HI Pump FAQs
05/19/2016
Q. When is a metering pump used in a water or wastewater treatment plant? A. Specialized feed systems supply chemicals for various stages in water or wastewater treatment. The process requires optimal synthesis of new biological growth, so the addition of chemicals may be required to maintain a favorable growth environment. It is also important to maintain the pH of the wastewater in the process and sufficient alkalinity to provide for this operating pH range.
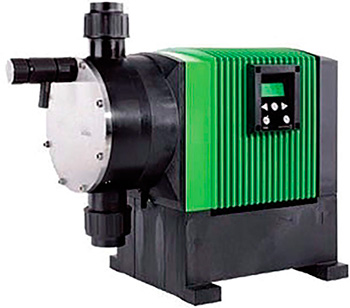
- functional testing of production units
- mechanical integrity test at rated speed and specified pressure
- rate of flow and mechanical integrity at rated speed and specified pressure
- verification of performance to the manufacturer's specifications
- steady-state accuracy
- linearity
- repeatability
- net positive suction head or net positive inlet pressure
- Factory or purchaser furnished driver
- Drive motor of proper voltage or appropriate design to operate metering pump
- Safety relief valve to protect the pump from overpressure
- Closed tank or open sump, properly sized for the pump being tested
- A discharge pressure gauge suitable for measuring not more than two times the complete range of pressures being tested, located as close as possible downstream of or near the pulsation dampener
- If required, dampening devices, such as pulsation dampeners, needle valves or capillary tubes, may be used to dampen out the pressure pulsations at the discharge pressure gauge.
- For variable speed applications, a means for measuring input speed to the pump should be provided and should be suitable for measuring the complete range of speed over the turndown range.
- A means for measuring pump rate of flow in liters/hour (gallons/hour) or other agreed-upon units
See other HI Pump FAQs articles here.