Each year, billions of dollars are spent on pumps used to introduce raw materials into various production processes or transfer liquids for storage or shipment to end users. Most pumps in service today feature mechanical seals, which are widely regarded to be the weakest point in the pumping system. More than 85 percent of pump repairs typically start with seal or bearing failures. For more hazardous applications, double mechanical seals help to prevent leaks, but they are expensive to maintain and repair. They often require a support system that needs a pressurized buffer tank to maintain higher pressure on the barrier fluid between the seal and the pump's stuffing box, plus piping and control systems that increase the size of the skid and the number of parts that must be maintained. Although double mechanical-sealed pumps should perform reliably for long periods of time, they inevitably require maintenance and eventual replacement. Replacing seals can be inconvenient, and the total costs add up in a number of ways. When measuring the costs of a leak in a chemical processing application, a good starting place is the lost productivity associated with service and repairs. Although pumps are often installed in pairs, taking a pump out for maintenance poses risks to a continuous production process, especially if the spare pump develops similar problems while the first pump is being serviced. Perhaps more important is the impact that leaks can have on employee health or environmental safety and the penalties, liabilities and remediation costs that come with chemical cleanup efforts.
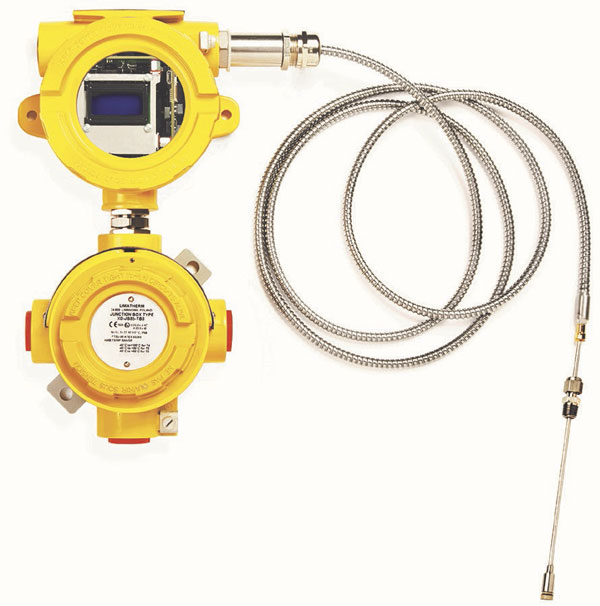
Environmental Protection & Safety
A $20 billion petrochemicals complex in Saudi Arabia requires hundreds of pumps to transport feedstocks into a massive tank farm. They also need other pumps to move the feedstocks into various chemical processing applications on a daily basis. Many of the process fluids being transferred are carcinogens (such as benzene) and other harsh products. Ensuring that site personnel, the surrounding community and the environment are not harmed is a priority for the plant operator. Over several decades, this company has gained vast experience with different types of pumps. This experience has taught them that the safest way to avoid seal leaks is simply to remove the seals, so sealless magnetic drive pumps have been incorporated into their systems for several transfer operationsWhen Reliability & Product Containment Are Non-Negotiable
A national oil company in the Middle East that also produces petrochemicals is one of the biggest adopters of sealless magnetic drive pumps in the region. Their daily activities rely on high-value chemicals, caustics, acids and solvents that are used in many production processes. While the chemicals used are critical to the production process, they are dangerous and potentially life-threatening to site personnel if not handled properly. For this reason, companies mandate that pumps withstand highly dangerous substances with zero leakage. Some applications span the full hydrocarbon chain, posing different challenges to pump seals. Sealless magnetic drive pumps have been able to overcome these issues through a containment shell design that vastly increases the pump's reliability. Previous containment shells were initially made of metal, but new technologies enhance the benefits of sealless magnetic drive pumps. One containment shell eliminates magnetic losses and heating of the process fluid. This facilitates greater efficiency with reduced power consumption required by the motor. The latest containment shells are engineered from proprietary materials that were initially developed for military aircraft construction. This nonmetallic composite material offers a range of benefits such as high tensile strength and temperature ranges from minus 100 C to 120 C. Resistance to a wide range of chemicals, resistance to thermal shock, as well as the elimination of eddy current heating and any resulting vaporization of the product in the rear of the pump. As a result, these containment shells can endure the rigors of a wide range of process applications.Detecting & Preventing Pump Failures
New sensing and monitoring technology used in sealless magnetic drive pumps helps operators prevent pump failures by identifying them before they happen. One device uses ultrasonic technology to monitor the process liquids that lubricate the bearings in the sealless magnetic drive pump, ensuring they remain vapor-free. If the gas is detected in the process fluids, the technology can alert engineers in time to take remedial action before the pump runs dry and damages the internal bearings. An intuitive user interface enables engineers to view and analyze recorded data.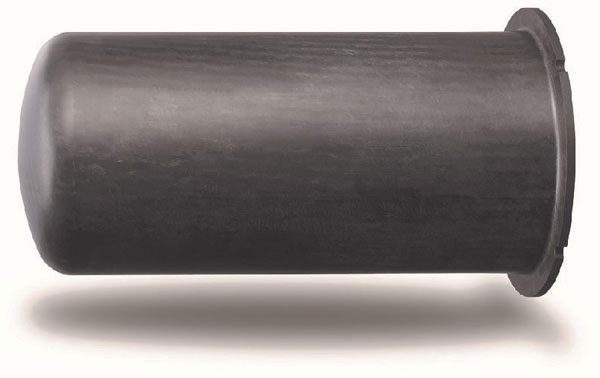