Responsible for supplying an average of 60 million gallons of drinking water each day, the Monroe County Water Authority (MCWA) in Rochester, N.Y., depends on more than 100 centrifugal pumps with a total installed capacity of more than 35,000-hp. These pumps range in size from 5-hp to 1750-hp and consume an average 5-MW of power daily. In an era of conserving energy and increasing sustainability, the MCWA is attempting to reduce energy consumption, greenhouse gases and operations and maintenance costs. Through computerized modeling of its water distribution system, the MCWA discovered many discrepancies in their pumps between the original manufacturer pump curve and the actual field pump curve. When inputting the pump curves into the model, they discovered that the model could not be calibrated using original manufacturer pump curve data. The MCWA staff went into the field and physically measured each pump's performance (head, flow, kW and RPM) to develop a set of field pump curves for the water distribution model. They found that in virtually every pump tested, actual field pump curves were significantly below the manufacturers specified pump curve and field measured pump efficiencies were often 20 percent or more below the original manufacturer's stated pump efficiencies.
Pilot Study
The MCWA team began a pilot study to refurbish several interior casings of the mechanically rebuilt pumps to see if reducing interior pump roughness would have any positive impact on pump performance and efficiency. Since only sandblasting the interior pump casings would allow corrosion and tuberculation to return quickly, the team began looking for acceptable coatings that could be applied after sandblasting to protect the interior surface from future corrosion and perhaps even enhance the reduction of head loss/hydraulic drag through the pump. Due to their availability, ease of application and relative low cost, the MCWA team focused their coating search on NSF-approved brushable type ceramic-filled epoxy coatings. While the manufacturing and chemical industries have long embraced ceramic-filled epoxy coatings for abrasion and corrosion resistance in pumps, the MCWA team found little research to support that coatings improve or stabilize pump performance and energy efficiency. Although the MCWA team was skeptical on how much performance and efficiency could be gained, they decided to sandblast and coat three of the mechanically rebuilt pumps as a pilot study test case. Once this was completed and the pumps were reassembled, MCWA conducted field pump performance tests to measure the coating's impact on pump performance and efficiency..jpg)
NYSERDA Study
Structure of Study
The ongoing study involves 18 of MCWA's centrifugal pumps. Six sets of three identical pumps were tested against each other. In every case, each pump was first either mechanically refurbished or sandblasted and coated. Next, the pumps were reassembled and field performance tested. The pumps were then disassembled a second time and either sandblasted/coated (if the first step was mechanical refurbishment) or mechanically refurbished (if the first step was sandblasting/coating) to measure the performance enhancement from the second step of the process. This step allowed the performance-enhancing benefits of mechanical refurbishment and sandblasting/coating to be measured independently. The team could determine the individual contribution of each step to increased pump performance and efficiency and if it made any difference as to the work sequence performed. Additionally, it was decided that three pumps would be sandblasted and left uncoated to develop a timeline showing how fast the corrosion and tuberculation would return to the point where pump performance began to decline. The pumps' performance would be field tested and studied for any performance degradation at 30, 60 and 90 days, then again at 6 months and every 6 months for 5 years thereafter. As with the pilot study, the MCWA team decided to use NSF-approved brushable type ceramic epoxy coatings in the NYSERDA study. These coatings tout abrasion, corrosion, cavitation and even chemical resistance. The MCWA was also interested in coatings that were easy to apply, could be done in house at reasonable cost and would provide a smooth finish to reduce friction. Using brushable ceramic epoxy products, They quickly began rebuilding the first set of pumps.Rebuilding the First Set
As is often the case, dismantling the pumps proved to be the toughest work, including overcoming seized and/or rusted bolts and other typical maintenance challenges. As with the pilot case, the mechanical refurbishment consisted of replacing wear rings, bearings, shaft sleeves and impeller inspection and replacement if necessary. Pump casings were sent out for sandblasting, and as soon as a pump casing was picked up and returned to the shop, the coating process began (generally within 4 hours after completion of sandblasting). The MCWA team started by filling in any deep pitted areas or gouges with a metal-filled epoxy and allowed that to cure before applying two 15-mil thick coats of brushable ceramic. Although inexperienced with these epoxy products, the team found them generally easy to apply, although it was initially difficult to be neat on the larger pumps. In addition to using short nap brushes and rollers designed for epoxy application, they also found inexpensive items such as household scrub brushes attached to broom handles ideal tools to reach into and apply the coating to the interior of the larger pumps, especially large double volute pumps.Results
After the first set of pumps were mechanically refurbished, sandblasted, coated and returned to service, the performance was measured, and the results surprised the team again. The data showed that compared to an OEM's specified pump curve, traditional mechanical refurbishment alone recovered only about half of a pump's total lost performance and efficiency. MCWA found that to fully return each pump to (or close to and in some cases in excess of) the original manufacturer specified pump curve required the additional step of sandblasting and coating the interior pump casings. Energy analyses also revealed that mechanical refurbishment alone could only achieve about half of the total potential energy savings of a pump compared to what could be achieved if the pump was sandblasted and coated in addition to being mechanically refurbished. This is illustrated by the results for MCWA's Beahan No. 2 unit (see Figure 3)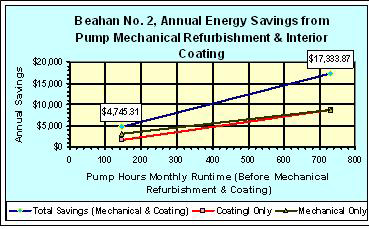