These pumps prevent equipment from corroding, provide lower costs and increase efficiency.
08/19/2015
Engineered composites can be designed and used to improve performance and efficiency as well as reduce maintenance and repair costs. Composite upgrades prevent expensive products from deteriorating, extend the life and reliability of existing equipment, and increase pump efficiency. They can even prevent pump leaks that can result in costly cleanups and fines from regulatory agencies. In most cases, reduced downtime resulting from introducing structural composite pump upgrades is one of the most important benefits.
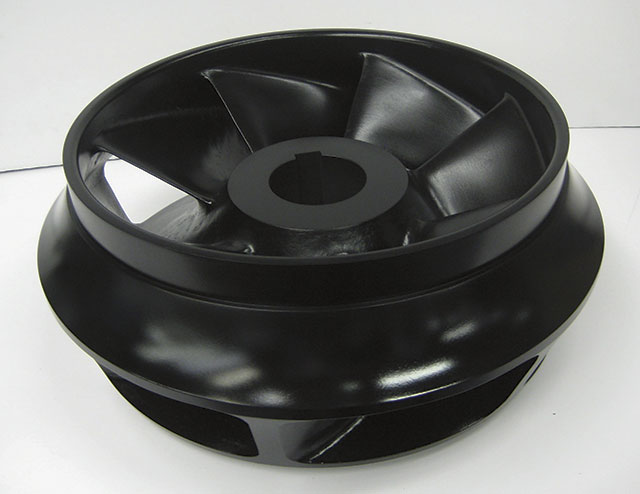
Pump Optimization
Too often, a pump is purchased for a specific performance but when put into service, it operates at a point completely different from the original design point, or BEP, because of the system requirements. The pump operating away from the BEP also causes problems such as excessive noise and vibration, shaft oscillation, cavitation, and premature wear and failure of the mechanical seals, bearings, rings, sleeves and impellers. In extreme cases, the pump shaft will break right behind the impeller from the excessive radial forces that occur when a pump is operated away from the original design point.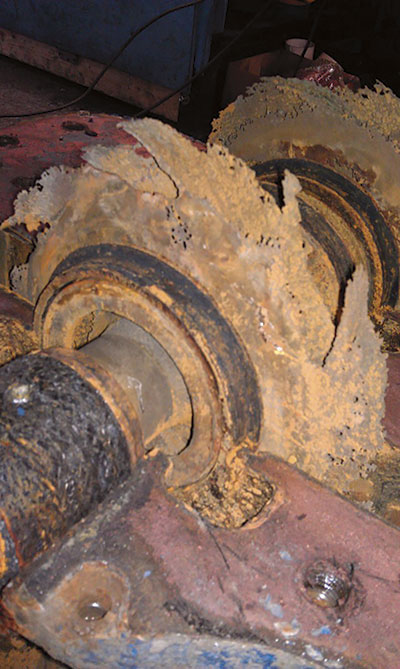
Improved Efficiency
In 2015, tremendous effort has been put forth to reduce energy consumption. The Department of Energy (DOE) and the Hydraulic Institute have been working together to reduce the energy consumption of pumps, motors and pump systems. Engineered composites can contribute to this effort. By re-engineering the pump/impeller design, they can significantly reduce energy consumption—in some cases by 20 percent.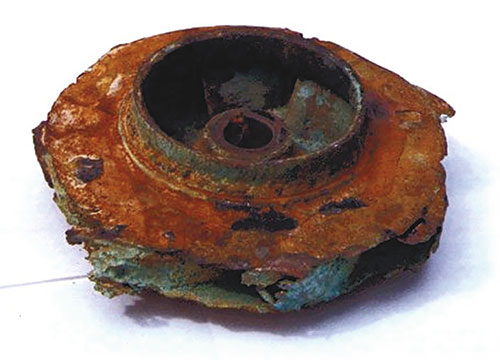
Equipment Longevity
In addition to improved efficiency, engineered composite impellers offer many advantages over traditional products cast from metal. They do not corrode, are lightweight, can run with tighter clearances, are designed for high efficiency, and are not subject to casting defects or imperfections. Many of these impellers and casing rings have been used successfully since 1955 in the Marine, Navy, wastewater, industrial and chemical markets. Structural composite impellers have often outlasted and outperformed products manufactured from bronze, stainless steel, duplex steel, monel and even titanium.Reduced Wear
The new alternative composite solutions for impellers and rings are ideal for new, repair or retrofit applications. Engineered impellers and rings are lightweight and do not corrode.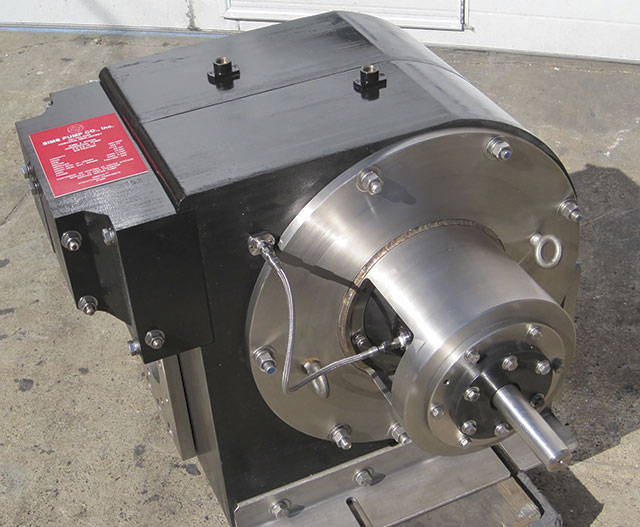
Maximized Performance
Because of new technologies, structural composite impellers are computer-engineered and precision-machined. The impeller vane geometry can be engineered using computational fluid dynamics (CFD) techniques and programmed to maximize efficiency and performance. Problems such as recirculation, radial thrust and cavitation can be minimized or eliminated by using structural composite impellers instead of the traditional metallic ones. Impeller vane shapes can easily be modified to provide the best vane shape for specific applications and performance requests.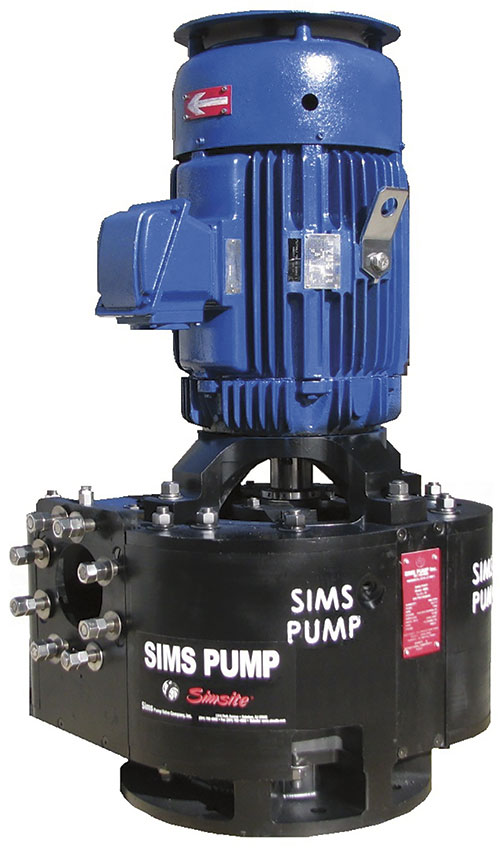