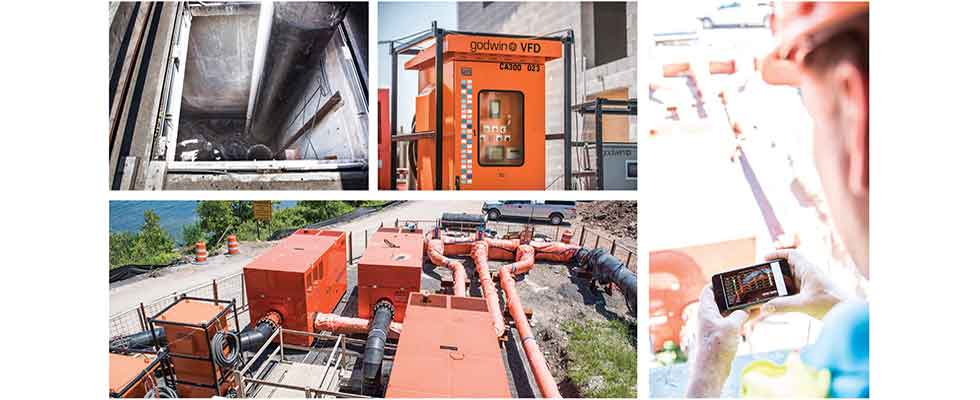
For decades, the standard in temporary bypass pumping has been diesel-powered portable pumps. Their flexibility and ability to be set up anywhere has made them a go-to choice. But with fluctuating fuel prices and rising service costs, along with growing interest in cleaner and greener sources of power, electric-driven pumps offer a practical alternative, especially for longer-term projects.
Several elements go into the contract selection process, but most decision-makers focus on the overall pump rental cost, rather than looking at the cost of pump rental plus anticipated operating costs. The latter approach provides a more comprehensive picture of total cost considerations, allowing for more accurate budgeting. It can also help avoid unanticipated operating cost overruns throughout the duration of the project.
Using this method is somewhat of a paradigm shift for the industry, but one that can have long-term benefits. While one option may be more cost competitive from a rental standpoint, calculating and including estimated operational costs as part of the bid process provides a more accurate view of total rental costs.
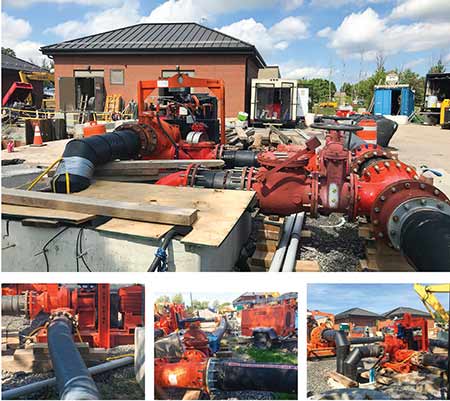
In some circumstances, electric-driven pumps may not be a cost-competitive alternative to diesel-powered pumps. Two factors to take into consideration are existing access to power and/or the cost of any necessary electrical drop as well as the anticipated rental length. On average, a project lasting under three months is not likely to provide enough savings when compared to a diesel bypass pump to offset the cost of an electrical drop.
In most cases, the rental cost differential between diesel- and electric-driven portable pumps is negligible. With that knowledge, calculating the operating costs of a temporary application can determine if the project is a good candidate for electric-driven pumps. This requires specific analysis and information.
Understand Operating Conditions
To accurately estimate operating costs for the project, what is first needed is a thorough understanding of the proposed operating conditions, specifically the duty point of the application. This is also known as the required flow and head. This data can help determine the operating costs for a proposed application by calculating the horsepower a pump needs to achieve the duty point.
Next, calculate the operating costs of using an electric- or diesel-powered pump. For example, an 8-inch portable pump on a sewer bypass application will be operating at 1,500 gallons per minute (gpm) and pumping against 80 feet of total dynamic head (TDH). This application uses a specific gravity of 1 as water is being pumped. A constant conversion factor of 3,960 is used in the calculation. Using this calculation on the performance curve for this pump, that would mean an efficiency of about 61%. Upon completion of the calculation, the impeller would need approximately 50 horsepower (hp) of torque from the drive source.
Converting Needs to Operating Costs
Once the operating conditions are known, the next step is to determine fuel consumption. Establishing fuel consumption makes it easy to estimate probable operating costs for both a diesel- and electric-driven pump in the application. Using the same example from above, Equation 1 is used to calculate diesel fuel consumption.
It is important to note this figure does not include service costs. Industry standards recommend service for every 250 hours of run time. For longer-term projects, this can add substantially to the operating costs. Returning to the same example, Equation 2 is used to calculate equivalent operating costs for an electric-drive pump.
As with the diesel pump calculation, this amount does not include an important cost consideration: getting electric power to the pump, also known as the drop cost. Though projected operating costs of electricity will always be less than diesel fuel, the drop cost can negate that cost advantage. Depending on the nearest power source and where the pump will be located, the cost can be significant. That amount also needs to be calculated and included in the operating costs.
One advantage electric-driven pumps offer over diesel pumps is that they also reduce the overall carbon footprint of a project, which may be a factor in the bid process. Depending on the project design, some electric pumps can provide the capacity that formerly required multiple diesel-powered pumps.
Determining Operating Costs
Returning to the above example, in this application, the pump is likely to run 12 hours a day and the cost of running electricity to the pump is $5,000/month. Knowing these factors, it is then possible to obtain an accurate comparison between the two options.
In this scenario, and even with standard diesel servicing costs factored in, the operating costs for diesel- versus electric-driven pumps are less at the two-month period. But as the duration of this application continues over time, the cost advantage begins to diminish, and the electric-driven option becomes more cost effective, even with the drop cost.
Again, it is important to note that rental cost differentials between diesel- and electric-powered pumps are negligible, further emphasizing the importance of calculating operating costs for the duration of the project.
A combination of electric and diesel pumps on-site is another option that can be considered. Often, an electric-driven model is chosen as the primary pump as it is used most during the project, and a diesel-powered pump is designated as a backup
to provide the needed redundancy for sewerage pumping. A project could be engineered this way for many reasons, and the cost savings of integrating electric pumps becomes an additional advantage.
It is vital to work with a trusted rental company that specializes in pump equipment rental. Doing the work upfront to calculate total rental and operational costs also provides a clear projection for budgeting purposes and minimizes unexpected operating cost overruns at the close of the project.