Gaskets are crushed more frequently than many end users realize. Some maintenance professionals claim that is all they see when they separate a leaking flange. Many simply replace the gasket rather than investigating the cause of the failure in depth. Gasket crush is a significant threat to plant reliability. This problem causes leaks, which can lead to a dangerous plant situation, especially if a hazardous fluid is involved. This issue is unpredictable and introduces variability into plant operations. All types of gaskets—metal, nonmetal and composite—experience gasket crush. If a gasket design fails on the first installation, plant personnel can replace it with a new design during the next plant shutdown. However, if a gasket has worked nine times without a problem, then leaks on the tenth installation because of gasket crush, an unplanned maintenance response is required. Users have two options for reducing gasket crush: better torquing procedures, which can be difficult, and better gasket design, which is easier to implement.
Torquing Procedures
In a crushed gasket, different compression patterns are visible—sometimes on one side of the gasket, sometimes on opposite sides and sometimes all over the gasket. These patterns point to over-compression. The most obvious conclusion is that something was wrong with the torque, even though sophisticated torque equipment, such as torque wrenches or bolt tensioners, is often used during installation.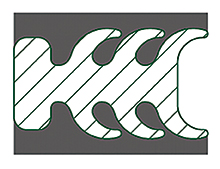
- Bolts must be well-lubricated with a lubricant of known coefficient of friction, because unlubricated bolts can consume up to 50 percent of the torque load.
- Torque typically is calculated based on the bolt material, not the required load of the gasket material, which is usually too high for the gasket need.
- Personnel only have access to a recommended bolt load for the cool flange when the operation has not yet started. The crucial hot torque load value is rarely available.
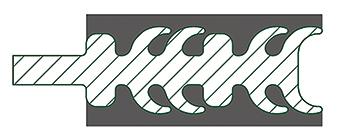
Gasket Design
Designing better gaskets is a much easier solution in practice than attempting to deal with torquing procedures and the art of hot torquing. Spiral-wound and camprofile gaskets are the most commonly used metal gasket types. The compressibility and elasticity of spiral-wound gaskets are useful sealing characteristics. When paired with the strength that a camprofile gasket achieves through its unitary metallic structure, gaskets start to approach optimal design.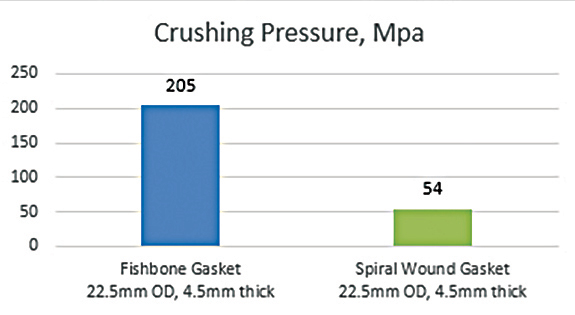
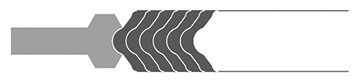
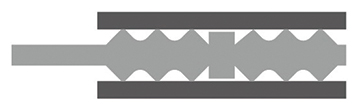
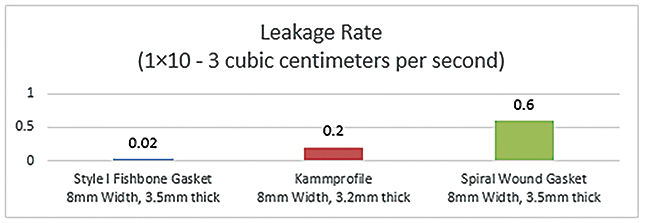