The importance of material selection when handling corrosives.
Vanton
10/08/2018
When it comes to dealing with caustic chemicals, not all pumping technology is created equal. If a system is going to last, the materials of construction must be compatible with the pumped media, or corrosion will quickly become an issue. System design is also a consideration. Systems with many wear parts are sometimes less suited to harsh conditions than other options with fewer individual components. Below are two examples of facilities upgrading to purpose-built technologies in chemical applications.
Going Sealless in Scrubber Towers
A Florida utility company has installed sealless, magnetically driven pumps to serve the scrubber towers in its odor control system. The waste treatment facility serves a population of approximately 200,000 residents and visitors who are sensitive to effluent disposal practices. Odor control must be given high priority. The facility is in an area with residences and commercial business on three of the four sides of the plant, so scrubbers being down for any length of time is not an option. Flow enters the facility through 36-inch pipes emanating from the two beach communities it serves. Pretreatment consists of screening to remove solids and grit, which are conveyed to a dumpster for off-site disposal. After pretreatment, the screened liquid flows directly to the effluent tank. Reuse water is filtered through deep-bed filters. Performance and reliability of the sophisticated scrubbing towers are critical to meet U.S. Environmental Protection Agency (EPA) odor control standards and to please the surrounding community.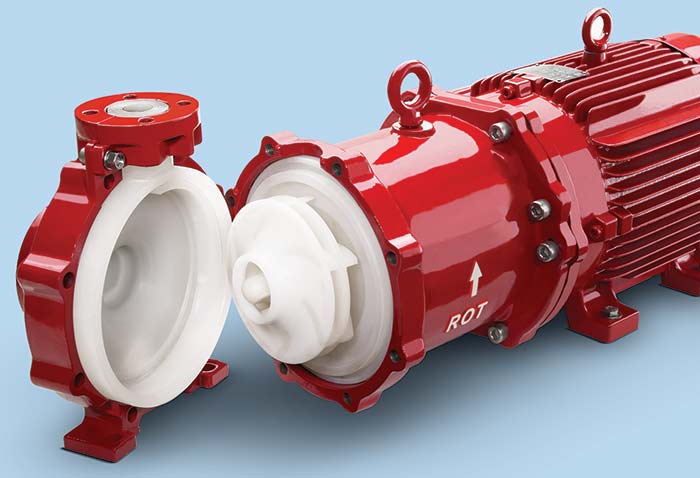
- The mag-drive are 3-inch by 2-inch flanged polypropylene pumps with 6-inch dynamically balanced keyed impellers, nonmetallic containment can assemblies, high performance rare earth magnets and no metal components in contact with the fluid.
- The casing, casing cover and impeller are made of precision molded, homogeneous polypropylene. The containment can is made of reinforced plastic. A fluoropolymer sleeve and end cap isolates the stainless steel shaft from the fluid.
- Extra-large stationary bearings of silicone carbide and rotating sleeve/thrust bearings of ultrapure alumina ceramic are locked into place by antirotation keys of polypropylene.
- Since the thermoplastic casings are protected by chemically resistant epoxy coated structural metal armor, these pumps can withstand the same nozzle loadings as metal pumps and their conformance to ANSI specifications permit for direct replacement of conventionally sealed centrifugal pumps.
Chemical System Eliminates Environmental Hazards
The designers of a petrochemical manufacturing plant were faced with the various problems associated with creating an environmentally safe, minimum maintenance and versatile neutralizing system for handling corrosive and hazardous acidic and alkaline chemical waste fluids under outdoor service. So they turned to specialists in the design and build of packaged and customized pH adjustment systems. The criteria for the system included these challenging fluid handling problems:- The flow of the system is an average flow of 50 gallons per minute (gpm) with a peak flow of 100 gpm.
- The pH values range from highly acidic to highly alkaline.
- Temperature fluctuates from 50 to 150 degrees F.
- Small suspended solids (salt precipitates) are present.