07/25/2014
Cost estimation errors are common in a variety of projects. Recent studies have shown the cost of machinery can represent 20 to 35 percent of a processing and manufacturing project’s total cost. The estimated costs for new plants and particularly new pump installations are very uncertain and have increased in recent years. The following concepts minimize the cost of pump installations:
- Maximizing the extent of manufacturing and installation in the shop environment
- Simplifying a pump package’s transportation and installation
- Providing modularized components that are easy to change
- Reducing on-site personnel supports and encouraging unmanned operation
- Eliminating as many standby pumps as possible
Pump Installation Cost Estimate
Historical data could inform pump installation cost estimation models within certain limits. Results have shown a large cost difference between different regions. The economies of concentration play an important role in cost. Cost studies have indicated that pump installation cost components usually have economies that are to scale to pump unit capacity and pump train size. The cost estimation of a pump unit or installation in a plant cannot be fully accurate, with the exception of the material cost, particularly the cost of a pump package. This cost can be estimated from the pump package’s vendor, and the cost of materials could be obtained from suppliers. However, other cost estimations are relatively inaccurate. Labor costs have much larger cost overruns compared to other cost components. The following estimation concept can be employed for a pump unit or installation: (Pump Unit Cost) = A × (Pump Package Cost) + B The factor A is assigned for all auxiliaries and accessories required for each pump package such as the foundation, civil works, piping and additional steel structures for each pump package. This factor is usually between 1.3 and 2.5. The pump package cost includes all skid-mounted facilities such as the driver and lubrication oil system. The factor B is assigned for all auxiliaries and accessories required for each pump unit, such as unit piping, unit utilities, protection systems, unit pit/drain, unit electrical facilities, safety equipment, unit steel structures and unit civil works. Because the cost underestimating error is generally larger than the overestimating error, proper safety margins for factors A and B are always encouraged. The cost is also a function of the project size or the pump system capacity. A proper set of factors should be developed for a defined range of the pump unit size and capacity for a region. Environmental conditions—soil, terrain, cost of living, population density, economies of scale, noise limits, applicable codes and distances from pump supplies—could affect the installation cost estimation and should be considered when the cost factors are estimated.Other Costs
Studies on recent pump installations have shown that the cost of civil works (site developments, foundations and others) are about 9 to 20 percent of the total cost. They have also shown that the cost of installation can be approximately 7 to 11 percent of the total cost. The required man-hours for the installation and commissioning of pumps can vary significantly. For packaged pumps, the following indications should be noted:- For large pump packages (more than 1 megawatt (MW)), the installation and commiss-ioning man-hours could be between 300 and 900 hours.
- For small pump packages (less than 1 MW), the installation and commissioning man-hours could be between 100 and 300 hours.
Case Study
The first case study is presented for a 6 MW pumping unit. The costs of electric motor-driven pump packages are obtained in millions of U.S. dollars (MUSD):- A 3 MW pump package: 0.9 MUSD
- A 1.5 MW pump package: 0.6 MUSD
- A 0.8 MW pump package: 0.45 MUSD
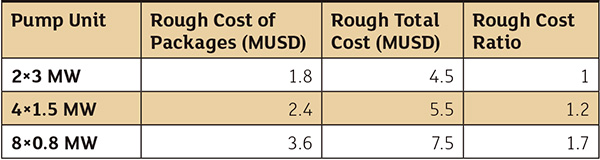
- Option 1: A 320 kW pump, $52,000
- Option 2: A 200 kW pump, $42,000
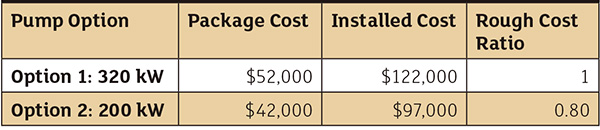