In 1988, the Environmental Protection Agency (EPA) issued regulations for underground storage tanks (USTs) and piping systems that handle petroleum products and hazardous chemicals. In 2015, regulations that affected owners and operators installing secondarily contained tanks and piping were revised. Owners and operators must use interstitial monitoring as release detection for these new or replaced tanks and piping. EPA regulation 40 Code of Federal Regulations (CFR) 280 lists more than 800 chemicals that are considered hazardous and have to be double-contained. The Resource Conservation and Recovery Act 40 CFR 280 defines USTs as any tank system, including any piping connected to it, with at least 10 percent of its volume underground.
State environmental guidelines and enforcement may exceed those of the EPA. States with an approved UST program have the lead in UST/piping enforcement where states without an approved program work with the EPA to coordinate enforcement actions.
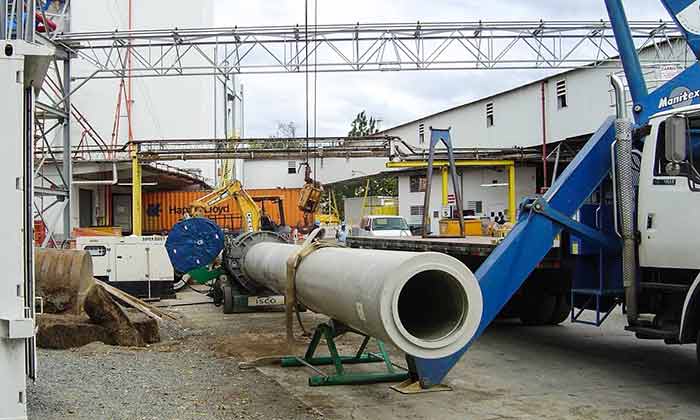
EPA regulation 40 CFR 280 requires that secondary containment must be able to hold leaking media for a minimum of 30 days. Drainage or suction systems can be monitored manually while pressurized systems require automated monitoring so the flow of the media can be restricted to avoid potential ground water contamination. Aside from the EPA regulating and enforcing 40 CFR for below-ground installations, many corporations have internal safety and environmental policies stipulating double-containment systems for underground and overhead piping systems. The Occupational Safety and Health Administration (OSHA) does not have a specific double-containment regulation for above-ground piping systems. The OSHA occupational chemical database lists hazardous chemicals and their permissible exposure limits (PELs). OSHA recommends isolating or enclosing the process as a way to control exposure of personnel to toxic substances.
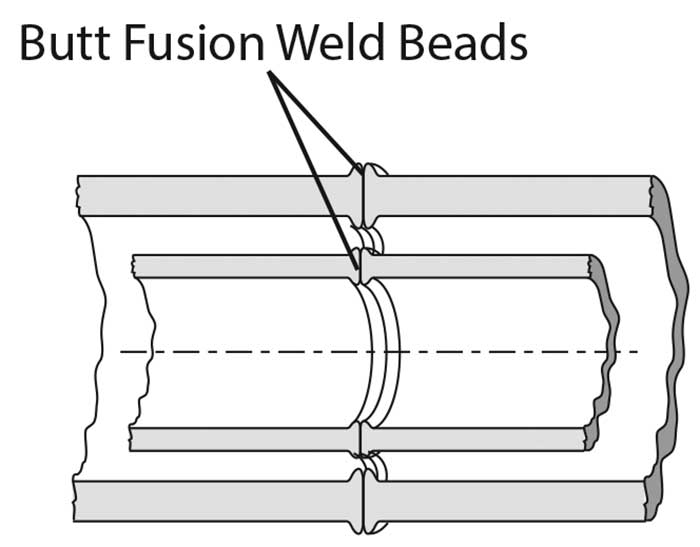
Design Criteria/Operating Parameters
Materials
Reasons why thermoplastics should be considered when designing a piping system include: excellent flow characteristics, corrosion/chemical resistance, energy efficiency, light in weight, fast installation time and long life expectancy. A wide assortment of materials exist that offer long-term performance where there is little or no degradation after 25 years. Little maintenance is required because there are no pitting, scaling or rusting corrosion. Polyvinyl chloride (PVC) and chlorinated polyvinyl chloride (CPVC) solvent-cemented joining systems, polyolefins—including polyethylene (PE) 100-RC, high density polyethylene (HDPE) and polypropylene—and fluoropolymers, such as polyvinylidene fluoride (PVDF), ethylene tetrafluoroethylene (ECTFE) and perfluoroalkoxy (PFA), use a variety of thermal fusion joining methods. These can be assembled using simple hand-held welding tools, hydraulic equipment or automated equipment that verifies proper welding procedures. Fusion joining methods have become more common in process applications due to their mechanical strength, chemical resistance and ease of installation for most field conditions. Pressure testing can be done within minutes of a final weld.
Chemicals & Temperature
All thermoplastic materials are resistant to a variety of organic and inorganic chemicals up to high concentrations with temperature capabilities ranging from cryogenic to 400 degrees F. Chemical resistance and temperature tolerances vary from one plastic to another. Many thermoplastic manufacturers provide chemical resistance guides. Consult the manufacturer for applications where there may be many chemicals or ones that are aggressive.
Pressure
Thermoplastics have varying pressure ratings at different temperatures. Pressure ratings for thermoplastics are reduced at elevated temperatures. Knowing the system’s standard operating pressure, temperature and heat gain from sun exposure is the starting point. Spikes in temperature may reduce the pressure rating. It is necessary to examine other conditions that may affect the operations of the piping, like heat radiating from a roof. If pressure spikes occur, determine for how long and how high.
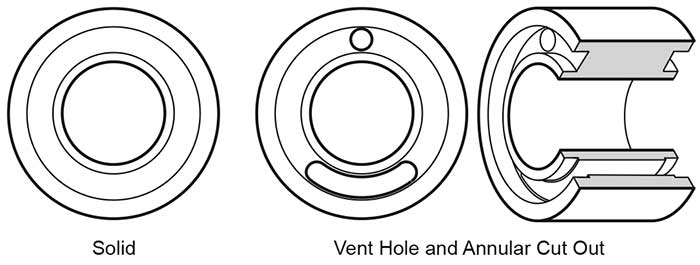
Temperature
The design for a double-containment piping system is similar to single-wall piping design. Chemical, temperature and pressure data are important for the carrier line and the containment secondary line. Temperature plays a key role, affecting the pressure rating of the pipe system and expansion rate. With regards to expansion: it is the rule, not the exception when engineering a piping system using thermoplastic materials. As temperatures rise and fall, thermoplastic materials expand and contract to relieve stress. Stress analysis can be calculated to determine the amount of growth and flexibility the system will require.
Expansion
If the chemical or chemicals entering the pipe system are hot, thermal expansion of the carrier pipe will occur. It can also occur when a mixture of chemicals creates an exothermic reaction. The methods used to handle expansion in double-containment piping systems are similar to those used in single-wall piping systems. A flexible design system uses a fitting that anchors both the carrier and containment pipe and allows the carrier pipe to move inside the containment line. Containment areas generally may need to be expanded in order to address the thermal expansion and contraction of the carrier pipe.
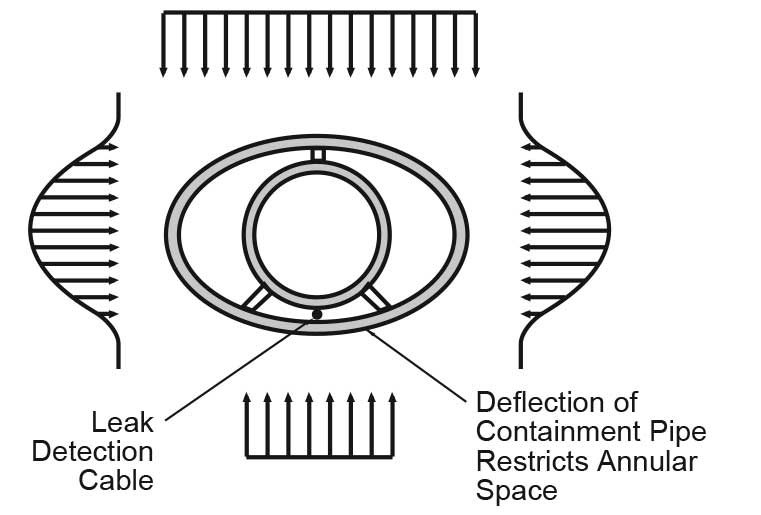
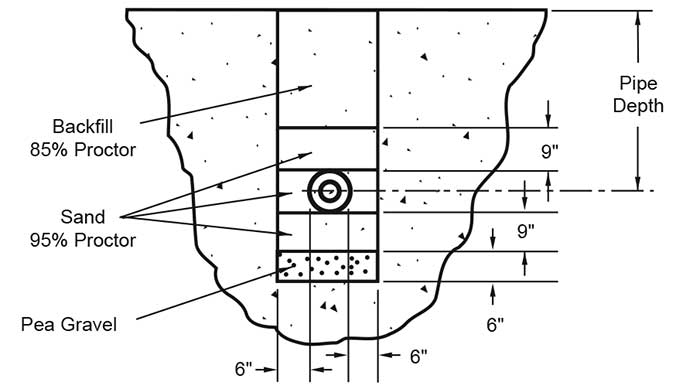
For restraint design, proper use of restraint fittings (what some call a dogbone) and guides throughout the system will isolate the fittings from thermal stress and end loads when temperatures fluctuate.
Burial
When burying thermoplastic pipe, both static loads (weight of the column of soil on top of the piping) and live loads (traffic) need to be taken into account. With static loads, the deeper the burial, the higher the load on the pipe. Live loads, on the other hand, have a greater effect on pipe at shallower depths. Other factors to consider when burying thermoplastic pipe are the type of soil, compaction of the soil and the design of the trench. The material PE 100-RC has mechanical properties that do not require special soil backfill or compaction methods. Double-containment burial calculations are always based on the outer wall of thermoplastic pipe. If leak detection cable is to be installed in the interstitial space, deflection of the material has to be calculated.
Installation
Installation costs can be cut considerably by using fusion welding. Fusion-welded systems can reduce labor by over 50 percent. The butt fusion welding method for thermoplastic pipe fuses the inner and outer pipe simultaneously (if both are the same material), essentially creating one weld. Most double-containment systems—whether metal, thermoset or thermoplastic—are stepped up a minimum of two sizes from the inner pipe to create an interstitial space between the two pipes.
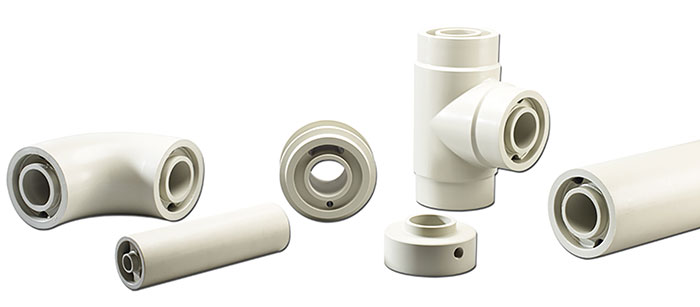
Some double-containment systems are co-extruded, meaning the carrier and containment pipe are extruded at the same time. This saves material and labor costs, since centralizers do not have to be inserted and welded to center the carrier pipe in the containment pipe when cut. The containment pipe steps up one size versus two sizes for fabricated systems. For example, a 1-inch by 3-inch fabricated double-containment pipe system versus a co-extruded one inch by one and a half inch system. Less space is required for the piping.
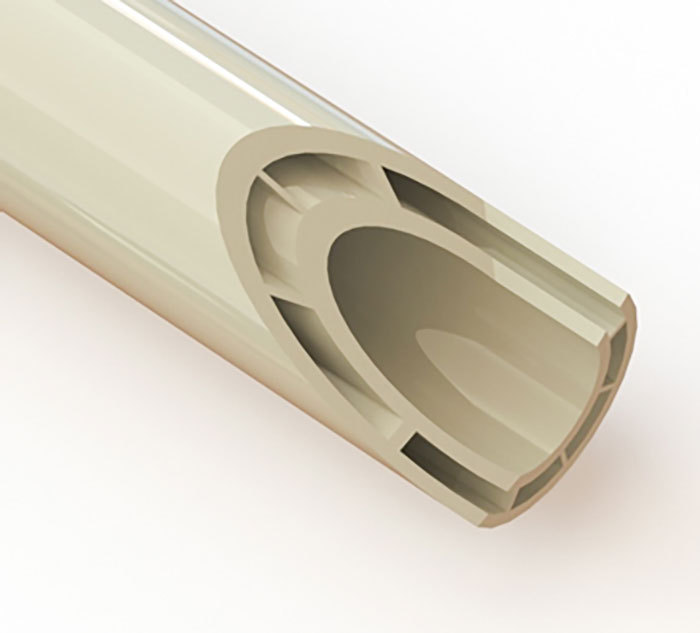
The most common underground process waste systems are drain, waste and vent. A common way to reduce costs is to use a thinner wall pipe for the containment. Heavier wall materials are generally used for the carrier line since the process chemical or process waste is flowing daily. For example, most manufacturers with standard dimension ratio (SDR) ratings produce polyolefin and fluoropolymer piping. An For chemical systems an SDR11 by SDR32.5 polypropylene pipe would have a pressure rating of 150 pounds per square inch (psi) for the carrier pipe and 45 psi for the containment pipe. PE 100-RC SDR11 by SDR17 would be 150 psi carrier and 90 psi containment, which maintains chemical compatibility and reduces cost when compared to an SDR11 by SDR11 containment system.
When using the same material for the containment pipe is too expensive compared to the carrier pipe because of size, using dissimilar materials is another option that can lower costs. This can be justified because the containment pipe does not handle the media on a continuous basis, and the EPA requires that the containment pipe be able to hold for a minimum of 30 days. Keep in mind that labor goes up when dissimilar materials are used because the number of joint connections is double and having to use different joining techniques is possible. Typical examples of this are a stainless carrier inside glued fiberglass reinforced plastic (FRP) containment or fusion-welded PVDF inside solvent-cemented CPVC a polyolefin like PP or PE.
During material selection, consider the time the liquid must be retained in the containment pipe. In the event of a leak, how long will it be before a repair can be made? Is it a process line that cannot be shut down for a long period of time due to production? It is important that the containment pipe has the capability to hold the media until such time that the repair can be made.
Leak Detection
Automated leak detection options such as cable or low-point sensors set off an alarm to alert plant personnel. Cable leak detection systems must have minimum clearance of 3/4 inch in the annular space between the carrier and containment pipes. That means a fabricated double-containment system must be used because co-extruded pipe has annular space less than 3/4 inch and continuous ribs the length of the pipe. Pulsed cable-radar technology has the capability of locating a leak with ±.3 percent of the sensor string or ± 6 feet. Consult the double-containment supplier for recommendations specific to the project.
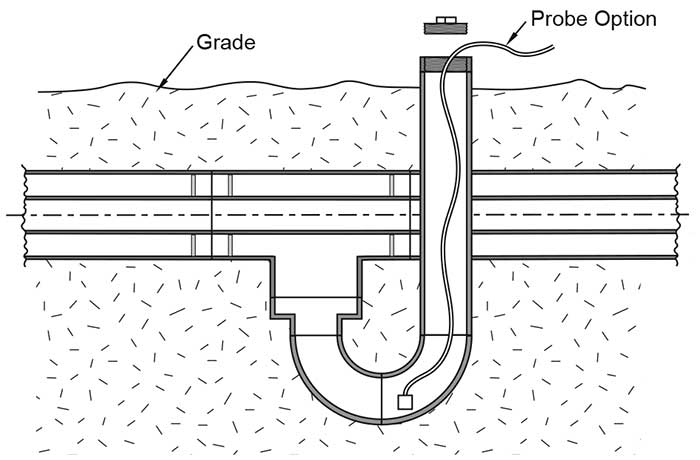
Low-point sensors are another automated option for drainage or pressure systems. They pinpoint an area or zone that has developed a leak. Zones are compartmentalized in order to keep liquid trapped so as not to affect another zone and tripping another senor. Compartmentalizing the system minimizes the area to which the leak can spread. Low-point stations containing leak detection probes can also be used manually for drainage systems. Other manual options are manways or sumps where the media would collect or sight glasses with valve for above-ground installations for visual inspection.
Additional Components
End terminations are needed where the double-containment is closed off in order to transition to single-wall pipe. Additional centralizers or (support discs) are required when pipe is cut in the field. Floor drains and cleanouts may be required are available for drainage systems. Many systems use double-containment valves to isolate the process or shut down in an emergency. If double-containment valves will be used, ensure there is sufficient access to the valves to enable the replacement of seats and seals over time. Some double-containment valve components may require the whole unit to be cut out of line in the event of valve failure, which is an expensive proposition.
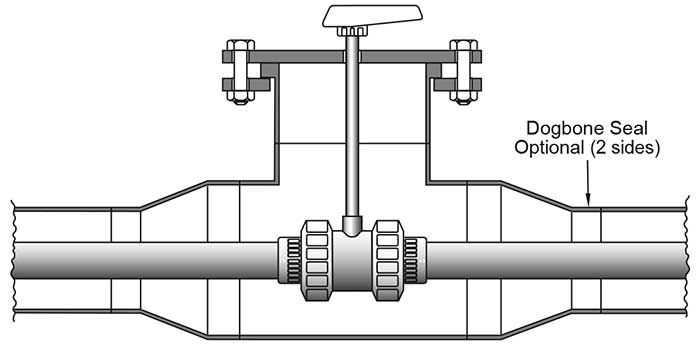
Training
Whether PVC, FRP, stainless steel, HDPE or another material, it is strongly recommended that the manufacturer trains the installer on any required equipment and proper installation. The owner, engineering firm, manufacturer and contractor all want the system to perform at maximum efficiency. Proper training reduces the potential for pipe failure and its environmental impact.
When investigating double-containment piping system options, locate manufacturers that provide extensive engineering data (engineering design guides). Verify that the manufacturer has an engineering staff that can provide specific recommendations and guidance. Field personnel that can conduct installation training can help ensure a successful project.