How do end users choose, and what are each type’s ideal applications?
08/25/2014
Motor manufacturers routinely answer questions about the differences between submersible and immersible motors and the applications best served by each design. While end users ultimately decide which motor best fits their need, this article explains how the designs differ and provides information that will help end users make informed decisions.
Submersible Motors
Municipal and industrial wastewater markets use submersible motors for both wet and dry pit applications. These are totally enclosed, non-ventilated (TENV) motors. Wet pit motors use the effluent for cooling and are designed to run continuously while submerged. These standard designs are also rated to run in air for 15 minutes when conditions require it. These motors can also be designed for continuous operation in dry pit applications by de-rating a larger horsepower motor frame. This allows the motor to dissipate heat while running continuously in a dry pit application that only experiences flooding under unusual conditions, such as heavy rains or a backup in the system.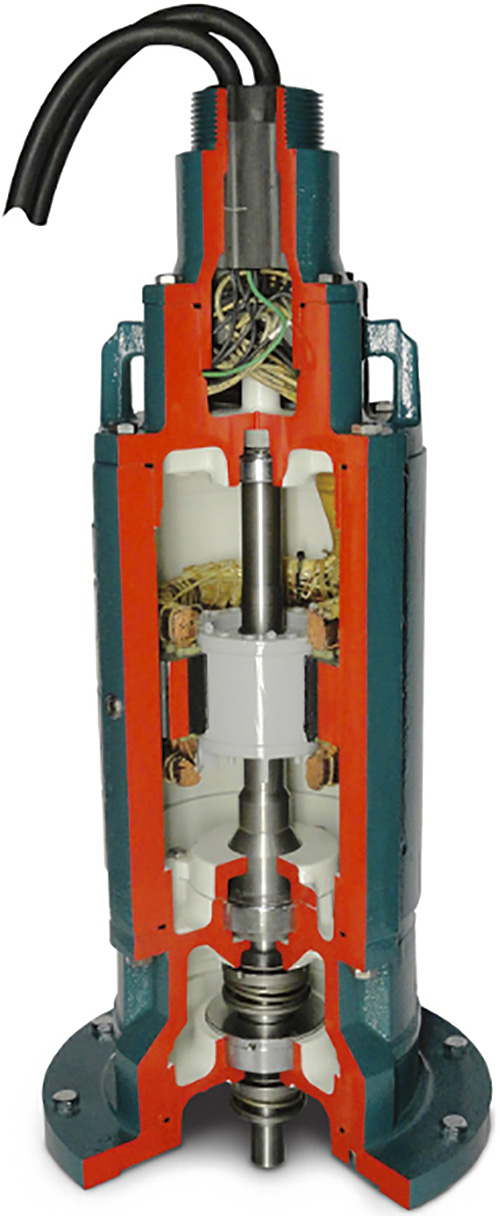
Immersible Motors
Immersible motors, on the other hand, are specifically designed to be operated in a dry environment that might flood under unusual circumstances. One company’s immersible design was developed for an end user who needed a more cost effective alternative to the more expensive, oversized submersible frame motors used for continuous in air operation. Immersible designs use TENV enclosures in smaller frames and totally enclosed blower cooled (TEBC) enclosures on larger frames. They have a sealing system that allows reliable operation for two weeks while submerged under a maximum depth of 30 feet of water. The immersible design has been proven with extensive tests, including disassembly and inspection to ensure dryness and structural integrity. The TEBC design runs continuously in air and has a separate 1/2 horsepower motor running an external fan for constant velocity cooling. An end user-supplied float switch turns off the blower motor if the water reaches a level near the cooling fan. The opposite drive end is totally enclosed, and the fan and blower motor are mounted separately to ensure that moisture will not enter the motor from the opposite drive end. These motors are also built with precision machined cast iron frames and endplates with grooves and O-rings to prevent water ingress to the motor.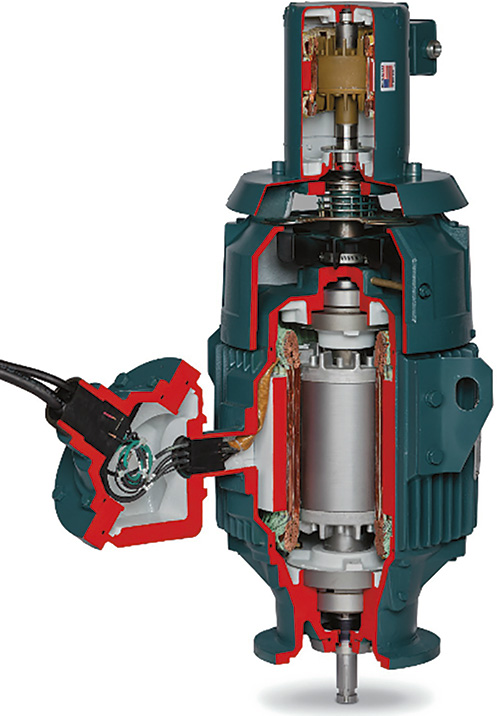