Getting the most out of a mechanical seal is directly proportional to the quality of the environment in which it operates. In nearly every application, the key to mechanical seal longevity and extended mean time between failure (MTBF) is understanding the needs of the mechanical seal and how it should be supported. Although every application is unique in its mechanical sealing requirements, vertical pump applications present a specific set of challenges. When determining the best piping plan(s) to support a mechanical seal, it is important to first understand how different types of pumps may affect the seal chamber pressure. For example, the seal chamber pressure on a vertical overhung pump (OH3) is going to depend on specific impeller features. Whereas for a vertical sump pump (VS5), because the discharge piping is run outside of the shaft column, the seal chamber pressure will be very close to atmospheric pressure. This article focuses on three unique pump categories: vertical turbine and wet pit pumps, vertical sump and slurry pumps and vertical overhung pumps.
Vertical Turbine & Wet Pit Pumps (VS1, VS2, VS3, VS6 & VS7)
The mechanical seal in a vertical turbine or wet pit pump is located in the shaft column above the mounting plate of the pump. Process fluid is brought up through the shaft column and exits the pump from the discharge nozzle. Because of this, the seal chamber pressure will be equivalent to the discharge pressure of the pump. The mechanical seal will need to be properly vented to prevent vapor lock, so the flush port should be as high as possible axially (above the seal faces). The most common piping plan selected for these kinds of pumps is an American Petroleum Institute (API) Plan 13, which needs to be sized to provide adequate flush flow over the seal faces to keep them cool and lubricated. The primary advantage of API Plan 13 in this arrangement is that it allows for continuous venting of the process fluid to avoid accumulating vapor in the seal chamber and vapor-locking the seal. The axial positions of the flush ports become important when operating a vertical mechanical seal. To promote the best possible venting scenario, the flush-out (FO) ports should be located as far outboard as possible, above the seal faces. In contrast, for any vertically oriented seal, the flush-in (FI) ports should be below the FO ports. If possible, flush porting in the mechanical seal should be tangential to promote ease of flow throughout the seal. API Plan 13 can be used to remove solids from the seal chamber as well. If there are solids in the process fluid, it is advised to use API Plan 13 in conjunction with a bleed bushing (usually supplied by the pump manufacturer) and include API Plan 32 for proper seal chamber flushing.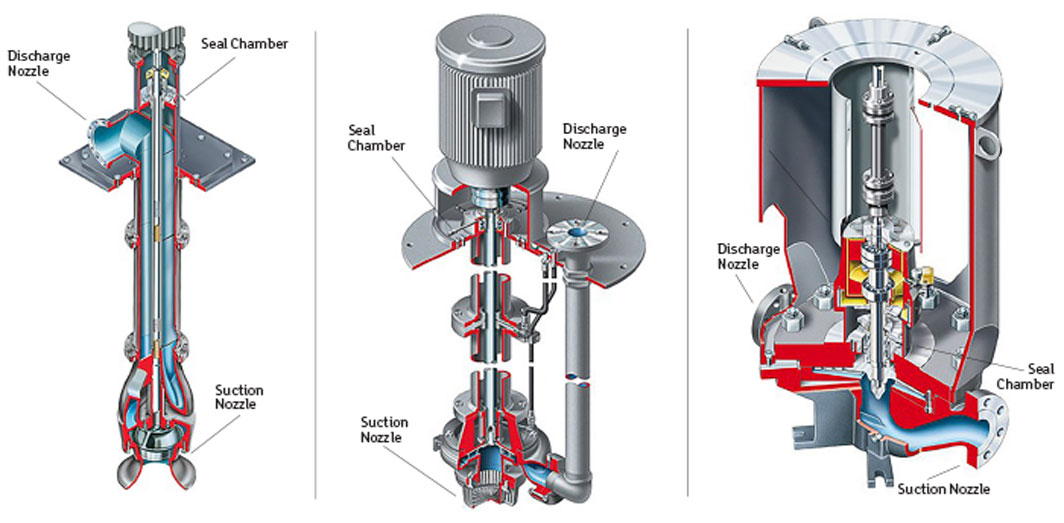