Fluid ends are used in well stimulation processes and are critical components of a well service pump, responsible for pressurizing the pumped proppant into the well. The design and materials used to make fluid ends for the well stimulation industry have changed very little since they became mainstream in the 1950s. Because of their strenuous life cycle, fluid ends are subjected to extreme stress, hit with high pressures, abrasive materials and corrosive fluids hour after hour, making them prone to failure. In today’s market, that is an expensive problem. Now, more than ever, fluid end manufacturers must address these fundamental flaws and improve materials and design in order to stay competitive and meet the needs and expectations of their customers.
Materials
Carbon steel was the original material used to make fluid ends for the well service industry. Although carbon steel performed well in application, the material had a fundamental weakness—corrosion. The life of the carbon steel fluid end was typically 250 to 450 hours. Anything beyond that would possibly be affected by stress corrosion cracking. This would then lead to fluid end fatigue failure under the cyclical pressure of the application.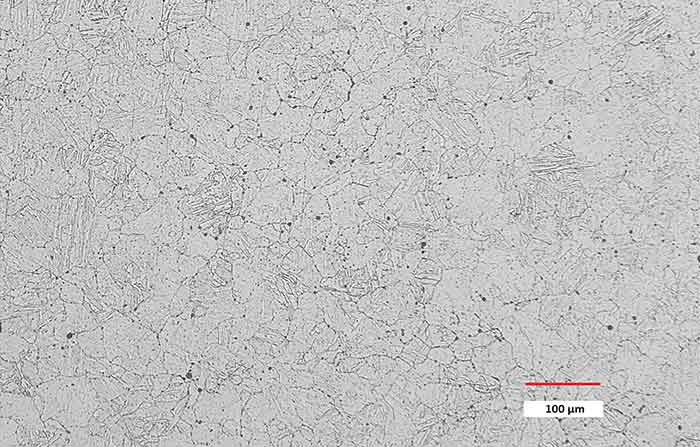
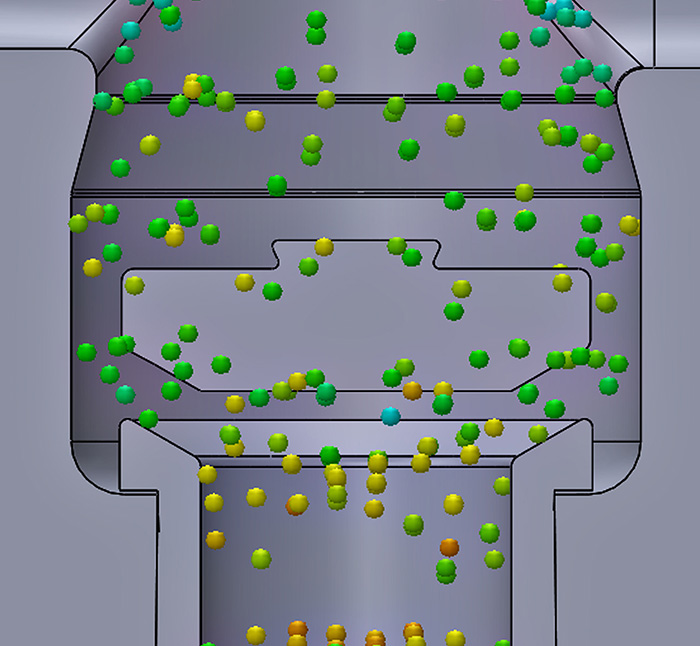
Design
It was in the 1950s that fracking as we know it today really began, with Allison aero engines and modified pumps. Although overall performance has dramatically changed since then, the basic design—specifically the geometry—of the fluid end has changed little. The fluid end design basically consists of a straight bore with a cross bore for the plunger, into which the valve and seat, retainers, and springs are assembled, essentially becoming a series of straight bores with restrictions. With only a few minor design changes since inception, most probably wonder: “Why change what has worked for so long?” The answer is simple: in order to meet the needs and expectations for increased life and performance of the fluid end, design changes must be made.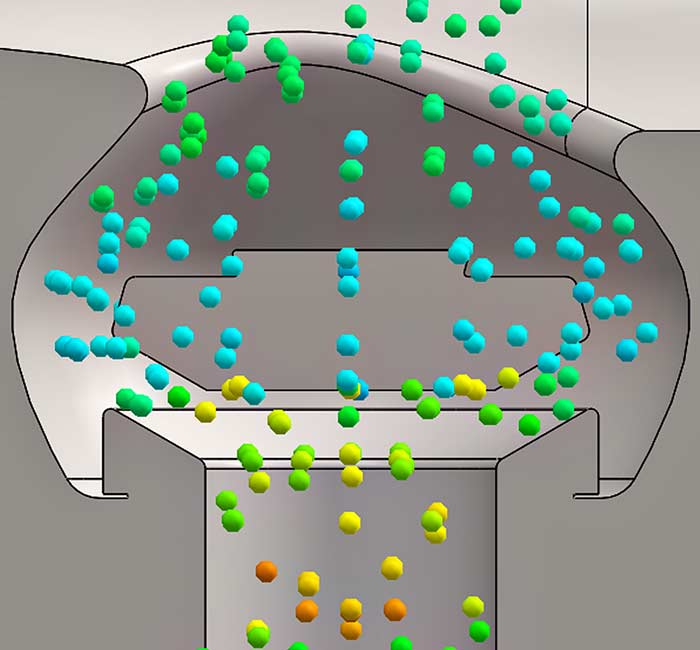