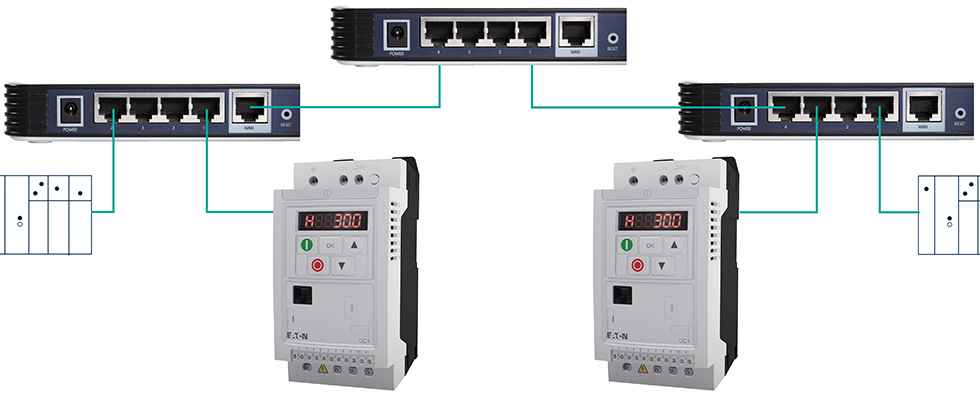
Over the past 30 to 40 years, industrial controls have evolved from panels full of control relays to sophisticated programmable logic controllers (PLCs). Other types of specialty controllers such as distributed control system (DCS) controllers for the process control industry have also evolved as industrial controls became more automated.
But, it was the advent of the PLC that drove the need for industrial networks. The first PLC arrived on the scene before the personal computer existed, requiring other means for programming them, such as terminals.
This limited the number of instructions and reduced the early PLCs to “relay replacers.” The only instructions early PLCs supported were contacts and coils, which are similar to relay logic.
As the demand for more sophisticated controls became apparent and when the personal computer became available, PLCs evolved as more powerful industrial controllers.
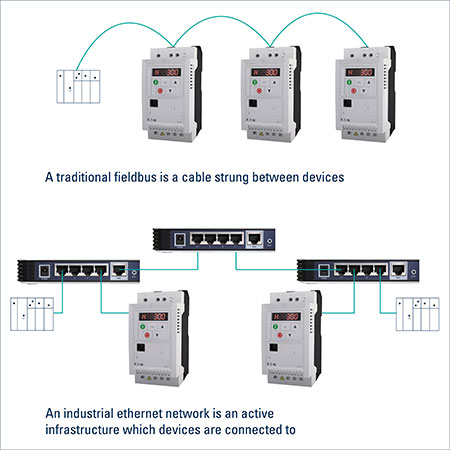
The Need for Industrial Networks
Industrial networks were the result of the rise and acceptance of PLCs as the controller of choice for most industrial applications. As PLCs and their applications grew, the following demands for industrial networks followed:
- Upload and download programs from a personal computer running PLC programming software.
- Monitor the execution of a program while “online” with the PLC.
- Communicate from a PLC to distributed input and output (I/O) modules.
- Communicate between PLCs to exchange critical control data.
Other uses for industrial networks have also evolved as industrial applications and other products became more sophisticated. Motor protection in the form of overload relays advanced from electromechanical devices to solid-state devices offering better motor protection as well as the ability to communicate on industrial networks. Soft starters and variable frequency drives (VFDs) were invented to provide additional control features for motor applications. These devices also provided connectivity to industrial networks.
Today, industrial networks have evolved to the point where all types of motor control and protection devices are controlled and monitored by PLCs using industrial networks. Distributed I/O modules are also connected to these same networks as are human machine interface (HMI) devices.
PLC Programming Software
PLC programming software became powerful, allowing PLCs to support more powerful functions. Because PLCs and programming software were becoming more powerful, faster industrial networks were needed to upload and download the programs, monitor and control distributed I/O and monitor execution in “real time.”
Distributed I/O
Distributed I/O was a concept that came out of the early years of the PLC. Once some of the early industrial networks had emerged, the value of distributing I/O modules that would communicate data to and from a PLC became apparent. Rather than running wires long distances throughout a facility back to a central PLC panel, distributed I/O allowed a single communication cable to be run to distributed I/O modules. These I/O modules were then wired to devices such as solenoids, push button, pilot lights, limit, proximity and photo switches that were in proximity to these I/O modules. This saved on the cost of wire and the labor of running bundles of wires long distances and reduced the impacts of electrical noise.
Faster and faster industrial networks were needed for distributed I/O to keep up with high speed, automated production of various products and processes.
Industrial Network Reliability
The primary reason for the acceptance of industrial networks in industrial applications is reliability. For example, the early industrial networks basically sent data from one PLC to another and hoped it got there without being corrupted. There are many electrical noise sources in industrial facilities such as starting and stopping large motors and switching power supplies. This electrical energy can change data being transmitted over communication networks. This was unacceptable in industrial applications. Especially when controlling critical I/O.
Shortly after industrial networks became available, something called error checking and retries were added to them.
Error checking and retries ensured that critical control data was not used unless it was deemed intact. This allowed for the acceptance of industrial networks in most industrial facilities. The actual process of error checking has become much more sophisticated through the years, but the basic principle still holds. The data transmitted must only be used once it has been verified as not having been corrupted.
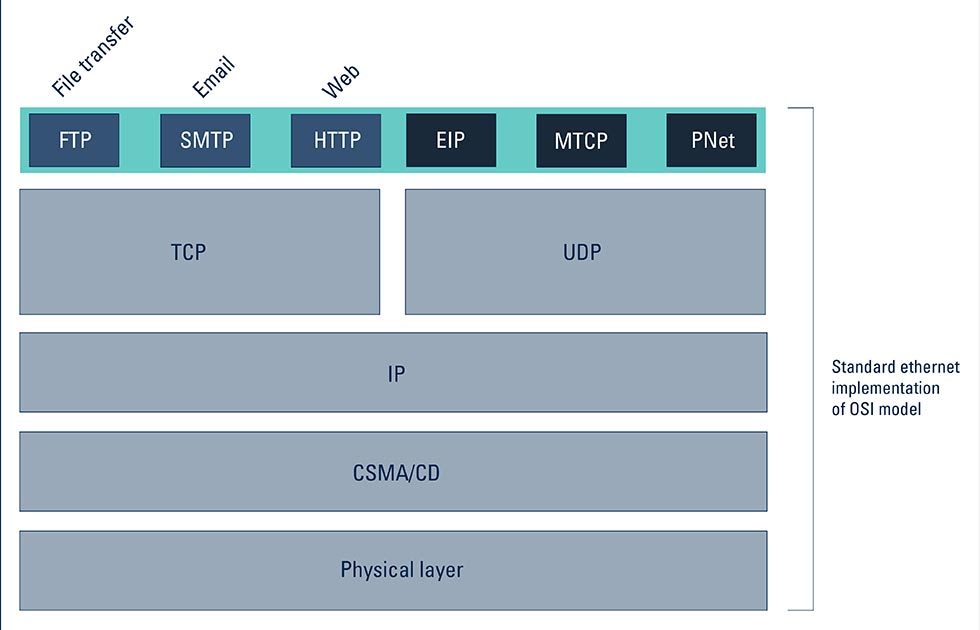
Proprietary to “Open” Industrial Networks
Up until the early 1990s, industrial networks were proprietary and owned by the various PLC manufacturers. Royalties had to be paid to the owners of these networks to obtain the specification to develop products for these networks.
Mainly due to a push by large manufacturing customers of these PLC vendors to “open” industrial networks, new networks administered by third-party organizations were created. These networks were the following RS-485 based fieldbus networks:
- DeviceNet, administered by odva.org
- PROFIBUS, administered by profibus.com
- Modbus serial, administered by modbus.org
These were the major networks that were turned over to newly formed independent trade organizations. Any company could purchase the specification for these network protocols and develop products for them. Conformance testing was also provided by these organizations to ensure each product operated according to the specification. But, no royalties needed to be paid and no company could be turned down.
This opened the door for any company to develop products on these open networks. This is what the large end users wanted. They wanted the ability to purchase the products they needed from the manufacturers of their choice and know these products will operate properly on the network.
Industrial Networks Today
These initial open networks are still around today, but they have also evolved into their Ethernet transmission control protocol/internet protocol (TCP/IP) versions.
- EtherNet/IP evolved from DeviceNet
- PROFINET evolved from PROFIBUS
- Modbus TCP evolved from Modbus serial
These Ethernet-based networks include others such as EtherCAT. Ethernet-based networks have evolved through the years with the advancements of commercial Ethernet. They began as 10-baseT (10 megabits per second [mbps]) networks and have moved to 100-baseT (100 mbps) then to 1 gigabits per second (gbps) networks in some cases. The industrial Ethernet networks tend to lag the commercial Ethernet networks found in the office environment because industries tend to be more conservative.
Other advances in industrial Ethernet networks are in the form of full duplex Ethernet using full duplex managed industrial Ethernet switches to eliminate collisions and increase throughput and determinism.
The Future of Industrial Networks
It is always difficult to predict the future of technology with the incredible technical advancements that are constantly occurring. But, it seems that Ethernet-based industrial networks are here to stay for the foreseeable future. Additional advanced features will and are being added. Some examples are: faster throughput, better determinism, real-time control, cybersecurity, wireless options and safety protocol options
Industrial Ethernet-based networks can follow the technological advancements of commercial Ethernet TCP/IP. This also ensures the cost of the physical media will be kept to a minimum even with industrial versions of Ethernet cables and switches. Once the commercial communication network changes from Ethernet to something new and better, the industry will follow. But, only at its own pace when it is deemed reliable.