permanently misaligned expansion joint connection with the original part could lead to reduced service life and/or missed expectations of the new expansion joint. Determining the best way to accommodate this when it comes time to replace the existing expansion joint can have long-term effects on reliability. Since the original components may not fit in the newly disoriented flange connection, they are limited in their reliability.
Types of Customization & Benefits
Expansion joints are designed to withstand the pressure retention of rigid pipes, yet be flexible and absorb misalignment induced in these systems. However, there are limits to exactly how much flexibility can be absorbed before damage occurs. Using this flexibility to connect two misaligned pipe flanges will take away from how much movement can be absorbed during the actual operational period when the system is running. Attempting to retrofit a standard-size expansion joint to connect a misaligned pipe connection can put excessive stress on the component and could lead to a shorter operational service life. For this reason, the Fluid Sealing Association (FSA) recommends no greater than ±1/8-inch misalignment of the pipe flanges during installation. Depending on the severity of misalignment, it can be advantageous to implement a custom-sized expansion joint to minimize the stresses that cause these joints to fail or become damaged during installation. Maintenance crews can also benefit by having a component that will fit precisely. Concerns for safety are present when attempting to put enormous pressure to compress, elongate or offset the joint so it will fit in place. Custom, made-to-fit expansion joints provide long-term dependability and can be designed in many orientations. To prevent overexertion, expansion joints are often constructed to connect nonstandard distances between pipe flanges. Other modes of misalignment can connect pipe flanges that are no longer centered.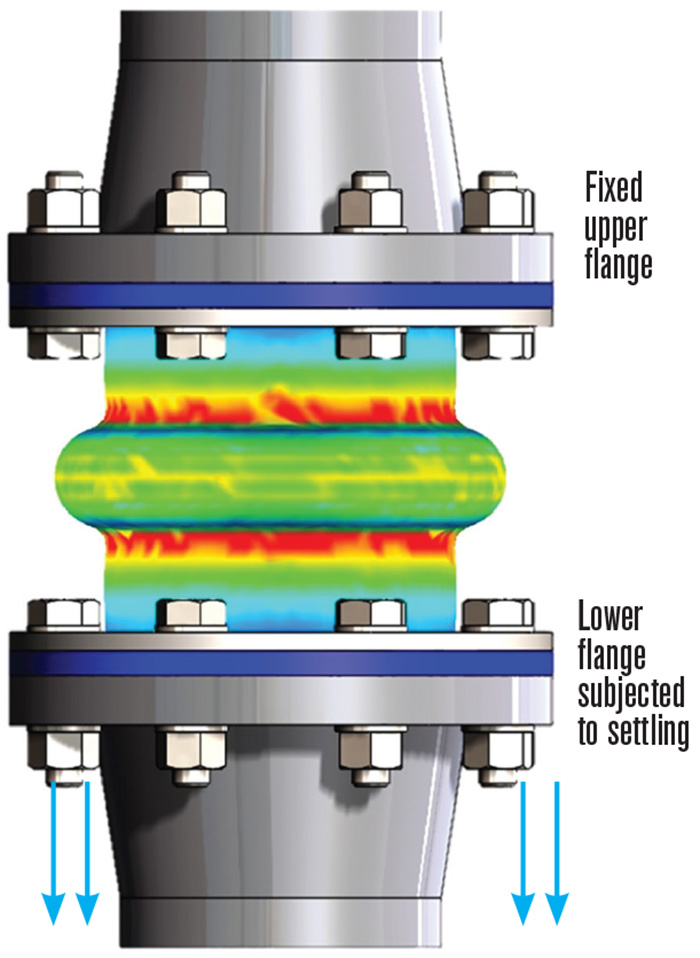
Face-to-Face Tailoring
Years of cycling, wear and other factors can contribute to the disorientation of a particular pipe connection. The length of an expansion joint, a dimension commonly referred to as face-to-face, bridges the gap between two parallel pipe flanges. A common industry problem is created when foundations settle and piping support structures transition lower than where it was originally constructed (Image 1). Expansion joints are designed to account for this, but choosing the correct replacement will make the difference between continued reliable service life or system failure. Stretching an expansion joint to fit the changed flange connection often results in immediate damage that is only sometimes visual to the naked eye. A stress point on the outer cover of the expansion joint will usually become visible at the transition corner between the flat portion and the base of the arch in the form of a crack. The severity of cracking, elongation and settling will be aggravated when pressure in the pipeline is turned on. Depending on nominal pipe size, industry standards will include standard face-to-face sizes of 6, 8, 10 or 12 inches, according to the FSA. When a standard 6-inch face-to-face joint is removed, the length between flanges could have been elongated to 7 inches or more. Many expansion joint consumers are not aware of the capability to build the expansion joint to the required nonstandard 7-inch face-to-face since it is not a standard offering. Building the replacement expansion joint to the nonstandard 7-inch face-to-face will eliminate any initial stress imposed on the joint.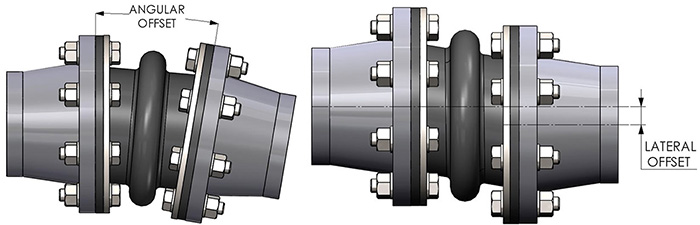
Lateral & Angular Offset
When the foundation of a pump begins to settle, the horizontal suction line feeding in from a separately restrained pipe can also cause misalignment. If a standard-size expansion joint is installed in the newly offset pipe opening, the joint will need to be forcibly displaced to make the connection. As a result, the reinforcing materials of the expansion joint will be under stress immediately and could lead to a much shorter service life. The rate of deterioration on this joint is higher compared to one that is not forcibly manipulated and is under little stress from the first day of operation. Understanding the type of offset that is required in designing a custom replacement joint is crucial for ensuring the best fit. If the flanges are still parallel but not centered, this is referred to as lateral offset. Misalignment can also occur when the flanges are centered but are no longer parallel. Referred to as angular offset, this is most similar to an elbow connection. Combinations of both lateral and angular offset also exist in cases of severe misalignment.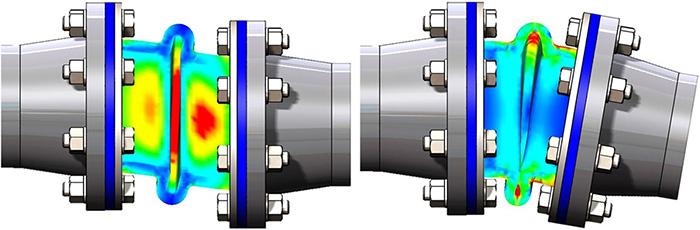
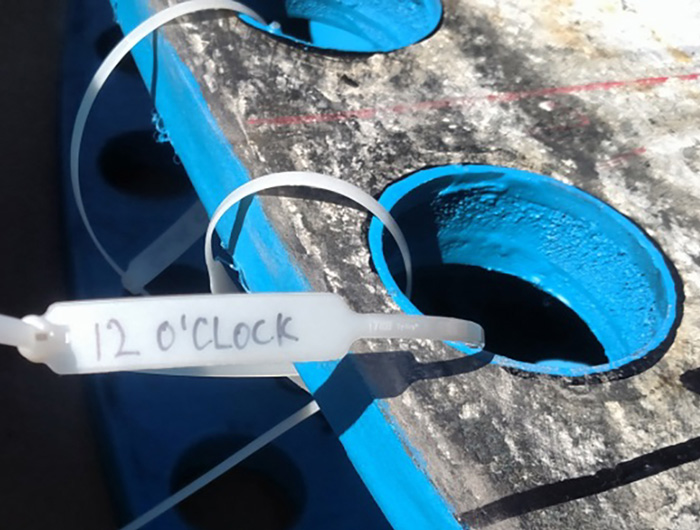