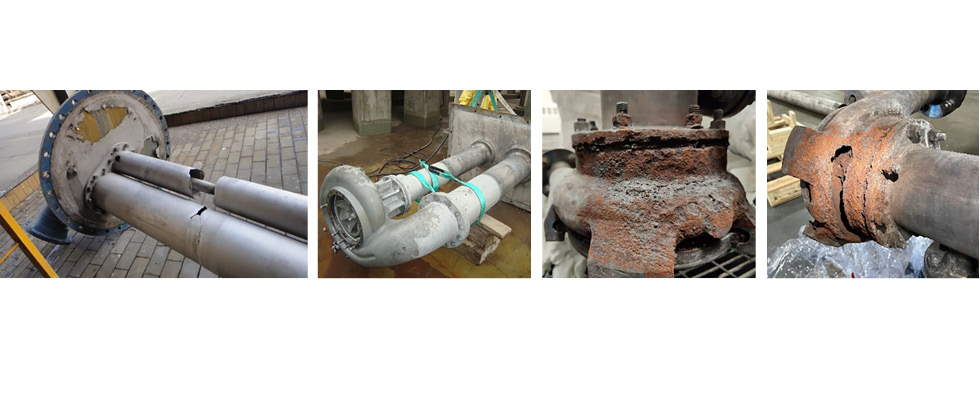
When selecting a type of pump for pumping hazardous liquids, many questions must be asked about the system in which the pump will be operating in. There must be a complete understanding of the chemistry of the liquids, operating temperatures and associated risks from the interaction of contaminants, vapors, corrosion, leaks and possible freeze-ups.
This article will discuss centrifugal vertical in-tank pumps (American Petroleum Institute [API] VS-1, VS-4 and VS-5) and horizontal (API OH1, OH2) pumps. It will also discuss vertical and horizontal mag-drive and canned motor pumps.
Pumping hazardous liquids will be defined as high temperature liquids such as molten salt, sulfur, sodium, highly corrosive acids such as sulfuric or hydrofluoric and flammable or toxic liquids such as phosgene and phosphorus. Keep in mind there are many low-temperature hazardous liquids that should follow the guidelines discussed in this article.
Shaft sealing on both vertical and horizontal pumps and flange sealing of mounting plates, the discharge flange for vertical pumps and the suction and discharge flanges for horizontal pumps will be the most critical areas of the pumps in preventing leaks of hazardous fluids or vapors.
High temperature hazardous fluids that solidify at lower temperatures must drain back to the tank revivor when the pump is shut down for any reason. Freeze-ups in the piping, heat exchangers and/or valves can lead to a dangerous situation.
Buildup of reactive material from contaminates formed within a process can cause explosions within the system. It is critical to understand any changes to the chemistry of the hazardous liquid being pumped.
It is critical to have a baseline analysis of the fluid chemistry when starting the system with hazardous fluids. Monitoring the chemistry overtime will prevent changes that could cause accelerating in corrosion or that could cause an explosion. Cross contamination of the fluid’s chemistry with air, water or another chemical can cause complete system failures.
When working with molten salt, sodium and molten sulfur, understanding the melting point, solidification points, thermal conductivities, high specific heat, high boiling points and viscosities will help prevent freeze-ups and deadheading of the system. Horizontal pumps are not designed to operate at a deadhead or shut-off condition, though there are some vertical cantilever pumps designed to operate for a short period of time at deadhead.
Understanding the maximum operating temperatures before a breakdown of the chemistry occurs is critical, as hazardous gases or byproducts can form.
Selecting a vertical pump for in-tank applications presents less risks associated with deadheading if there is a failed valve or freeze-up in the system. Most vertical pumps (API VS-5 and VS-4) are capable of running at deadhead for a short period of time. The bypass area of the volute is a built-in pressure relief feature, and the shaft sealing system does not contact the hazardous liquid.
Selecting a horizontal pump has more risks associated with its installation and operation. The shaft sealing system presents the highest risk area for leakage. Mechanical seals are used quite often, but care must be taken when selecting a seal design. If zero leakage is required, then users should consider using a mag-drive or canned motor pump design.
The compatibility of material used for components within a pump handling hazardous liquids is critical. In the production of ammonia nitrates (AN), this reaction between AN and copper brass can lead to the formation of a complex salt known as tetraamminecopper(II) nitrate (TACN), where any contact between TACN and AN can lead to AN becoming highly unstable. This can result in a higher sensitivity to mechanical and thermal stimuli, presenting significant explosive properties. The cages of the ball bearings used in the pump must be steel and not a brass- or copper-based alloy.
The compatibility of the materials of construction and forms of materials used in the pump must be designed for the different pumpages, environments and operating conditions they will be used for. Highly corrosive liquids can destroy a pump in months.
Choosing the right type of materials is critical in extending the life span of a pump. There are many options in plastics, metals, specialty alloys and ceramics that can be used for hazardous liquids.
Pump mounting flanges can be sealed using dual filled spiral wound gaskets or metal rings in ring type joint (RTJ) flanges. Sealing of the mounting flange requires the correct fastener system to be used. The type and design of the bolts, studs, expansion sleeves, nuts and locking systems must work together to seal against vapors or liquids leaking from the vessels.
There are several shaft sealing options for vertical pumps, which include standard packing box designs, combination labyrinth seal and packing box designs and mechanical seals of several types.
Depending on the application, single and double mechanical seals are used to prevent leakage. Barrier fluid and gases must be compatible with the liquids being pumped.
On high temperature systems, additional cooling chambers and heat fans may be incorporated into the design to reduce the heat migration up the shaft.
Mag-drive pumps and canned motor pumps are another zero-leakage option for hazardous liquids. When dealing with hazardous vapors, these options should be evaluated first. Mag-drive pumps are available in vertical and horizontal designs from several of the major pump OEMs.
Maintenance of pumps handling hazardous liquids falls into two categories: in the field or in a maintenance shop. It is critical the proper personal protective equipment (PPE) is worn in either category. Pumps handling highly corrosive acids must be cleaned properly to remove any residue that can cause burns to maintenance personnel.
Proper ventilation is critical when working on pumps handling hazardous fluid. Off-gassing of very deadly gases and vapors can come from the tanks and pits where the pumps are installed. Disassembly procedures using heat can also generate toxic fumes that can be deadly to personnel.
When dealing with extremely high-temperature liquids, fire containment must be considered for where the pumps are installed. The area must be free of combustible materials both on the ground and above the pump. The overhead piping and electrical cables above the pump can be damaged from fire.
Leak containment is critical to prevent plant personnel from coming into contact with the hazardous liquids. Drip pans, spray shields and insulation blanks are used to contain and control where the liquids can flow to. Vapor and gas monitors are used to ensure the area is safe to work in.
In high-temperature applications, thermal expansion can be a problem with both vertical and horizontal pumps. Flange loads and forces on the piping can cause many leaks and fracturing of welds. Horizontal (API OH-2 centerline mounted) pumps are designed for high-temperature applications and work well.
Monitoring systems to ensure safe operating environments for personnel should include air monitoring, pressure and temperature sensors and daily or weekly inspection of equipment by video or plant personnel.
When pumping corrosive acids, high-temperature molten salts and metals and radioactive and dangerous chemicals, a well-designed monitoring system can allow operators to see problems developing.
Advanced computer monitoring systems with built-in interlocks and corrective reactions will ensure a safe operating hazardous pumping system.
Preventing catastrophic failures to equipment and health issues to plant personnel must be one of the highest priorities when evaluating pumping hazardous liquids.
It is the responsibility of the owner of the pumping equipment to develop an emergency response plan and training program for their employees in handling these highly corrosive, toxic and high-temperature liquids. Included in this plan should be evacuation routes and procedures, site security and control, decontamination procedures, safe distances and places of refuge, emergency alerts and responses and emergency medical treatment and first aid.
Finally, when selecting a pump OEM, be sure they understand all the hazards associated with the system. A small misunderstanding can lead to catastrophic results like loss of life, production losses and a total shut down of a facility. Be sure to conduct failure mode and effects analysis (FMEA)/hazard and operability (HAZOP) reviews of the complete system and individual components. Consider using outside consultants that deal with hazardous fluids to participate in the FMEA/HAZOP review.